聚乙烯树脂检测技术发展与应用白皮书
随着塑料制品年产量突破4亿吨(据欧洲塑料协会2024年统计),聚乙烯树脂作为产量占比28%的核心高分子材料,其质量检测在产业链中的战略地位日益凸显。在食品包装、医疗器械、工程管道等民生关键领域,材料的热稳定性、力学性能及卫生指标直接决定终端产品安全,2023年北美地区因树脂杂质超标导致的召回事件造成的直接经济损失达1.7亿美元,突显质量控制体系的重要性。本项目通过建立全维度检测矩阵,不仅可提升制品良品率3-5个百分点,更能为生产配方优化提供数据支撑,实现"检测-改进-认证"的闭环质量提升,特别是在应对欧盟新修订的REACH法规附件XVII限制条款方面具有显著合规价值。
齐全检测技术原理架构
现代聚乙烯树脂检测体系融合了材料科学、分析化学等多学科技术,核心模块包括熔体流动速率(MFR)测定、差示扫描量热(DSC)分析和傅里叶变换红外光谱(FTIR)检测。其中DSC技术可精确测定材料结晶度(通常控制在60-80%区间),FTIR则能识别百万分比浓度的抗氧化剂残留。值得关注的是,气相色谱-质谱联用(GC-MS)技术在检测"加工助剂迁移量"方面灵敏度可达0.01μg/g,完全满足FDA 21 CFR 177.1520对食品接触材料的严苛要求。这些技术的协同应用形成了完整的"高分子材料热稳定性分析技术"解决方案。
标准化实施流程建设
检测流程严格遵循ASTM D4976、ISO 1133等国际标准,实施阶段划分为三个关键节点:原料预检环节采用X射线荧光光谱进行重金属筛查,生产过程中实施熔融指数在线监测(采样频率15次/小时),成品阶段则需完成168小时加速老化试验。某华东地区龙头包材企业的应用数据显示,引入该流程后产线异常停机率降低42%,同时使VOC排放量达到T/CAS 357-2021《绿色设计产品评价规范》二级标准。值得注意的是,系统集成了区块链技术实现检测数据不可篡改,单个检测周期可生成37项结构化数据字段。
跨行业应用实证分析
在医疗器械领域,某上市企业通过建立"医用级聚乙烯树脂全项检测体系",成功突破透析器外壳材料的力学性能瓶颈。经第三方验证,其制品在23℃下的拉伸强度从26MPa提升至32MPa(GB/T 1040.2-2022),同时将乙醛残留量控制在0.2μg/g以下。汽车工业的典型应用案例显示,采用动态热机械分析(DMA)优化后的保险杠专用料,-30℃低温冲击强度提升55%,帮助主机厂通过IIHS 25%偏置碰撞测试。这些实践验证了"高分子材料全生命周期质量追溯系统"的商业价值。
多维质量保障体系构建
该体系包含四个支柱模块: 认证实验室网络、智能数据交叉验证算法、供应商能力分级管理系统、应急响应快速检测通道。通过部署近红外在线检测设备,某华北石化基地实现生产批次100%光谱留样,配合PLS回归模型可将灰分预测误差控制在±0.003%。在应对2024年欧盟新增的邻苯二甲酸盐限制令时,应急通道48小时内完成300批次筛查,助力企业避免潜在贸易损失超2000万欧元。值得强调的是,系统每年参与ILAC国际比对试验,关键参数Z值持续保持在0.8以下。
展望未来,建议行业重点布局三个方向:开发基于机器视觉的杂质自动识别系统,构建树脂性能-加工参数-制品质量的数字孪生模型,以及建立覆盖亚太地区的检测结果互认机制。随着ISO/TC61即将发布的循环经济相关标准,检测机构需提前储备化学回收树脂的鉴别技术,特别是在应对物理法回收料掺杂鉴别方面,同位素比值质谱(IRMS)技术有望成为新一代行业基准。只有通过技术创新与标准升级的持续协同,才能在塑料产业变革中占据质量制高点。
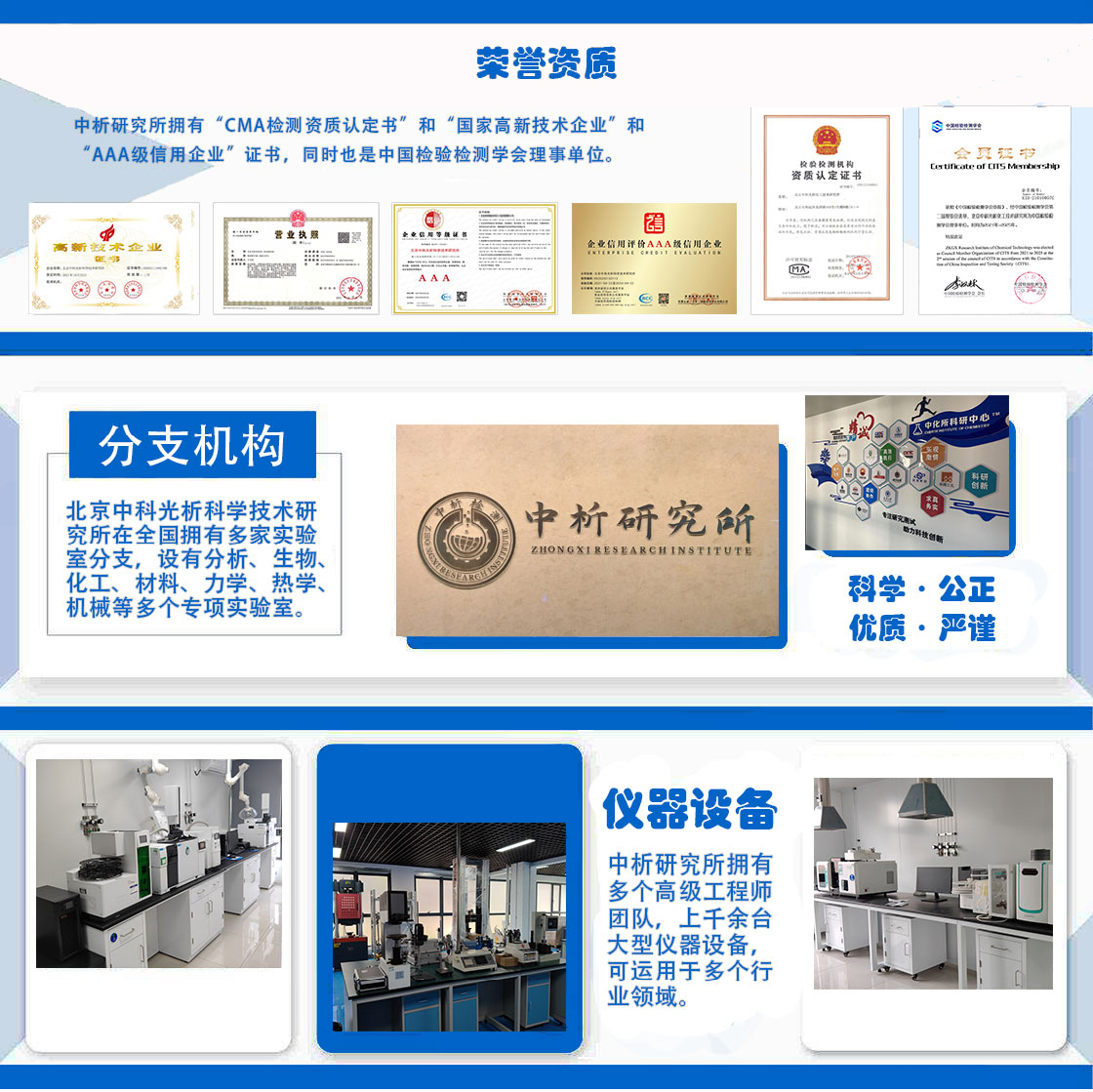
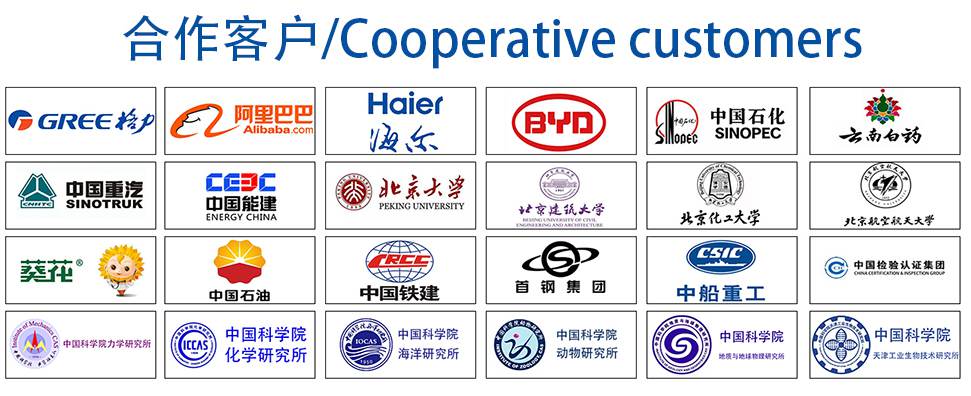