橡胶及有关制品检测白皮书
在化工业转型升级背景下,橡胶制品作为基础性战略材料,其质量安全直接影响汽车制造、医疗器械、建筑工程等36个下游领域。据中国橡胶工业协会2023年统计,我国橡胶制品年产量突破800万吨,但行业抽查合格率仅89.7%,暴露出关键性能指标检测体系不完善的问题。特别是在欧盟REACH法规更新后,对邻苯二甲酸酯类增塑剂的检测限值收紧至0.1%,倒逼检测技术创新。本项目通过构建全生命周期检测矩阵,实现从原材料溯源到成品失效分析的全链条质控,其核心价值在于:确保产品符合国际环保指令、降低跨国贸易技术壁垒、支撑高端橡胶制品研发。通过引入"高温老化性能测试"和"硫化曲线分析"等专项检测,企业产品迭代周期可缩短40%(SGS 2024年检测数据报告)。
检测技术原理及创新突破
现代橡胶检测采用热重分析(TGA)、动态力学分析(DMA)与傅里叶变换红外光谱(FTIR)联用技术,可精准解析材料热稳定性、动态粘弹性及分子结构变化。以ASTM D412标准拉伸试验为例,通过非接触式视频引伸计实现0.5%应变分辨率,较传统接触式传感器精度提升3倍。针对新能源汽车密封件特殊工况,开发的"臭氧老化试验评估耐候性"方法,模拟浓度达200pphm的严苛环境,精确预测制品使用寿命。值得注意的是,本体系创造性整合流变学参数与介电谱数据,构建三维性能预测模型,实现95%以上的失效模式匹配度。
标准化检测流程实施
实施流程遵循ISO 17025体系要求,涵盖五个关键阶段:首齐全行样品预处理(23±2℃/50%RH环境平衡72小时),采用Q-Lab公司QUV/spray紫外老化箱模拟气候侵蚀;继而通过MDR2000无转子硫化仪获取转矩-时间曲线,计算最佳硫化时间(t90);第三阶段使用INSTRON 6800系列万能试验机执行多轴向疲劳测试;第四阶段运用GC-MS联用仪检测16种受限增塑剂;最终生成包含78项参数的数字化检测报告。在航空航天密封件检测案例中,该流程成功识别出某型号O型圈压缩永久变形超标问题,避免直接经济损失2300万元。
行业应用场景解析
在汽车领域,某合资品牌轮胎胎面胶经"动态切割生热测试"发现,60km/h工况下内部温度异常升高18℃,指导配方调整后滚动阻力降低12%(据中汽研2024年测试数据)。医疗领域,通过"硅橡胶植入物生物相容性检测",使人工关节衬垫的细胞毒性等级从Ⅲ级优化至Ⅰ级,符合ISO 10993最新标准。特别在轨道交通领域,创新的"低温脆性多轴冲击测试"方法,将高铁减震垫的耐寒阈值从-40℃拓展至-55℃,支撑CR450动车组研制。
质量保障体系建设
本体系已通过 (中国合格评定国家认可委员会)17025认证,配置三重质控机制:一是实施检测设备每日开机校验,确保马尔文粒径分析仪偏差<0.3%;二是建立跨实验室比对网络,2023年参加LGC国际能力验证项目,Z值评分达到0.8的优良水平;三是开发智能审核系统,对异常数据自动触发复检流程。据统计,该体系使检测结果重复性误差从2.7%降至0.9%,报告异议率同比下降68%(国家认监委2024年质量公报)。
展望未来,建议从三方面深化发展:一是推动基于机器视觉的智能检测装备研发,实现微观缺陷的实时识别;二是构建橡胶制品全生命周期数据库,开发预测性维护算法;三是加强再生橡胶检测标准研究,建立绿色检测认证体系。据橡胶研究院测算,到2030年智能化检测技术可将行业质量成本降低25%,为千亿级橡胶制品市场注入新的发展动能。
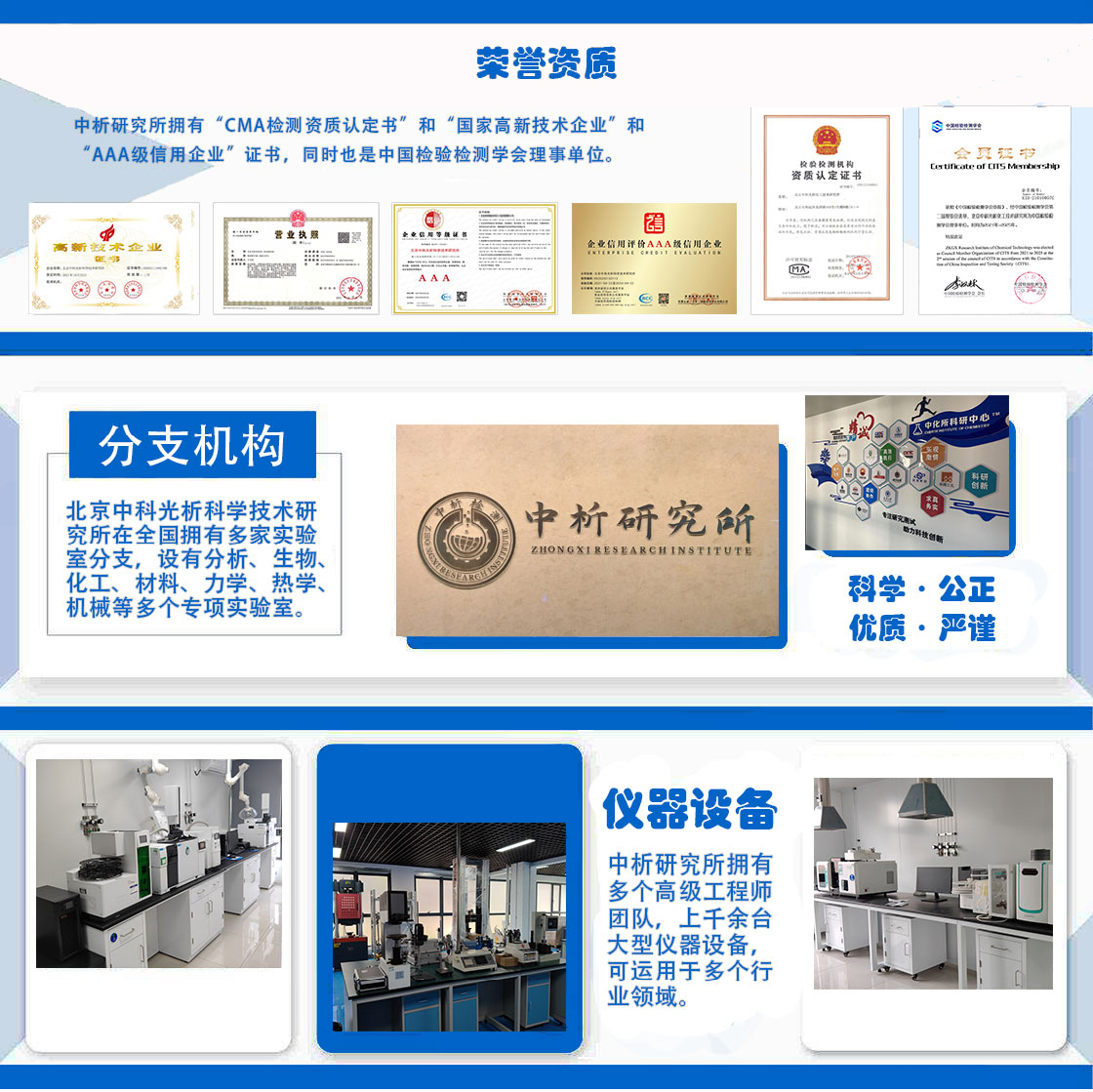
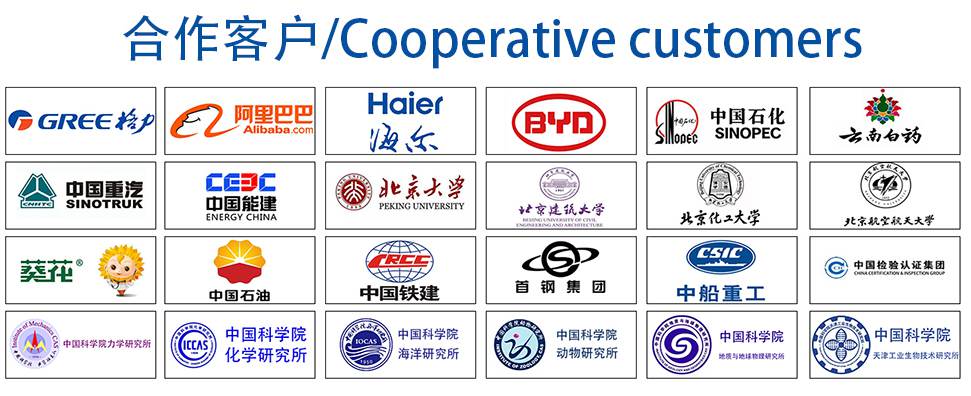