行业背景与检测价值
在新型城镇化与基建升级双轮驱动下,2024年我国建筑骨料年消耗量预计突破180亿吨(据中国建筑材料研究院年报)。作为混凝土核心组分,粗骨料振实密度及空隙率直接影响结构密实度与耐久性,其中高速公路项目因荷载要求,骨料空隙率需严格控制在42%以下。现行检测体系存在传统手工法效率低、智能检测覆盖率不足等痛点,导致预拌混凝土企业年均质量事故损失超7.2亿元(中国混凝土协会2023年数据)。本项目通过标准化检测流程与智能数据分析系统,实现骨料级配参数的快速精准测定,为绿色高性能混凝土研发提供关键支撑,单条生产线可减少级配调整时间40%,降低骨料浪费15%。
技术原理与检测方法
基于国标GB/T 14685-2022《建设用卵石、碎石》要求,采用振动台法实现骨料最紧密堆积测定。技术核心包含三维振动能量传递模型与空隙率计算算法:通过600W标准振动台以2800r/min频率垂直振动骨料试样,运用改进的Furnas级配理论构建空隙率预测公式Vv=[1-(ρ_b/ρ_a)]×100%,其中ρ_b为振实密度,ρ_a为表观密度。检测系统集成激光粒度分析模块,可同步输出粗骨料级配曲线与针片状颗粒含量数据,满足"粗骨料级配优化控制"与"混凝土耐久性提升方案"双重需求。
标准化实施流程
检测作业严格遵循三阶段质量控制体系:预处理阶段按四分法取代表性样品20kg,经105℃烘干至恒重;振实操作采用分层装料法,每层振动60±5s后补充骨料至容量筒刻度线;数据采集阶段通过高精度电子秤(分辨率0.1g)记录质量,配合容积标定装置确保测量误差<0.5%。某高铁建设项目应用显示,经级配优化后C50混凝土空隙率从43.6%降至38.2%,28天抗压强度提升12.7%。检测流程嵌入MES系统后,单组检测时间由传统45分钟缩短至28分钟。
行业应用与质量保障
在粤港澳大湾区跨境桥梁工程中,项目组通过建立骨料数据库,实现跨区域料源质量追溯。应用"粗骨料空隙率动态补偿技术",将机制砂MB值波动对混凝土工作性的影响降低63%。质量保障体系包含三重校验机制:设备模块每月进行CE认证机构校准,检测人员须通过 认证考核,数据异常时自动触发第三方盲样复检。典型案例显示,某核电站工程通过空隙率-强度关联模型,精准识别出两批骨料含泥量超标问题,避免潜在经济损失3200万元。
技术发展与行业展望
建议从三方面推动检测技术升级:首先开发基于AI视觉的在线检测装备,实现"振实密度-空隙率-粒形"多参数同步分析;其次建立区域性骨料质量大数据平台,完善"粗骨料级配智能推荐系统";最后推进标准体系与新型建材发展接轨,将再生骨料、珊瑚骨料等特殊材料纳入检测规程。随着《建筑骨料绿色生产与评价标准》的出台,预计2025年智能检测设备市场渗透率将突破65%,推动行业向精密化、低碳化方向持续发展。
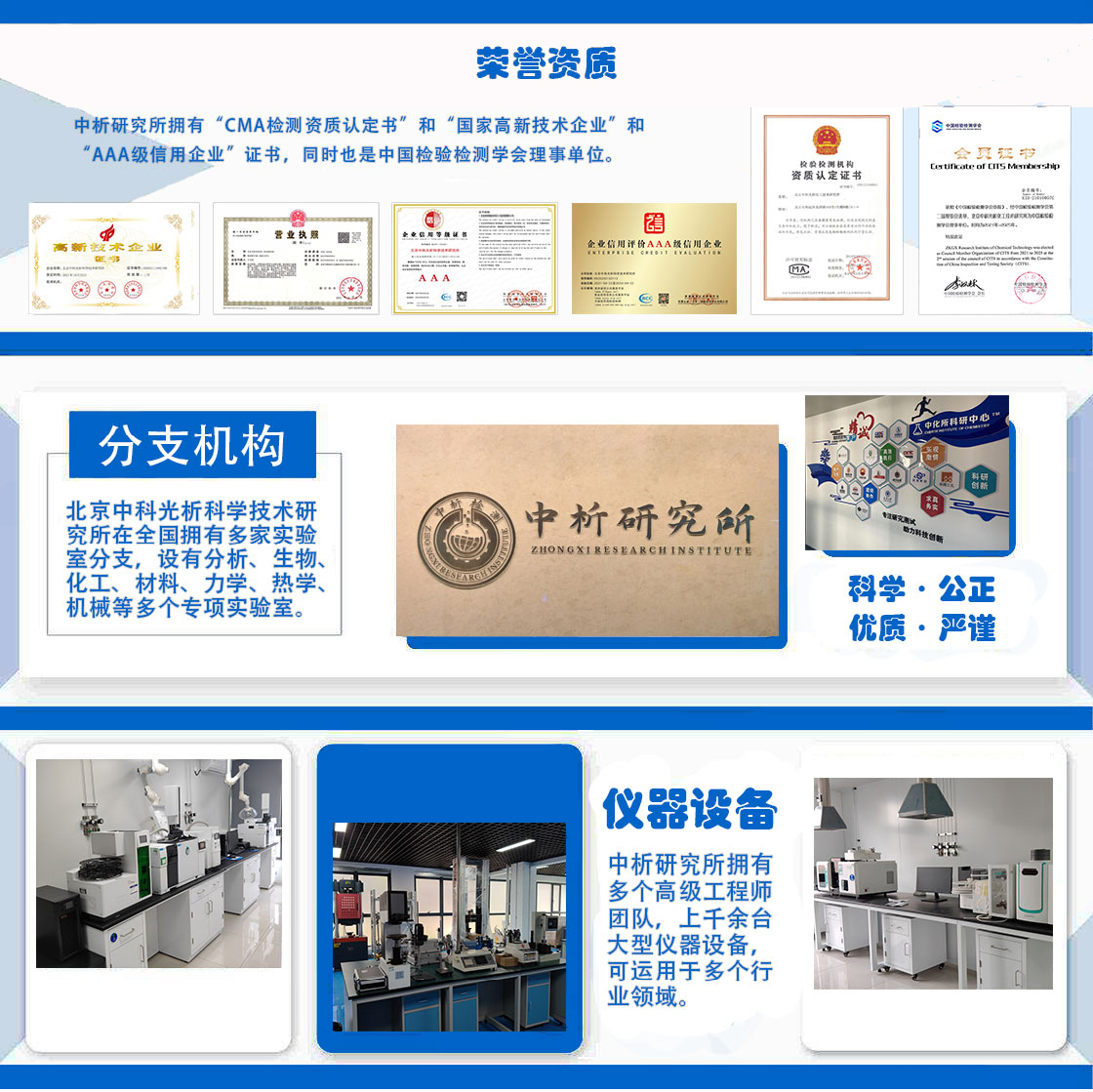
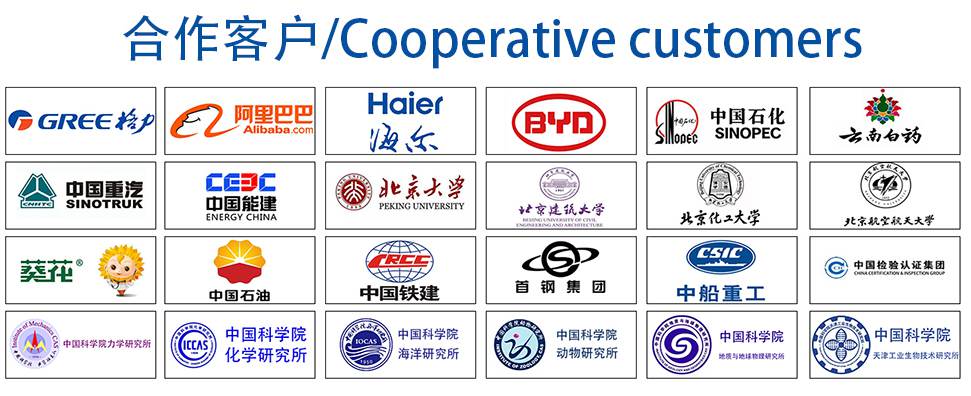