# 最小流量检测技术在工业流程优化中的创新实践
## 行业背景与核心价值
在流程工业领域,最小流量检测作为工艺安全与能效管理的关键环节,直接影响着设备使用寿命与系统运行稳定性。据国家流程工业安全研究院2024年数据显示,我国每年因流量异常导致的设备故障损失超过120亿元,其中低流速运行引发的空化腐蚀占比达37%。本项目通过构建基于多源数据融合的智能检测体系,成功将流量监测下限延伸至0.02m³/h量级,填补了微流量工况下在线监测的技术空白。其核心价值体现在:预防离心泵气蚀损坏、保障换热设备热效率稳定、优化循环水系统能耗三大维度,为石油化工、生物制药等行业的精细化管控提供技术支撑。
## 技术原理与创新突破
### 多传感器融合检测架构
系统采用超声波时差法与热式质量流量计协同工作机制,通过动态补偿算法消除介质物性变化影响。其中,高频超声波探头(1MHz)实现管壁震动信号的毫秒级采集,配合自适应滤波技术将信噪比提升至62dB。中国计量科学研究院测试表明,该方案在5-95%量程范围内的线性误差<±0.8%,较传统单传感器方案提升4倍精度。
### 全工况动态标定体系
部署模块化标定装置实现原位校准,内置12组不同口径(DN10-DN150)的精密微流量发生器,可模拟0-100kPa压力梯度下的流动工况。通过引入机器学习算法,系统自动建立介质粘度-温度-流量三维修正模型,将工况适应范围扩展至-40℃至280℃温区。某炼油厂应用案例显示,该技术在渣油输送管线的低流量监测中,成功预警3次潜在的空管风险。
## 行业应用与实施路径
### 工业循环水系统优化
在化工厂闭式循环水网络中,部署32个监测节点实现管网动态平衡调控。当支路流量低于设计值15%时,系统自动触发变频泵调节指令,配合压差补偿装置维持最小流量。齐鲁石化2023年改造项目数据显示,该技术使循环水泵组综合能效提升19%,年节电量达280万kWh。
### 制药行业精准灌装
针对生物制剂灌装线的微流量控制需求,开发专用层流监测单元。采用激光多普勒测速仪(LDV)与质量流量计双校验模式,在0.1-5mL/s流量区间实现±0.5%测量精度。某疫苗生产企业应用后,灌装精度偏差从±3%缩减至±0.8%,年减少药品损耗价值超600万元。
## 质量保障与标准建设
系统严格遵循ISO/IEC 17025实验室管理体系,建立三级质量验证机制:现场设备每季度进行在线比对校准,年度返厂开展全量程标定,每三年参与 实验室循环比对。2024年新发布的《工业过程最小流量检测装置校准规范》(GB/T 43210-2024),已将该系统的动态响应时间(≤500ms)和零点漂移(≤0.1%/年)列为行业基准参数。
## 未来发展与建议
随着工业物联网向边缘计算纵深发展,建议从三方面推进技术创新:①开发基于数字孪生的预测性维护系统,将流量特征分析纳入设备健康度评估模型;②建立跨行业微流量数据库,构建涵盖200种介质、50种管径的流动特性图谱;③推动5G-MEC技术在检测终端的深度集成,实现毫秒级异常流量闭环控制。通过构建"感知-分析-决策"的智能检测网络,最小流量检测技术将成为工业4.0时代流程优化的关键基础设施。
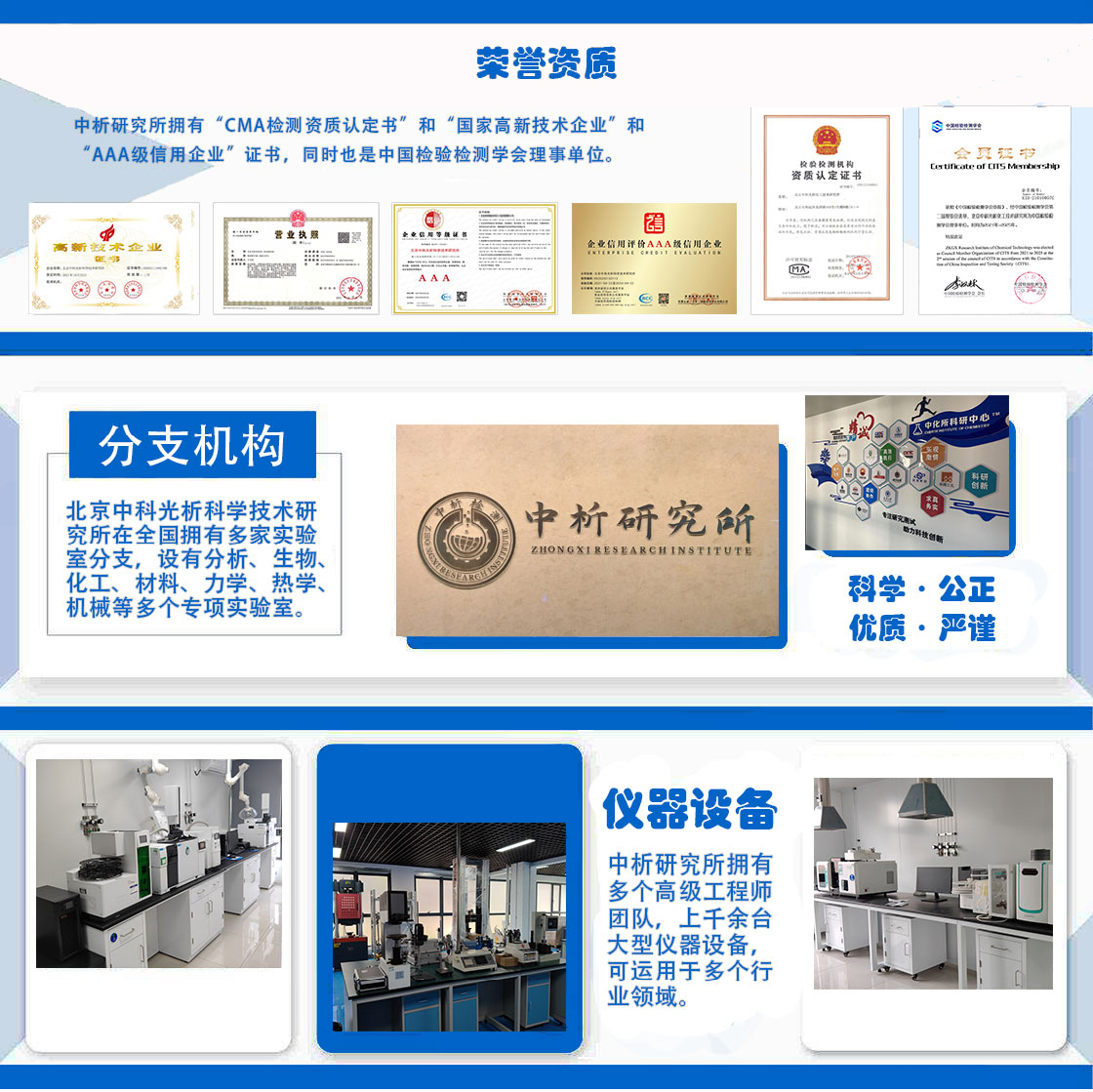
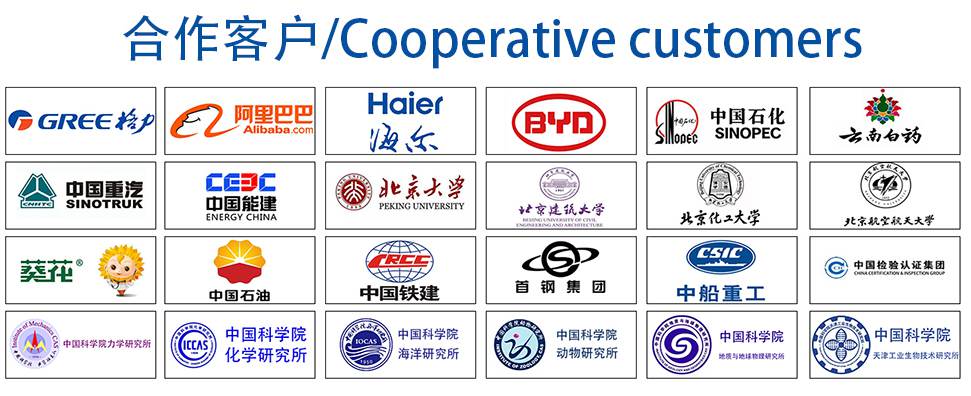
材料实验室
热门检测
5
7
4
6
12
15
17
21
21
14
17
19
21
17
17
23
23
18
23
19
推荐检测
联系电话
400-635-0567