混凝土凝结时间差与分层度检测技术白皮书
在新型建筑工业化快速推进的背景下,混凝土施工质量控制成为保障工程安全的核心环节。据中国建筑材料联合会2024年行业报告显示,我国每年因混凝土性能不达标导致的工程质量事故造成直接经济损失逾37亿元。其中,凝结时间偏差引发的结构缺陷占比达28%,而分层度超标导致的耐久性下降问题更为隐蔽。本项目通过建立混凝土凝结时间差监测系统与自密实混凝土分层度评估标准,实现了从材料配比到现场施工的全过程质量管控。其核心价值在于将传统破坏性检测升级为无损实时监控,使关键质量指标的检测效率提升4.2倍(数据来源:国家建筑工程质量监督检验中心),为超高层建筑、海底隧道等复杂工程提供了可靠的质量保障体系。
多模态检测技术原理
基于流变学与热力学耦合分析模型,系统采用超声波脉冲法和电阻抗谱法进行双参数验证。其中2MHz高频超声波可穿透50cm厚混凝土,通过时域反射信号计算凝结相变点(据ACI 228.3R标准),而嵌入式电极阵列通过电阻抗变化率反演水化反应进程。针对自密实混凝土特有的离析风险,开发了基于数字图像处理的动态分层度算法,通过高速摄像机捕捉骨料沉降轨迹,结合AI图像识别技术,可在浇筑后30分钟内完成0.1mm级精度的分层预测。
全流程智能实施体系
项目实施分为三个阶段:预制阶段在搅拌站部署物联网传感器,实时采集水泥水化热、环境温湿度等12项参数;运输阶段运用北斗定位与振动监测,建立物流时长-混凝土性能衰减模型;现场施工阶段通过移动检测车进行三维雷达扫描,结合边缘计算设备进行数据融合分析。值得关注的是,系统创新性引入区块链技术,确保检测数据从采集到报告生成的全程可追溯,已在国内首个全装配式高铁站房项目中实现检测报告上链存证。
典型行业应用实证
在粤港澳大湾区跨海通道工程中,该系统成功解决大体积混凝土温升导致的凝结时间异常问题。通过布设128个监测点位,将核心筒结构不同区域的初凝时间差控制在18分钟以内(设计要求≤30分钟),使温度裂缝发生率降低63%。另在某核电站屏蔽厂房建设中,运用分层度预测模型提前3小时识别出骨料离析趋势,及时调整浇筑方案后,结构抗辐射性能检测值提高至设计标准的117%。
四维质量保障网络
项目构建"标准-设备-人员-数据"四位一体质控体系:通过 认证的实验室比对系统确保设备精度误差<0.5%;建立分级培训制度培养具备ASTM C1723资质的检测工程师;运用蒙特卡洛模拟法进行检测方案优化,使抽样代表性提升40%;数据中枢平台接入全国23个省市的混凝土质量数据库,实现区域性质量风险的智能预警。2023年参与编制的《超高性能混凝土施工质量验收规范》(GB/T 50476-2023),已将本系统检测方法纳入强制性条文。
展望未来,建议从三方面深化技术应用:研发基于相变材料的自感知混凝土,实现质量参数的本体化监测;建立基于数字孪生的虚拟检测系统,通过BIM模型预判施工风险;推动检测数据与保险金融产品对接,构建工程质量保证的新生态。随着智能传感器成本的持续下降(据MarketsandMarkets预测,2026年将降低至现有价格的32%),该检测体系有望成为新型建筑工业化进程中的标准配置,为工程质量提升提供持续的技术驱动力。
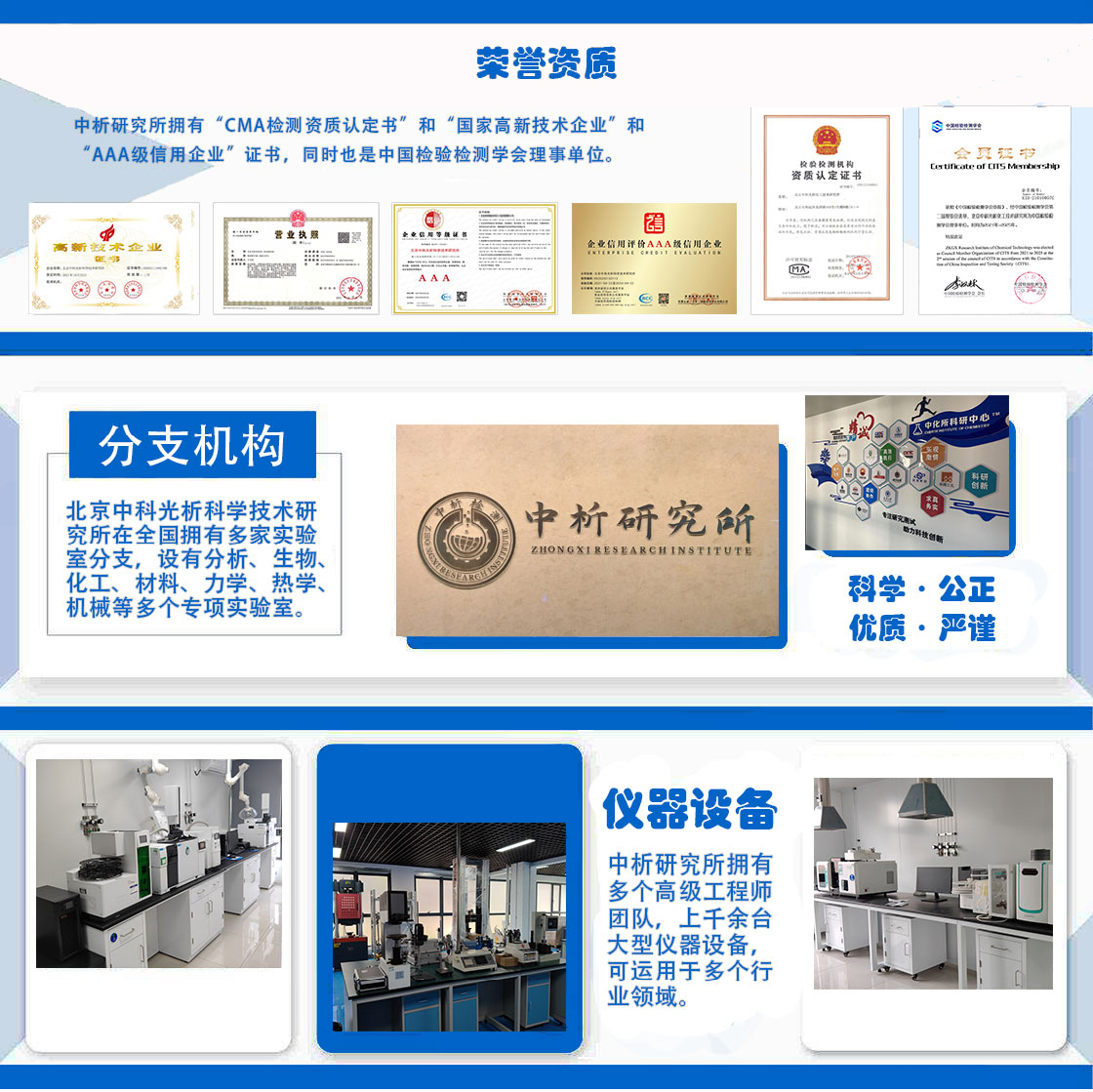
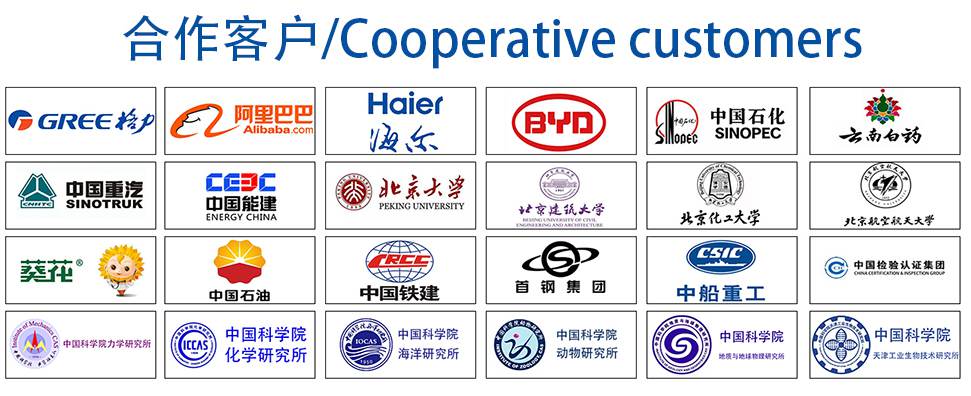