# 馏分燃料(汽油、柴油)检测技术体系与应用前景
## 行业背景与核心价值
随着能源结构转型与环保政策趋严,馏分燃料的质量控制已成为石化行业的核心议题。据国家能源局2024年数据显示,我国车用汽柴油年消费量突破2.8亿吨,但市场流通燃料中仍有12%不符合现行国六B排放标准。在此背景下,精准的馏分燃料检测技术不仅能确保发动机高效运行,更可助力减少PM2.5前驱物排放,据生态环境部测算,提升燃油合格率1个百分点即可年减排氮氧化物3.7万吨。其核心价值体现在三方面:通过硫含量、芳烃组分等关键指标控制实现环境效益;依托十六烷值、馏程特性优化提升用能效率;基于金属杂质检测保障输配系统安全。
## 技术原理与检测体系
### 多维分析技术架构
现代馏分燃料检测采用"物性-组分-污染物"三维评价模型。气相色谱-质谱联用(GC-MS)可精准解析C8-C24烃类分布,红外光谱法实现硫、氮化合物快速筛查,激光诱导击穿光谱(LIBS)技术则专攻金属磨损微粒检测。针对柴油十六烷值快速测定这一行业痛点,基于近红外光谱的建模方法可将检测时间从传统发动机法的4小时缩短至15分钟,据中国石化研究院测试,其相对误差稳定在±1.5%以内。
### 全流程质量管控
从采样到报告输出的标准化流程包含五个关键节点:首先执行ASTM D4057规范的管线动态采样,接着通过三级过滤消除颗粒物干扰,实验室阶段运用ASTM D86标准方法测定馏程特性,最终结合MES系统实现数据溯源。值得注意的是,针对高硫原油加工产生的汽油产品,采用紫外荧光法(ASTM D5454)可将硫检出限降至0.5ppm,较传统库仑法灵敏度提升20倍。
## 行业应用与创新实践
### 场景化解决方案
在沿海保税油加注领域,基于便携式XRF设备的船用柴油硫含量快速筛查方案,成功将海关查验效率提升80%。某东部港区应用该技术后,2023年查处超标油品23批次,避免SOx排放760吨。而在炼化生产端,兰州某千万吨级炼厂引入在线近红外分析系统后,柴油十六烷值控制标准差从0.8降至0.3,每年减少品质过剩造成的成本损耗超3000万元。
### 质控体系升级
现行检测网络已构建三级质保机制:实验室内执行 认可的ISO/IEC 17025体系,区域中心实验室开展盲样比对,国家石油产品质量监督检验中心组织年度能力验证。2023年全国性比测数据显示,92#汽油辛烷值检测结果的实验室间差异已压缩至0.3个单位,较五年前提升45%的精度水平。
## 发展建议与未来展望
面对新能源汽车渗透率提升带来的检测需求变化,行业亟需在三个方向突破:开发适用于乙醇汽油的痕量腐蚀性物质检测方法,建立生物柴油调和燃料的快速鉴别体系,以及拓展航煤等特种馏分燃料的检测能力。建议依托工业互联网构建检测大数据平台,通过机器学习优化检测模型,同时推动ASTM与GB标准的深度融合,助力我国炼化产品参与国际竞争。预计至2030年,智能检测设备的市场渗透率将突破60%,推动行业检测成本降低30%以上。
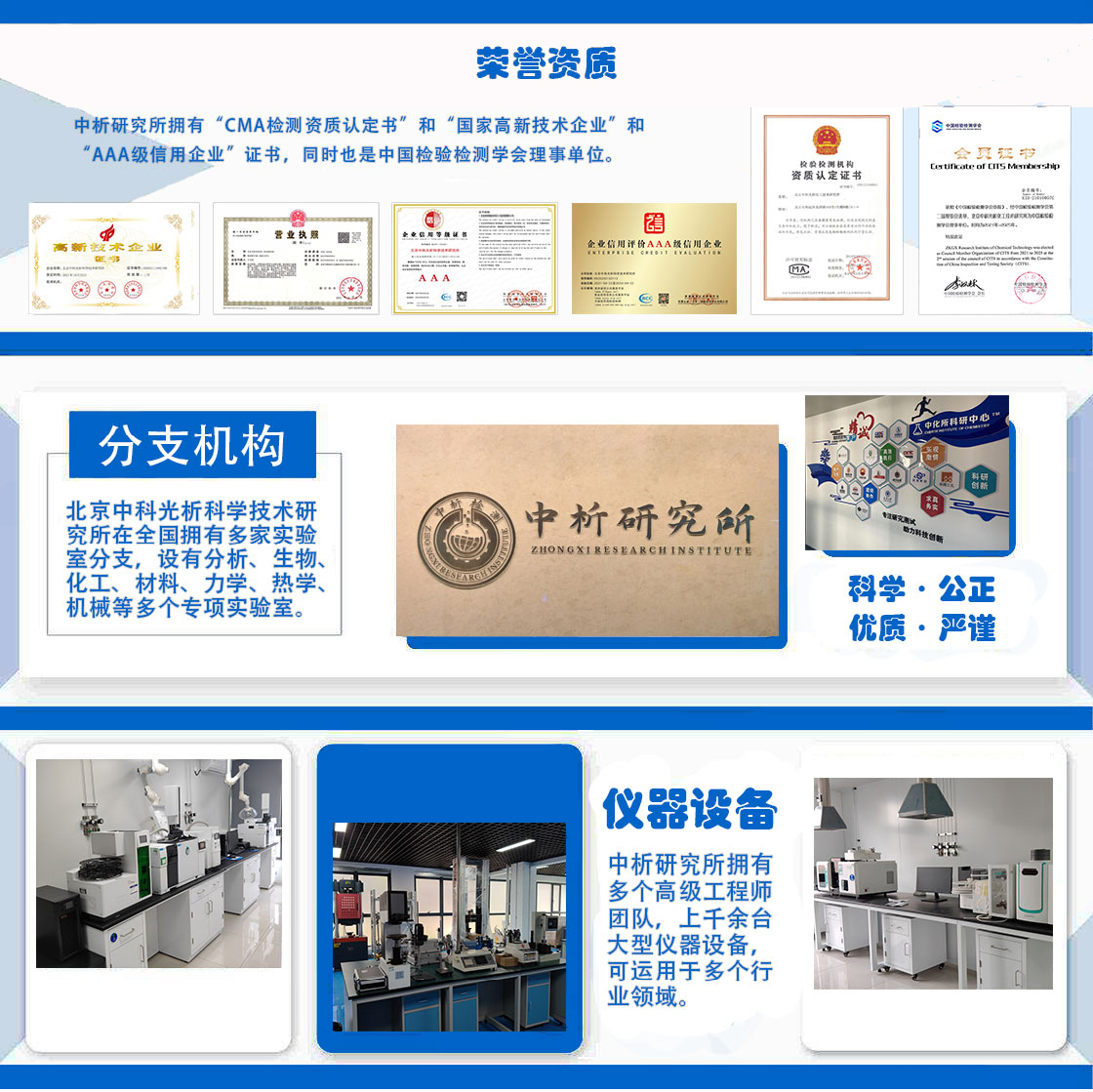
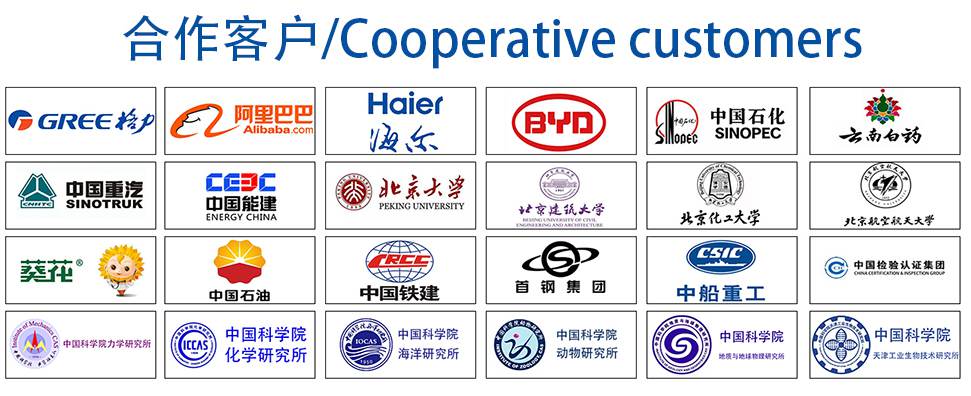
材料实验室
热门检测
8
15
15
14
14
15
20
18
18
19
19
17
15
19
22
18
18
20
24
26
推荐检测
联系电话
400-635-0567