转向万向节总成检测的重要性与核心项目
转向万向节总成作为汽车转向系统的核心传动部件,承担着动力传递与方向调节的关键功能。其工作状态直接影响车辆操控安全性和转向灵活性。由于长期承受交变载荷、振动冲击及复杂路况的影响,万向节总成的磨损、变形、润滑失效等问题可能导致转向异响、虚位增大甚至断裂风险。通过系统化的检测流程,可有效预防转向系统突发故障,确保行车安全并延长总成使用寿命。
六大核心检测项目详解
1. 外观完整性检测
使用5倍放大镜配合工业内窥镜,重点检查万向节叉头、十字轴、轴承滚针的磨损划痕,排查壳体裂纹与锈蚀程度。需特别注意防尘罩是否存在龟裂老化,其破损将直接导致润滑脂泄漏。
2. 动态间隙测量
采用专用游隙检测仪,在轴向/径向方向施加标准测试载荷(通常≤500N),精确测量各方向自由间隙值。优质总成的轴向间隙应≤0.15mm,径向间隙≤0.05mm,超过0.3mm需立即更换。
3. 润滑效能评估
通过光谱分析仪检测润滑脂金属磨粒含量,配合黏度计测量润滑剂稠度变化。正常工况下,润滑脂含水量应<3%,Fe元素浓度需<150ppm,异常升高表明内部异常磨损。
4. 扭矩传递测试
在动态试验台上模拟实车工况,记录0-45°转角范围内的扭矩波动曲线。合格产品扭矩波动率应<15%,最大传递扭矩需达到设计值的120%以上,确保过载保护功能正常。
5. 材料强度验证
对关键部件进行洛氏硬度测试(HRC58-62为佳),配合金相显微镜分析热处理质量。进行10^7次循环疲劳试验,要求无裂纹扩展现象,确保材料耐久性达标。
6. 密封性能检测
在3Bar气压下进行气密性测试,保压30分钟压力降需<0.05Bar。同步实施IP67级防水试验,确保万向节内部完全隔绝水汽侵入。
智能检测技术应用趋势
当前主流厂商已采用三维激光扫描技术进行形位公差分析,配合MEMS传感器实时监测运行振动频谱。基于AI算法的智能诊断系统可自动比对历史数据,提前300小时预警潜在故障,检测效率较传统方式提升70%以上。
建议每行驶2万公里或经历极端路况后实施全面检测,及时更换失效部件。规范的检测流程可降低45%的转向系统故障率,是保障行车安全的关键技术措施。
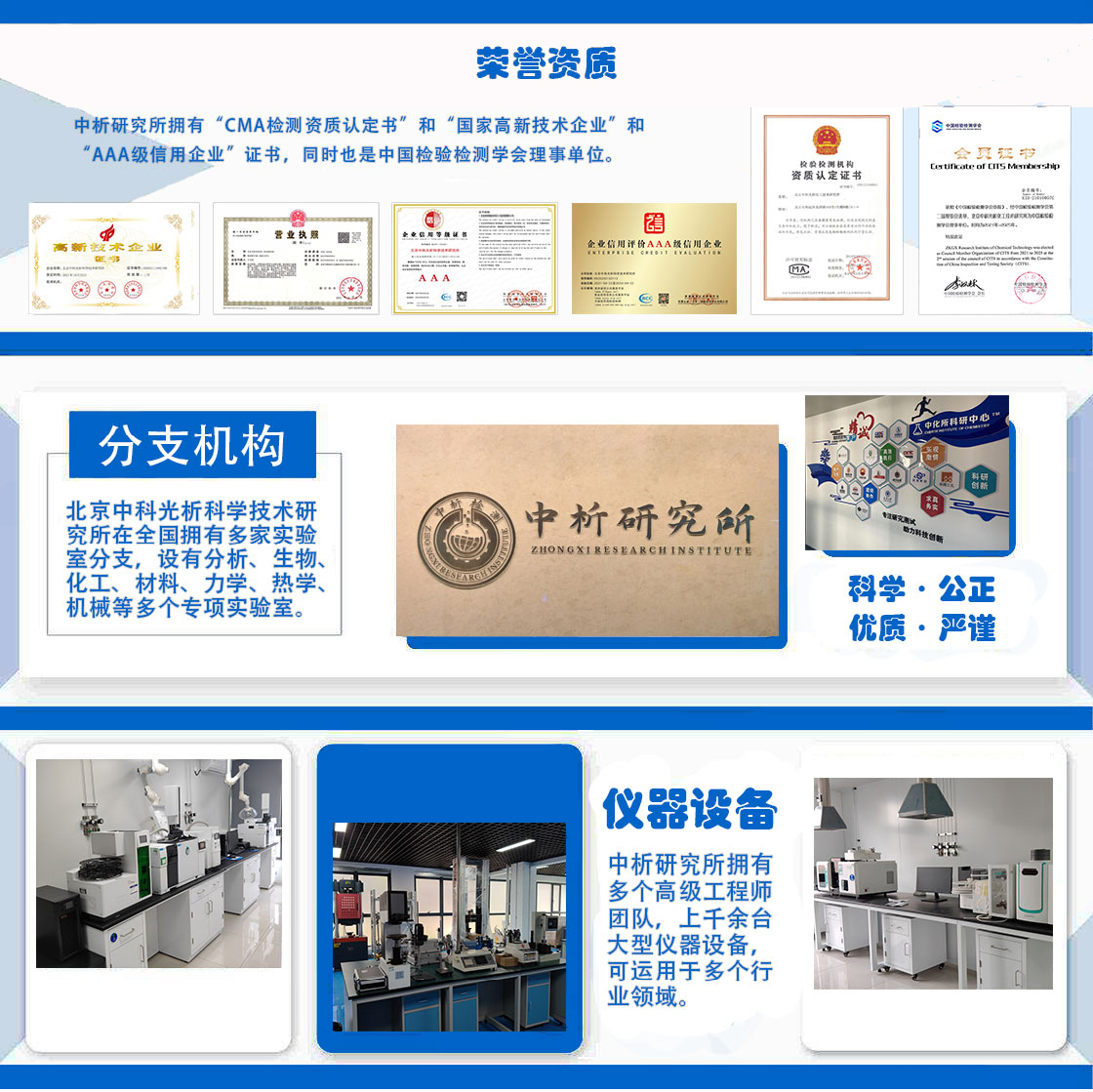
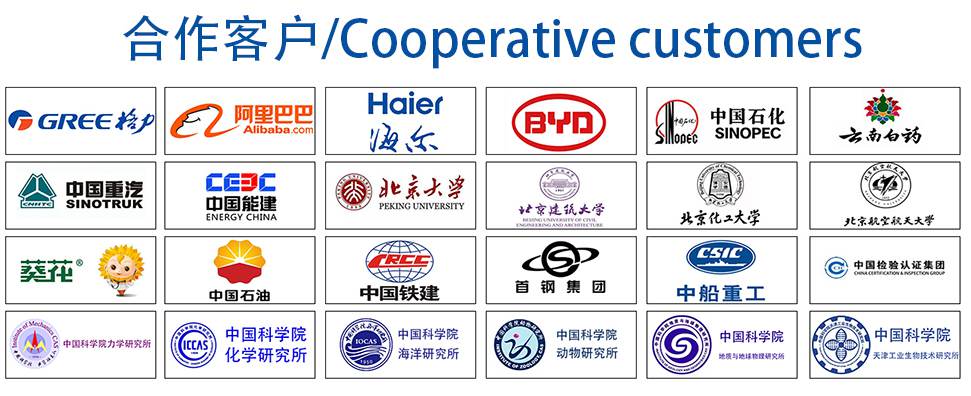