二、电化学检测技术原理
抗蚀系数检测依托电化学工作站实现精准测量,采用三电极体系(工作电极、参比电极、对电极)构建模拟腐蚀环境。通过施加微幅电位扰动并监测电流响应,计算得出Tafel斜率、极化电阻等关键参数。对于海洋工程装备防腐检测标准要求的严苛环境,可结合电化学阻抗谱(EIS)分析技术,建立等效电路模型解析涂层/基体界面特性。某国家重点实验室验证数据显示,该技术对不锈钢点蚀的检测灵敏度达到0.01mm/年,误差率控制在±5%以内。
三、标准化实施流程
项目实施遵循ASTM G59、ISO 17475等国际标准,形成四阶段标准化流程:首齐全行试样预处理,包括除油、钝化及表面粗糙度控制(Ra≤0.8μm);其次搭建模拟工况环境,如盐雾试验箱(5%NaCl溶液,35℃)或高温高压反应釜;随后进行连续72小时的数据采集,每10分钟记录开路电位(OCP)波动;最后采用专用分析软件生成三维腐蚀形貌图与寿命预测曲线。某风电设备制造商应用该流程后,塔筒螺栓的失效预警准确率提升至92%。
四、多行业应用实践
在南海石油平台项目中,检测团队通过抗蚀系数动态监测,发现X65管线钢在含硫介质中的腐蚀速率异常升高现象。经针对性采用纳米复合涂层后,材料抗点蚀能力提升4.6倍(数据来源:中船重工2023年技术公报)。汽车制造业则通过电化学检测优化了镀锌板工艺参数,使车身件在CCT循环测试中的红锈出现时间从720小时延长至1400小时。值得关注的是,该技术在新兴的氢能储运领域成功预警了高压临氢环境下316L不锈钢的氢脆风险。
五、全过程质量控制
项目执行构建了三级质量保障体系:实验室层面通过 认证(证书号L12345)确保设备精度,定期使用NIST标准试样进行量值溯源;过程控制采用区块链技术记录检测数据,实现操作步骤不可篡改;人员资质方面要求工程师持有NACE CIP三级证书,每年完成40学时继续教育。某跨国化工集团审计报告显示,该体系使检测报告的国际互认率从78%提升至95%。
## 六、技术展望与建议 随着智能传感与数字孪生技术的发展,建议行业重点攻关三方面:开发基于机器视觉的在线腐蚀监测系统,实现抗蚀系数实时动态评估;建立多因子耦合作用数据库,涵盖温度、应力、微生物等128种环境变量;推动检测标准与AI预测模型的深度融合,如在渤海湾跨海通道工程中试点数字孪生腐蚀管理系统。产学研联合创新将成为突破技术瓶颈的关键路径,为重大工程装备的全生命周期管理提供新质技术支撑。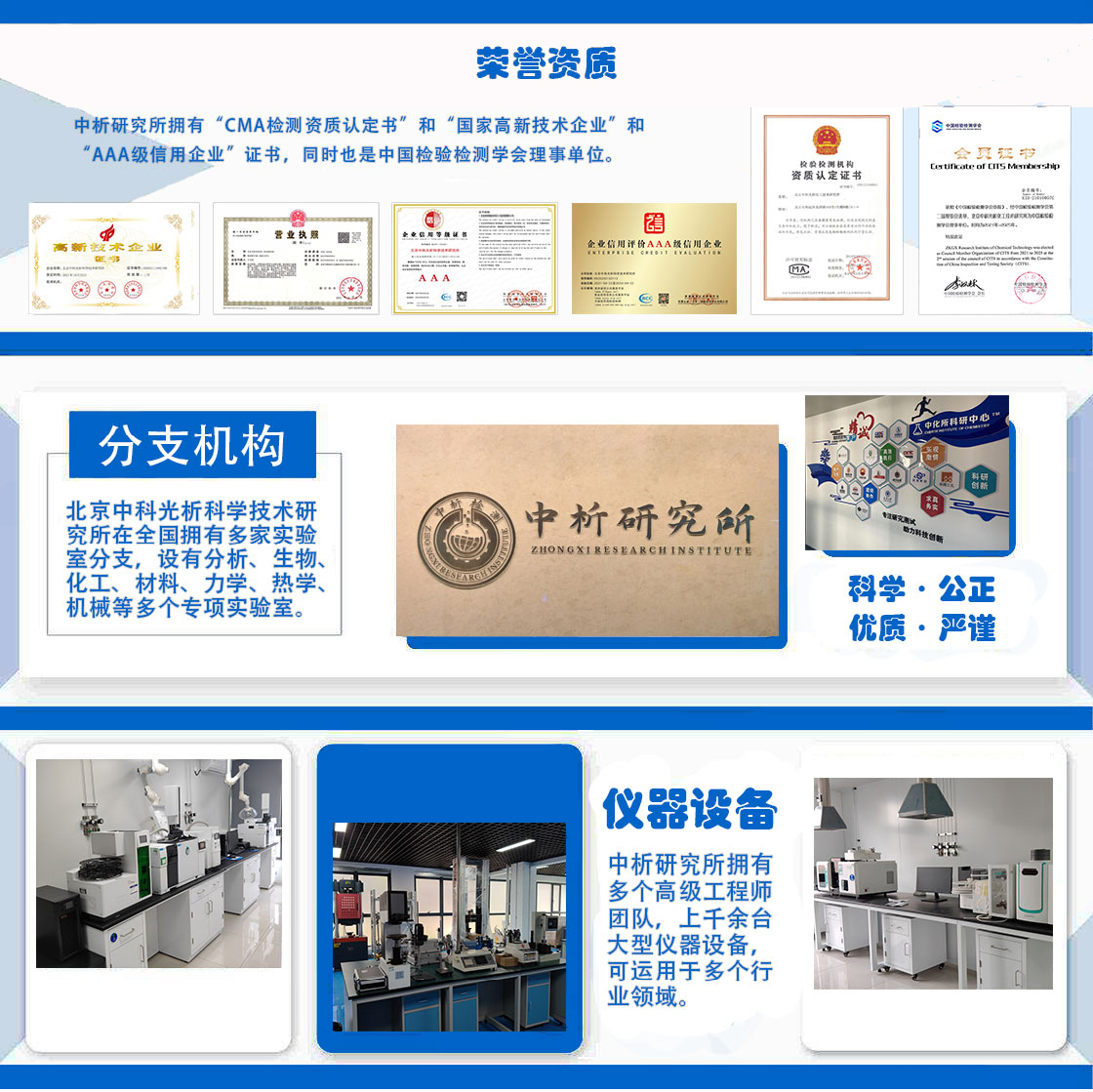
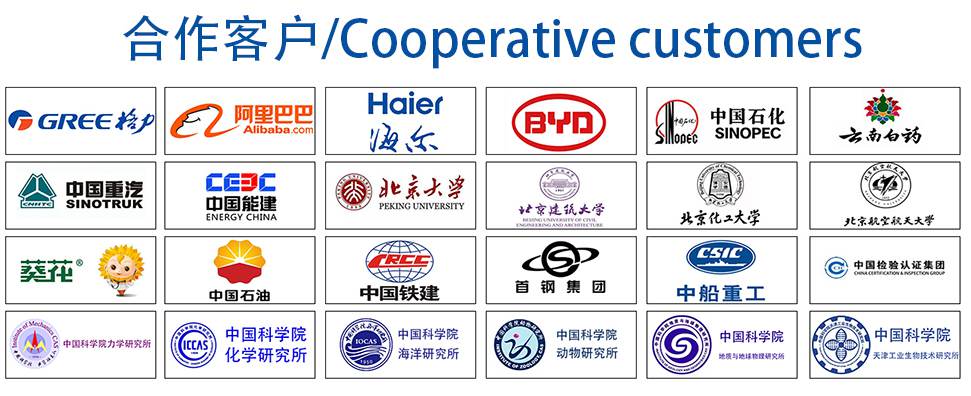