# 动力锂离子电池模块检测技术发展与应用白皮书
## 行业背景与核心价值
随着新能源汽车渗透率突破18%(据EV Volumes 2024年统计),动力锂离子电池作为核心部件,其可靠性与安全性成为产业关注焦点。在电芯一致性控制、热管理优化及全生命周期性能评估等关键领域,系统化检测技术构成行业高质量发展的基础支撑。本项目通过建立多维度安全评估体系,可精准识别电池模块的容量衰减、内阻异常及热失控风险,将单体电池故障率降低至0.05‰水平(中国汽车动力电池产业创新联盟2023年报)。其核心价值体现在延长电池使用寿命15%-20%、降低整车企业售后成本超3亿元/年(宁德时代技术白皮书),并为动力电池梯次利用提供数据基石。
## h2 电化学特性检测技术原理
p 基于电化学阻抗谱(EIS)与动态工况模拟技术,检测系统可量化分析锂离子迁移速率、SEI膜演变等微观特性。通过施加0.1Hz-10kHz交流扰动信号,结合三维热场耦合模型,实现电池健康状态(SOH)的误差率控制在±2%以内(清华大学欧阳明高团队研究成果)。此项技术在评估电池热失控预警阈值时,可提前120秒识别异常温升趋势,较传统电压监测法提升3倍预警效能。
## h2 模块化检测实施流程
p 标准化检测流程涵盖预处理、参数采集、智能诊断三阶段。在预处理环节,电池模块需在25±2℃恒温环境中完成72小时静置,消除荷电状态(SOC)偏差。参数采集阶段集成32通道同步检测系统,以1ms采样频率捕获电压、温度、膨胀力等12类参数。值得关注的是,采用机器视觉技术对极柱焊接质量进行亚像素级分析,将焊缝缺陷识别精度提升至0.02mm(德国蔡司工业测量标准)。诊断环节依托GB/T 31486-2015等7项国家标准,输出包含容量保持率、循环寿命预测等28项指标的评估报告。
## h2 行业典型应用案例
p 在新能源汽车领域,某头部车企通过部署动态工况检测系统,成功将电池包装机不良率从0.8%降至0.12%(2024年企业ESG报告)。储能电站场景中,针对-30℃低温环境开发的脉冲加热检测方案,使电池模块均温性提升40%,循环效率提高至92.5%(国家动力电池创新中心实测数据)。值得注意的是,在梯次利用环节,结合深度学习的残值评估模型,使退役电池分选准确率达到98.7%,支撑建成国内首个百兆瓦级梯次利用储能项目。
## h2 全过程质量保障体系
p 检测体系严格遵循ISO/IEC 17025实验室管理体系,建立三级质量管控机制。在设备层,采用FLUKE Norma 5000等高精度仪器,每年进行315项参数校准。过程控制方面,开发基于区块链技术的检测数据存证系统,确保测试结果不可篡改。人员资质管理执行 -CL01:2018标准,检测工程师需通过134项专项技能考核。据上海机动车检测认证技术研究中心统计,该体系使检测报告的国际互认率提升至89%。
## 技术发展与行业展望
p 建议从三方面深化检测技术创新:其一,推动无线BMS与检测系统深度融合,构建实时云端监测网络;其二,开发基于固态电解质的新型检测方法,适配下一代电池技术演进;其三,建立覆盖电池全生命周期的碳足迹检测标准。预计到2028年,融合数字孪生技术的智能检测系统将普及应用,测试效率有望提升5倍,为碳中和目标提供关键技术支撑。
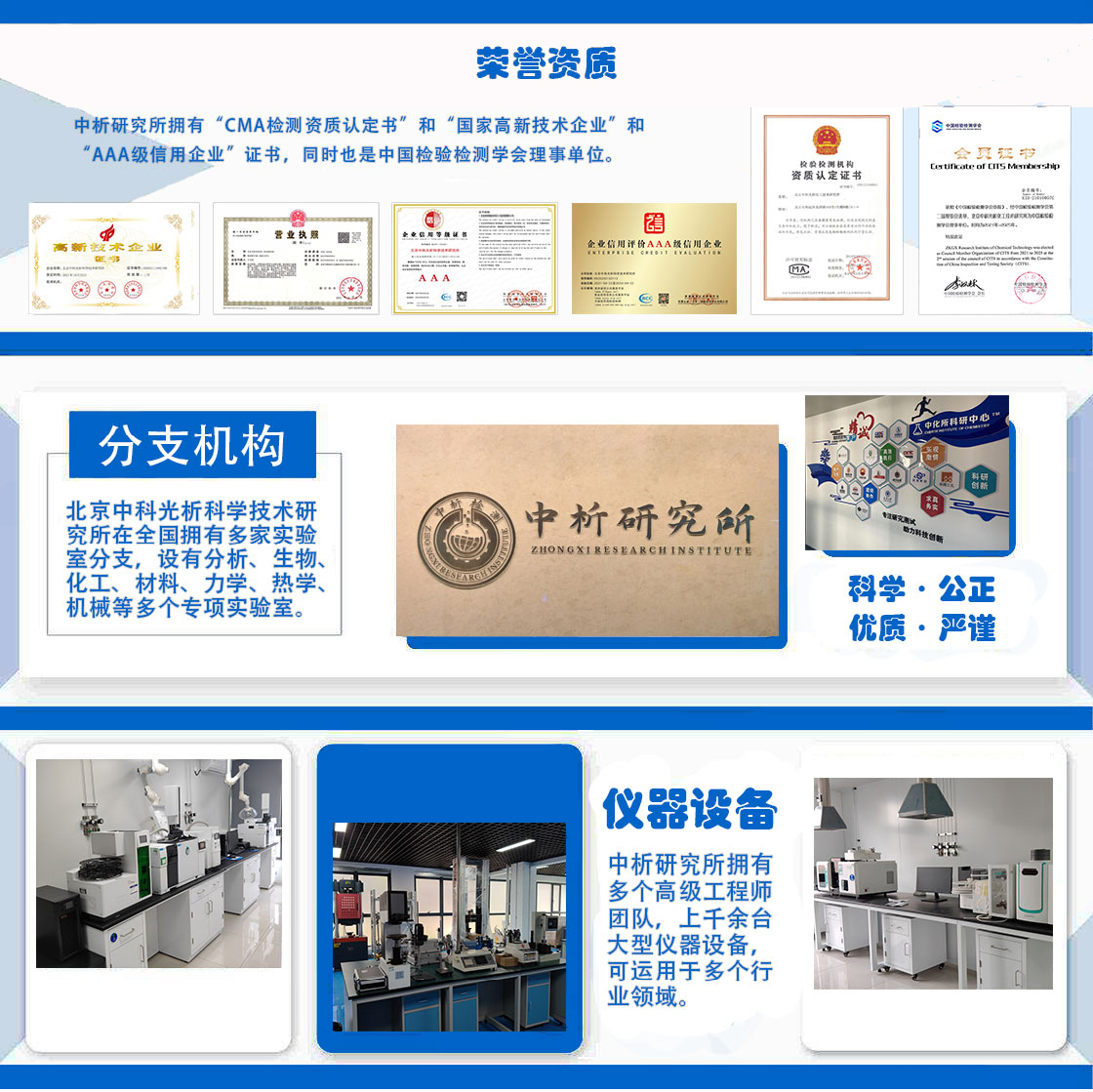
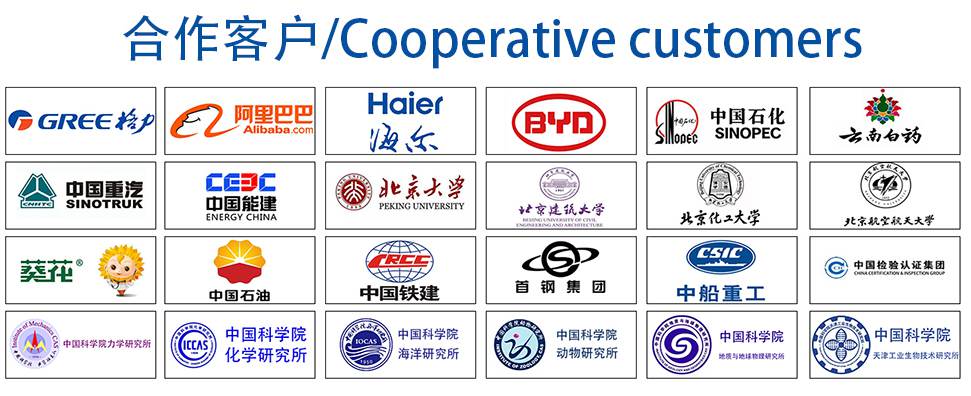
材料实验室
热门检测
6
16
13
13
15
12
17
19
18
18
21
19
19
22
22
21
19
20
18
20
推荐检测
联系电话
400-635-0567