汽车零件 低压电线热变形试验检测
汽车零件低压电线热变形试验检测的重要性
在现代汽车工业中,低压电线是汽车电气系统的重要组成部分。这些电线在支持汽车正常运转的同时,也承担着信息传递的功能。汽车的高性能和可靠性要求其电线必须满足高标准的耐用性和安全性。尤其在高温环境中工作时,电线的热变形特性成为关键因素。因此,进行低压电线热变形试验检测是确保汽车可靠性和安全性的重要步骤。
低压电线热变形的基本原理
低压电线的热变形是指在高温环境下,电线发生形变的现象。热变形可能导致电线表层绝缘材料的软化、变形甚至熔化,从而影响电线的正常功能,甚至引发短路等安全隐患。低压电线的热变形受材料的热稳定性、热膨胀系数以及环境温度的影响。因此,了解电线在高温条件下的行为及其临界温度是进行安全设计和材料选择的重要依据。
热变形试验检测的方法与过程
低压电线的热变形试验检测通常包括一系列规范的步骤,以确保试验结果的准确性和重复性。常用的检测方法包括热拉伸试验、热扭矩试验和热老化试验等。
热拉伸试验是通过在规定温度下施加拉力,以测量电线的拉伸强度和断裂延伸率。其目的是评估电线在高温下的力学性能,以及在这种状态下其承受外力的能力。
热扭矩试验是在设定的高温下对电线施加扭矩,评估其承受扭力的能力和对变形的抵抗能力。这一试验能模拟复杂工况下电线可能承受的综合应力情况,有助于发现电线材料在热应力环境下的弱点。
热老化试验将电线在一定的温度下保温一定时间,通过比较试验前后的力学性能以及电气性能,判断电线材料的热稳定性和耐久性。这一试验帮助预测电线在长期使用后的性能变化,为使用者提供使用寿命的参考。
低压电线热变形对汽车性能的影响
电线的热变形不仅影响电气系统的性能和安全性,还可能对汽车整体性能带来潜在风险。例如,热变形可能导致电缆的损坏和断裂,从而引发电气故障,影响发动机和其他系统的运转。如果这些故障出现在车辆行驶途中,不仅会导致车辆抛锚,还可能造成交通事故。
此外,汽车电子技术的广泛应用带来了更多的控制电路和传感器,这些部件都依赖于低压电线的信号传递能力。热变形可能导致信号传递失真或中断,影响车辆的智能控制功能以及自动驾驶系统的可靠性,从而对驾驶安全构成威胁。
如何改善低压电线的热变形性能
为了提高低压电线的热变形性能,汽车制造商和供应商可以采取多种方法。首先是选择热稳定性强的材料,例如采用新型高分子材料或添加抗老化剂来增加电线的耐热性能。其次是优化电线结构设计,比如增强绝缘层的厚度和强度,以提供更好的热屏蔽效果。
另外,制造工艺的改善也能提升电线的性能。比如,通过精确控制交联工艺,提高电线材料的均匀性和紧密性,使其在高温环境中的稳定性更好。最后,在电线的安装和使用过程中,合理布线和有效散热也是避免热变形的重要措施。
总结
低压电线的热变形试验检测对于汽车的安全性、可靠性和性能至关重要。通过系统的检测方法,制造商能够识别材料和设计的弱点,从而进行改进和优化。与此同时,通过不断的技术研发和工艺创新,汽车行业将持续提升低压电线的热变形性能,为车辆的安全和高效运行提供保障。
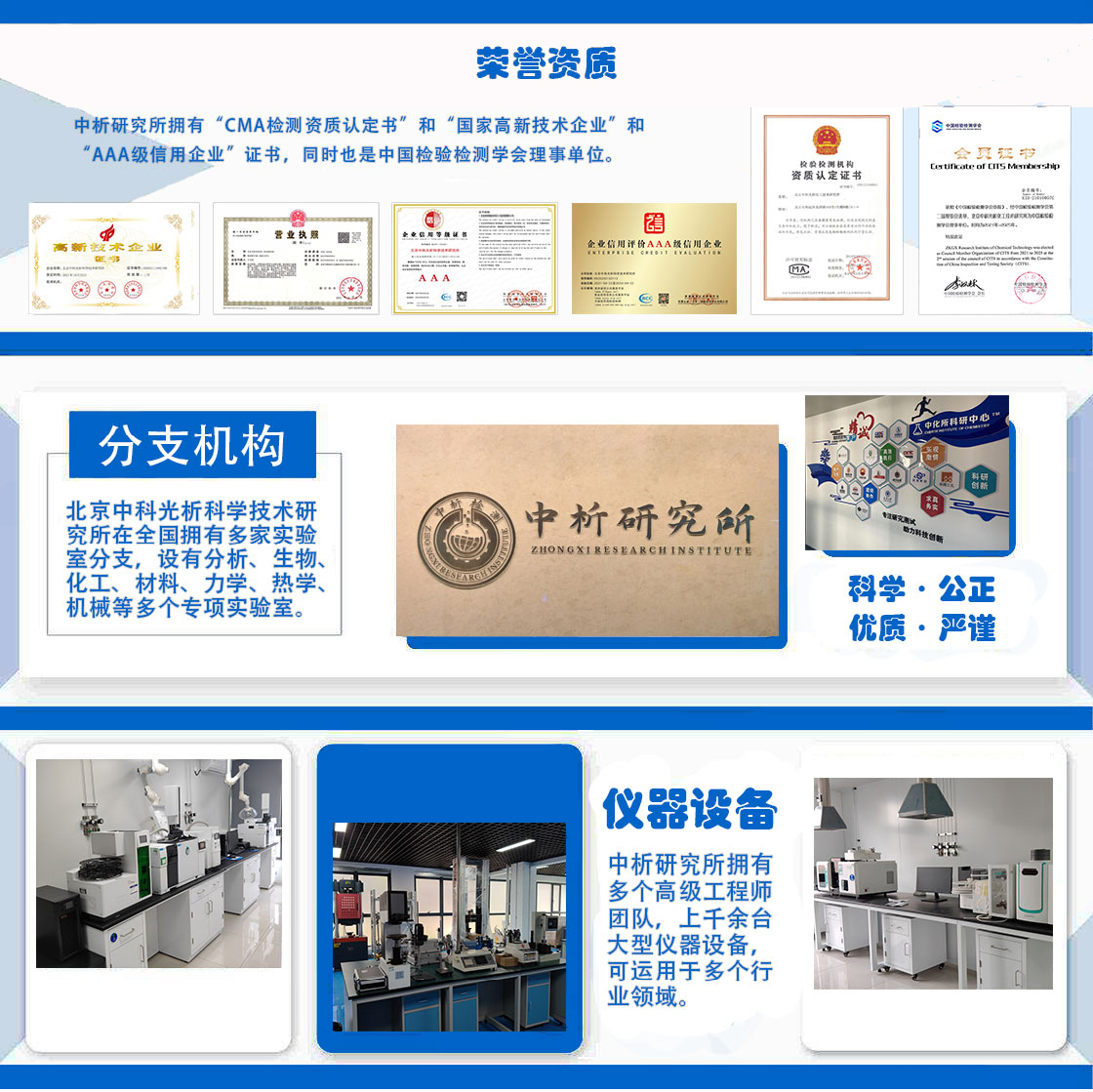
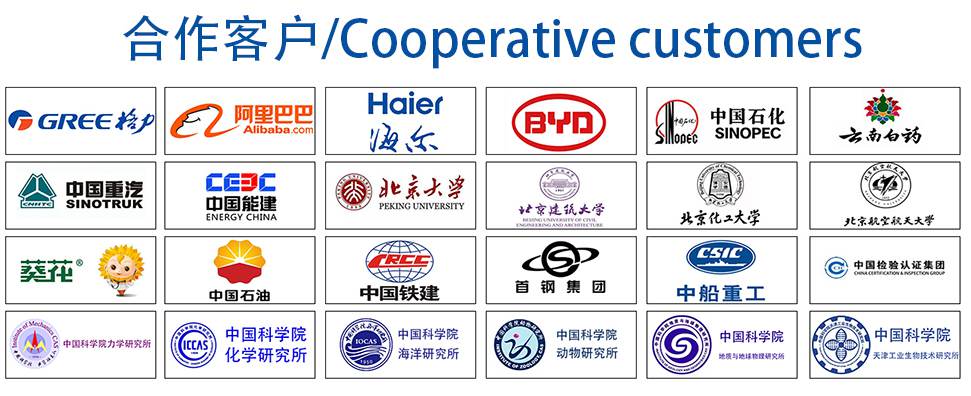