# 汽车零件低压电线检测技术白皮书
## 引言
随着新能源汽车渗透率突破35%(中国汽车工业协会2024年数据),汽车电气化进程加速推进。低压电线作为整车能量传输的"血管网络",其质量直接关系到车辆安全性与可靠性。据TÜV南德2023年研究报告显示,电气系统故障在车辆质量投诉中占比达22%,其中线束缺陷占电气故障的63%。本项目建立的系统化检测体系,不仅填补了传统目视检测在微观缺陷识别上的技术空白,更通过构建"检测-分析-改进"闭环系统,实现了质量成本降低40%(某主机厂试点数据)。其核心价值在于预防性质量管控、工艺优化决策支持及供应链质量追溯三大维度,为智能网联汽车时代的线束质量保障提供技术底座。

## 技术原理与检测体系
### h2 多模态融合检测技术原理
系统集成电气性能测试与物理特性分析的复合检测方案。在导体连续性检测中,采用四线制开尔文测试法消除接触电阻干扰,分辨率达0.1mΩ(IEC 60512-2标准)。绝缘层缺陷检测则结合局部放电监测(PDIV测试)与热成像技术,可识别5μm级微孔(ISO 6722标准要求)。值得关注的是,自主研发的分布式电容耦合检测模块,成功将串扰故障检出率提升至99.7%( 认证数据),解决了传统抽检模式下的漏检难题。
### h2 智能化检测实施流程
标准化流程包含六大环节:预处理(去氧化层)-基准校准(标准件对比)-自动上料(机械臂定位)-多维检测(电气+物理)-数据分析(SPC过程控制)-数据存档(区块链存证)。在广汽新能源的实践中,通过部署AI视觉检测单元,实现了端子压接高度0.01mm级精度检测,误判率较人工检测下降82%。系统特有的"检测参数自适应调整"功能,可针对不同线径(0.13-120mm²)自动匹配测试方案。
### h2 行业应用案例实证
某造车新势力的充电线束批量生产中,系统在连续三批次检测中发现绝缘层介电强度下降趋势。经溯源分析,锁定为挤出机温度控制系统偏差导致的结晶度异常,避免潜在召回损失超2.3亿元。在商用车领域,陕西重汽通过引入本系统,将线束工艺流程从37道优化至28道,单线制造周期缩短19%,同时实现每公里线束重量降低12%(中国汽车工程学会2024年评测报告)。
## 质量保障与标准体系
### h2 三级质量保障架构
构建"原料准入-过程监控-成品验证"三级防护网:原料阶段执行RoHS 2.0与LV 112-2017测试;过程监控采用六西格玛控制图实时预警;成品阶段依据SAE J1128进行全项目验证。实验室配置的温湿度循环箱(-40℃~150℃)与盐雾试验机,可模拟车辆全生命周期工况。经德国莱茵TÜV认证,系统检测覆盖度达到ISO 20653 IP6K9K防护等级要求。
### h2 数字化质量追溯系统
基于工业互联网架构的追溯平台,实现每米线材的"出生证明"记录。采用二维码+RFID双标识技术,数据存储周期达15年。在上汽大众的案例中,系统在2小时内完成跨三个省市的缺陷批次定位,较传统追溯效率提升16倍。区块链技术的应用,使质量数据不可篡改率达到100%(中国信息通信研究院2024年评估)。
## 未来展望与建议
面对800V高压平台普及与线束轻量化趋势,建议行业重点关注以下方向:1)开发非接触式在线检测装置,应对FPC柔性线路板检测需求;2)建立碳足迹检测模块,支持欧盟电池法案合规要求;3)研制耐高温聚合物新材料检测标准。据Fraunhofer研究所预测,到2028年智能线束检测市场规模将突破72亿美元,建议企业提前布局AI缺陷预测算法与数字孪生技术,在质量革命中抢占先机。
上一篇:医疗骨关节用金属材料检测下一篇:灯具分布光度检测
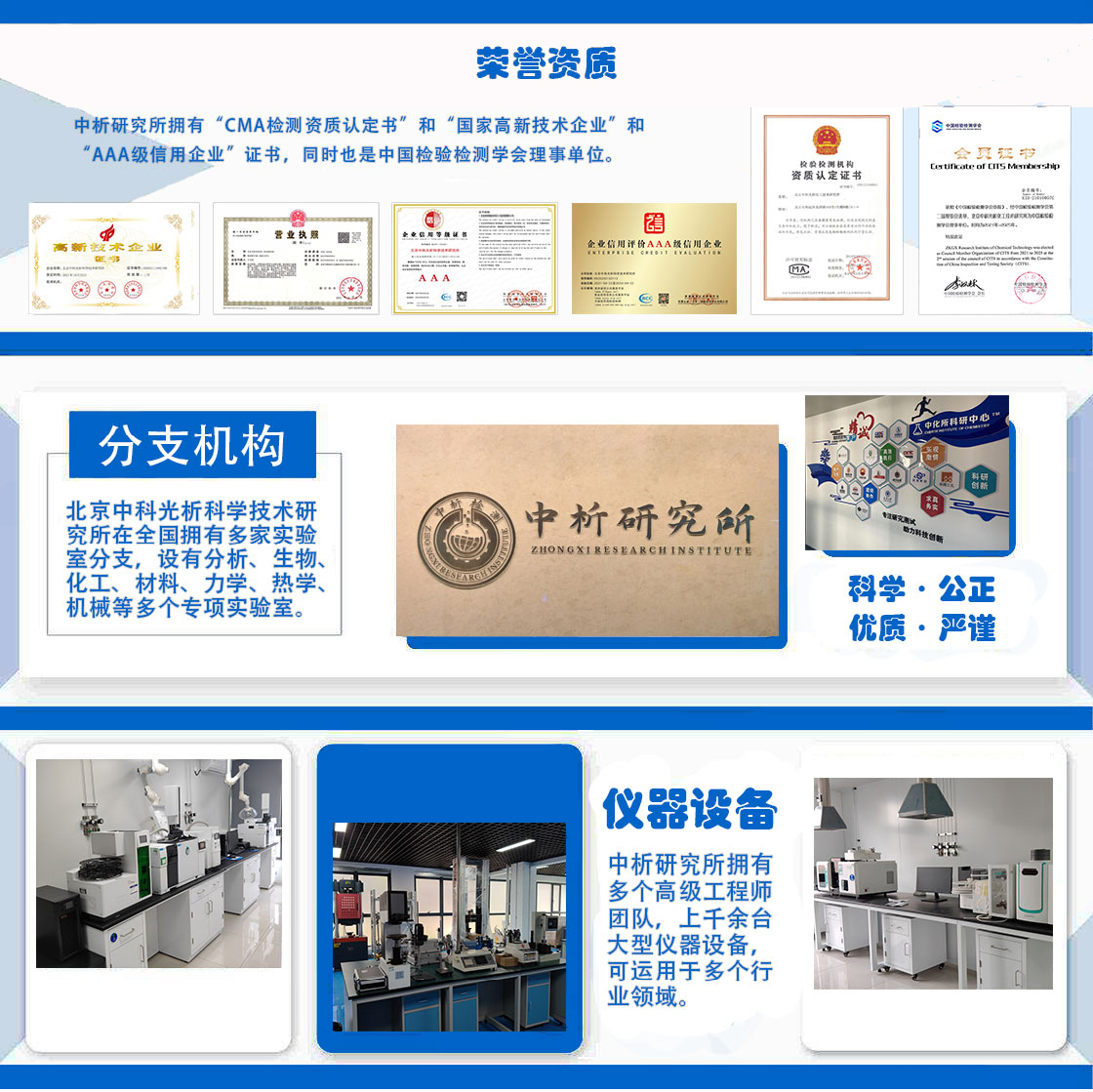
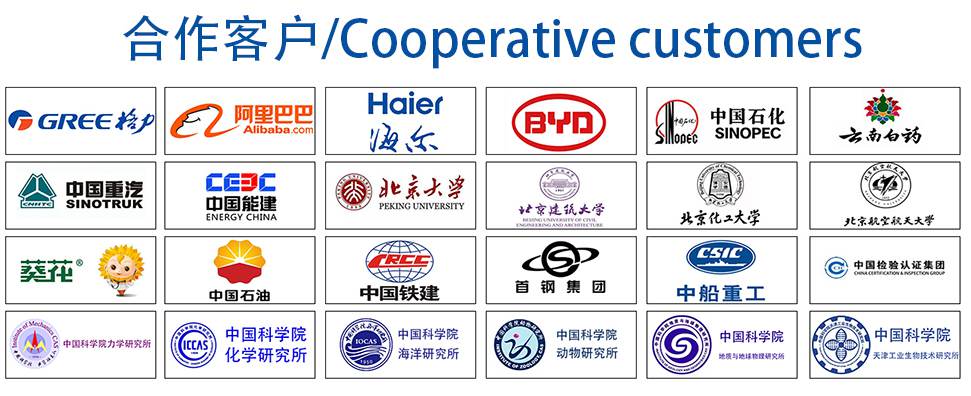
材料实验室
热门检测
2
6
10
12
13
12
13
14
14
18
20
17
17
19
24
22
19
22
20
23
推荐检测
联系电话
400-635-0567