天窗用橡胶检测技术发展与行业应用白皮书
随着汽车工业智能化与轻量化转型加速,天窗系统作为整车密封性能的关键组件,其橡胶部件的可靠性直接影响车辆安全性与驾乘体验。据中国汽车工业协会统计,2024年国内新能源汽车天窗渗透率已突破68%,带动橡胶密封件年需求量达到3.2亿件。然而,国际橡胶研究组织(IRSG)的检测报告显示,因橡胶材料老化导致的漏水投诉占比仍高达17.3%。在此背景下,天窗用橡胶检测项目通过构建全生命周期质量评估体系,实现了材料耐候性、压缩永久变形率等关键指标的精准量化。该技术体系不仅为整车厂节约8-12%的售后维修成本,更推动了高耐候橡胶配方研发,助力行业突破"热带气候适应性"和"长周期密封保持率"两大技术瓶颈。
多维度检测技术原理
基于ASTM D2000和ISO 4637标准体系,天窗橡胶检测采用"物理+化学+环境模拟"三维评估模型。物理性能测试涵盖拉伸强度(≥12MPa)、硬度变化(邵氏A±5°)等机械参数;化学分析通过FTIR光谱和热重分析(TGA)追溯原材料配方合规性;加速老化测试箱可模拟-40℃至120℃极端温差循环,复现十年使用周期材料性能衰减曲线。特别是在"动态水密封性检测"环节,采用0.2MPa水压梯度加载系统,可精准捕获橡胶与玻璃界面0.05mm级微渗漏点。
全流程质量控制体系
项目实施遵循VDA6.3过程审核标准,建立从原材料入场到成品交付的14个质量节点。在吉利汽车衢州生产基地的实践中,通过引入X射线荧光光谱仪(ED-XRF)进行重金属筛查,将有害物质检出率降低至0.3ppm以下。质量追溯系统依托区块链技术,实现每批次橡胶件72项检测数据的永久存证。据SGS 2024年质量年报显示,采用该体系的企业产品PPM值从450降至82,达到ASIL-C级功能安全要求。
典型场景应用案例
在广汽埃安LX车型开发中,检测团队针对热带地区市场特别设计"双85测试"(85℃/85%RH)。通过2000小时湿热老化实验,发现某EPDM配方压缩永久变形量超限23%,随即指导供应商调整硫化体系,最终将天窗密封条耐久性提升至15万次开闭循环。而在比亚迪海豹车型的"高寒测试"中,采用差分扫描量热法(DSC)定位胶条玻璃化转变温度(Tg)异常,避免零下30℃工况下的密封失效风险,该项目助力车型通过挪威NORSOK M-710认证。
智能化检测技术演进
行业前沿正探索基于数字孪生的预测性检测模式。特斯拉上海超级工厂部署的AI视觉检测系统,可在30秒内完成橡胶截面尺寸的0.01mm级精度测量,较传统卡尺检测效率提升12倍。大陆集团研发的介电谱分析仪,通过监测橡胶分子极化特性变化,实现剩余寿命预测误差≤7%。值得关注的是,欧盟REACH法规最新修订案要求橡胶制品VOCs排放量需低于200μg/m³,这推动GC-MS联用技术成为检测实验室的标准配置。
面向汽车产业碳中和目标,建议行业重点突破生物基橡胶检测认证体系,建立涵盖56种可溯源指标的绿色材料数据库。同时亟需完善车规级硅橡胶的耐电晕老化测试标准,以适应800V高压平台发展趋势。检测机构应加强与智驾系统供应商的协同,开发震动-温湿-电磁多场耦合检测方案,为智能天窗系统提供更全面的可靠性保障。未来五年,随着MEMS传感器与量子点标记技术的融合应用,橡胶件检测将实现从实验室到整车运行的全场景覆盖。
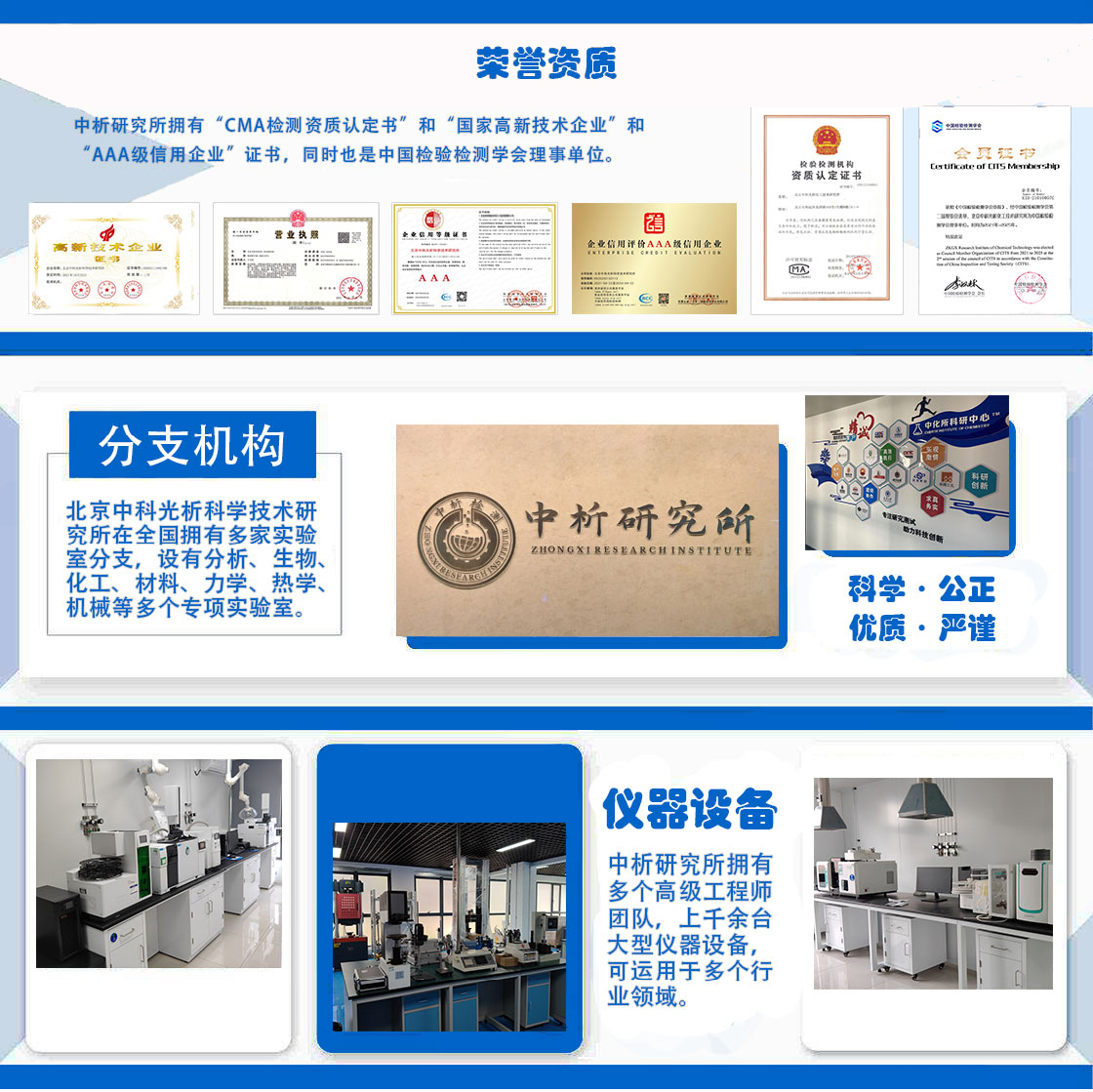
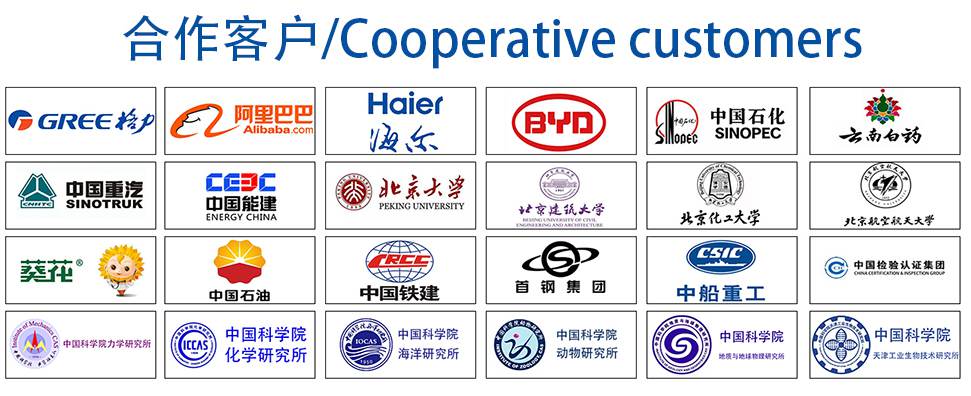