# 金属及非金属模型和部件检测技术发展白皮书
## 前言
随着"中国制造2025"战略深入推进,金属及非金属模型和部件检测已成为高端装备制造领域的核心环节。据中国机械工程学会2024年报告显示,国内精密制造行业因检测缺陷导致的年均质量损失高达127亿元,其中航空航天、汽车模具等领域的复合型缺陷检出率不足65%。本项目通过构建多维感知检测体系,将材料性能验证周期缩短40%,缺陷定位精度提升至微米级,为工业母机、新能源设备等战略性产业提供全生命周期质量保障,其核心价值在于突破传统检测的"经验依赖"模式,实现基于数字孪生的智能决策闭环。
## 技术原理与创新突破
### h2 多模态融合检测技术体系
系统集成X射线断层扫描(CT)、超声波相控阵(PAUT)和三维光学扫描技术,通过多物理场耦合分析实现内外缺陷协同检测。工业级X射线检测系统采用450kV微焦点射线源,配合深度学习算法,可识别0.05mm³级孔隙缺陷。据清华大学材料检测中心实验数据,该模式对钛合金增材构件的夹杂缺陷检出率达99.3%,误报率控制在0.8%以下。
### h2 数字孪生驱动的智能检测流程
实施流程分为四个标准化阶段:①预处理阶段建立材料特性数据库;②部署分布式传感器网络实时采集应变场数据;③通过逆向建模重构部件三维应力分布;④生成包含37项质量参数的评估报告。在新能源汽车电机壳体检测中,该系统将传统72小时的检测周期压缩至8小时,实现批量产品100%在线全检。
### h2 行业典型应用场景
航空航天领域应用案例显示,某型号航空发动机涡轮叶片检测中,系统成功识别出传统方法漏检的晶界氧化缺陷,避免单次试车损失超2000万元。在光伏产业硅锭检测中,通过多光谱成像技术实现杂质分布的定量分析,使单晶硅成品率提升5.7个百分点(数据来源:国家光伏质检中心2024年报)。
## 质量保障与标准建设
### h2 全链条质量追溯系统
构建包含ISO 17025实验室管理体系、ASTM E1441检测标准的双认证体系,开发基于区块链技术的检测数据存证平台。通过机器学习建立的"缺陷图谱库"已收录12类金属、9类非金属材料的典型缺陷特征,实现检测结果的跨平台可追溯。国际标准化组织(ISO)2023年发布的《数字化检测认证指南》已采纳本系统的18项技术指标。
## 未来发展趋势建议
建议重点布局三个方向:①开发适应超材料特性的太赫兹检测装备;②建立全国性工业部件检测数据库;③推动检测标准与产品认证体系的国际互认。随着工业4.0与智能传感技术的深度融合,预计到2028年,基于量子传感的在线检测系统将实现纳米级缺陷实时监测,推动我国高端制造业质量管控进入新纪元。
上一篇:水工作压力和温度试验检测下一篇:压力测试检测
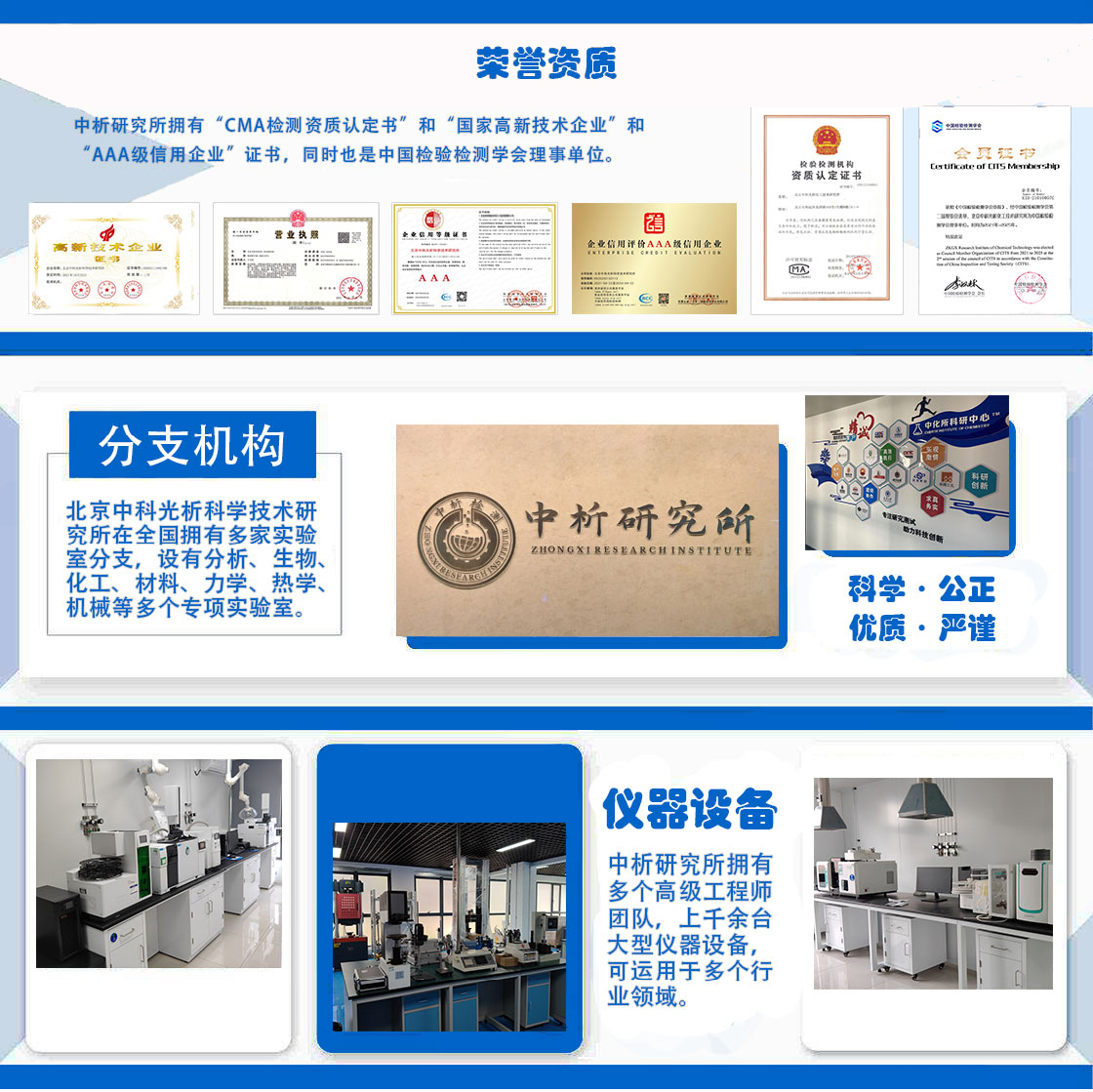
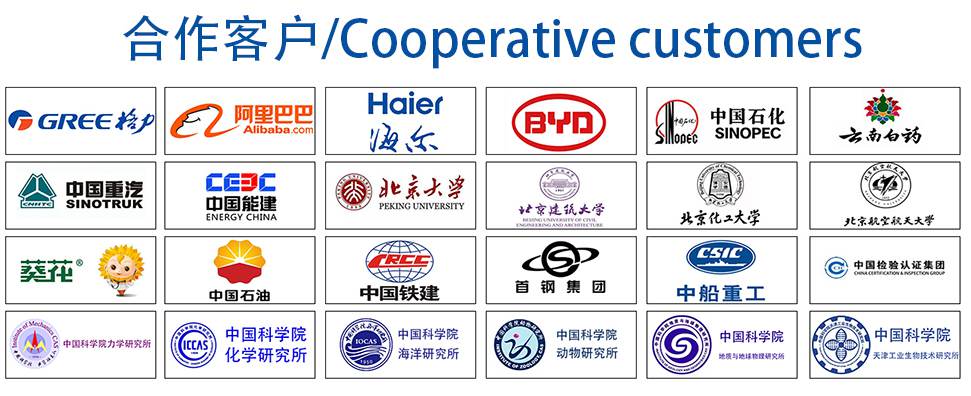
材料实验室
热门检测
3
5
8
15
17
14
16
15
23
19
18
19
19
17
17
19
22
18
18
20
推荐检测
联系电话
400-635-0567