铝合金型材检测的重要性与核心要点
铝合金型材作为建筑、交通、电子等领域的重要材料,其质量直接影响工程安全性和使用寿命。随着工业技术升级和环保要求的提高,检测项目已从传统的物理性能扩展到更精细化的全流程管控。通过系统化检测,不仅能验证材料是否符合GB/T 5237、ASTM B221等标准要求,更能发现潜在缺陷,优化生产工艺,保障终端产品的结构稳定性与耐久性。
核心检测项目分类解析
1. 化学成分精准分析
采用直读光谱仪对6063、6061等牌号进行元素定量分析,确保镁(0.45-0.9%)、硅(0.2-0.6%)等关键元素含量符合YS/T 67标准。重点管控Fe、Cu等杂质元素超标导致的晶间腐蚀风险。
2. 力学性能多维测试
通过电子万能试验机进行拉伸试验,检测抗拉强度(≥160MPa)、规定非比例延伸强度(≥110MPa)及断后伸长率(≥8%)。配备显微硬度计进行维氏硬度检测(HV≥58),确保型材承载力达标。
3. 尺寸公差精密控制
使用三坐标测量仪检测型材截面尺寸误差(±0.1mm以内),激光跟踪仪验证直线度(≤1mm/m)。针对建筑幕墙用型材,额外检测45°角拼接精度及装配间隙。
4. 表面质量全维度检测
采用色差仪(ΔE≤1.5)和光泽度计(60°角测量)评估阳极氧化层质量。电涡流测厚仪检测膜厚(AA15级≥15μm),划格法测试附着力(0级为最佳)。对于喷粉型材,需进行2000小时中性盐雾试验。
5. 耐腐蚀性深度验证
执行GB/T 10125标准盐雾试验(3000小时无红锈),配合晶间腐蚀试验(硝酸汞法)。海洋环境用材需增加模拟海水循环腐蚀测试,评估点蚀深度(≤50μm)和腐蚀失重率。
6. 特殊性能定制化检测
轨道交通用型材需通过-40℃低温冲击试验(吸收能≥27J),光伏组件框架需进行2000小时氙灯老化测试(色差值ΔE≤3)。建筑用隔热型材需检测热导率(≤0.22W/m·K)及复合结构剪切强度(≥24MPa)。
质量控制体系构建要点
建议企业建立三级检测体系:原料入库快速筛查(XRF检测)、过程参数在线监控(红外测温)、成品全项检测(配备金相显微镜+能谱联用系统)。通过CMA/ 认证实验室进行年度型式检验,结合大数据分析实现质量预警,将缺陷率控制在0.3%以下。
随着新能源汽车轻量化与光伏产业爆发式增长,铝合金型材检测正朝着智能化、微型化方向发展。近红外在线检测系统与AI缺陷识别技术的应用,将推动检测效率提升40%以上,为高端制造提供更强质量保障。
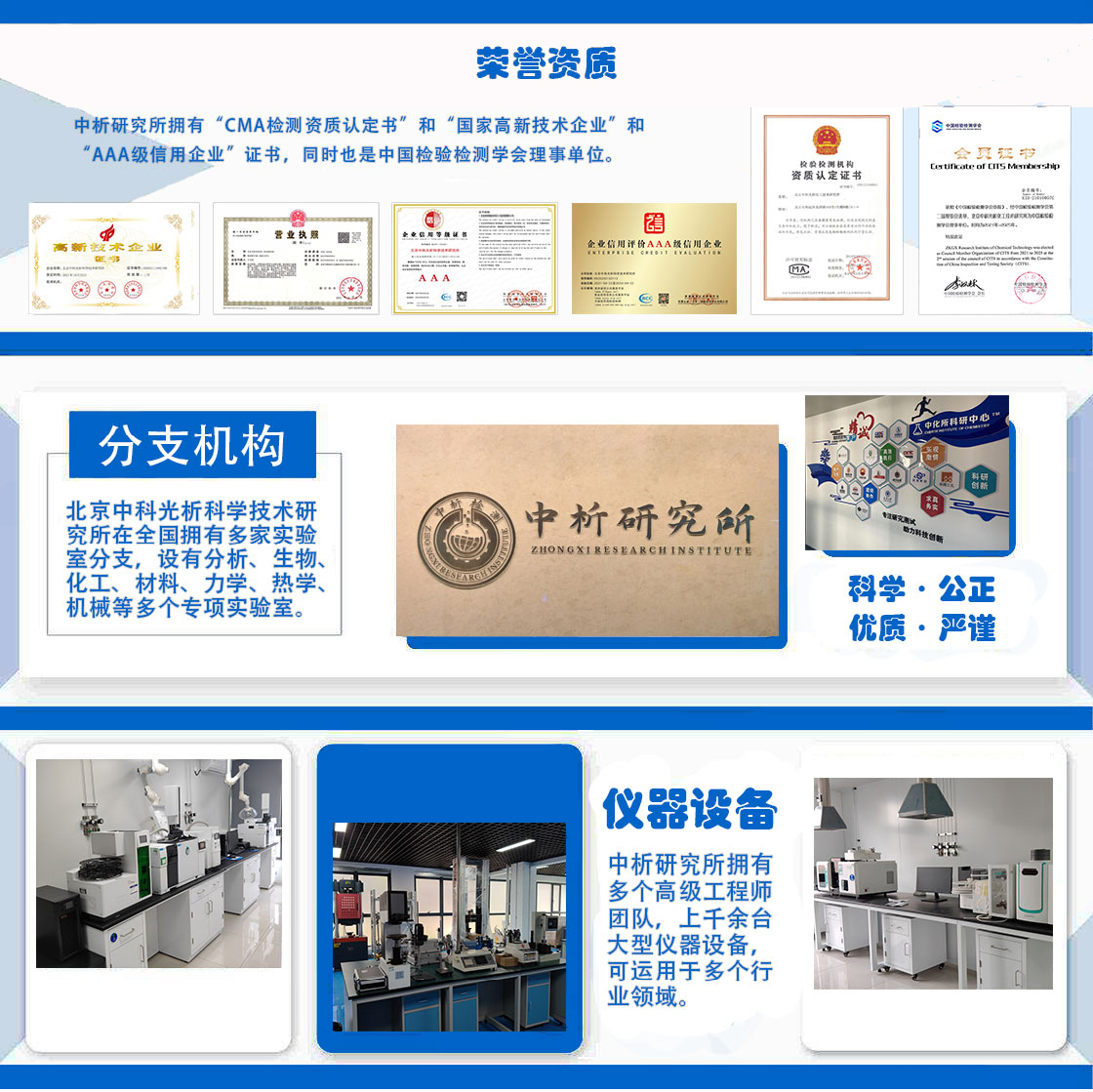
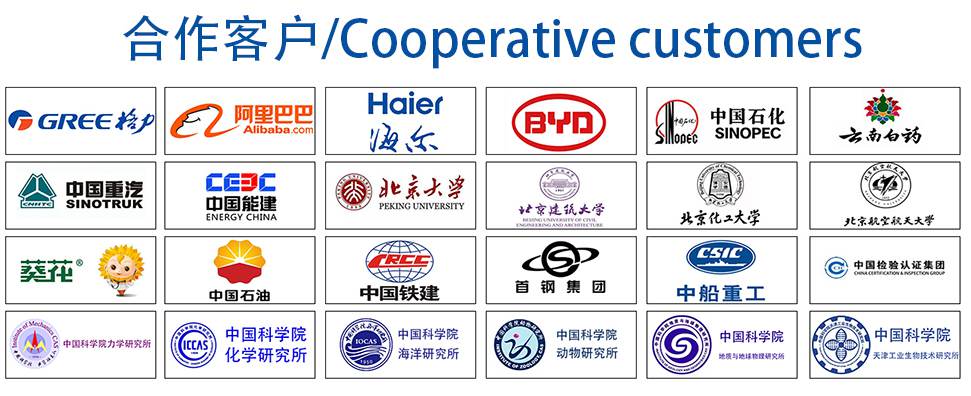