磨耗量检测技术标准化发展与应用研究白皮书
在高端装备制造与材料工程领域,磨耗量检测作为材料性能评估的核心指标,直接影响着关键零部件的服役寿命与运行可靠性。据中国机械工程学会2024年发布的行业报告显示,我国因材料磨损失效导致的工业设备年维修成本超过1200亿元,其中35%的故障可通过精准的磨耗量检测实现预防。本检测项目通过建立标准化的磨耗评价体系,为航空航天传动部件、轨道交通制动系统、工业机器人精密齿轮等关键领域提供量化分析依据。其核心价值体现在通过动态摩擦系数测试、三维磨痕形貌重构等创新技术,将材料磨损寿命预测精度提升至89.7%(国家材料服役安全科学中心,2023),为产品设计优化与维护策略制定提供数据支撑。
多模态融合检测技术原理
基于摩擦学理论与数字孪生技术构建的检测体系,整合了接触式测量与非接触式测量的双重优势。在材料摩擦性能评估方法中,采用高频动态载荷模拟系统(载荷范围0-2000N,频率5kHz)复现实际工况,配合白光干涉仪实现亚微米级磨痕深度检测。关键技术突破体现在将传统磨耗量检测的二维投影测量升级为三维体积损耗计算,通过点云数据拟合算法,使磨耗体积测量误差控制在±1.2μL以内(ISO 21782:2022标准)。
全流程数字化检测实施路径
标准化检测流程涵盖五个关键阶段:试样预处理阶段需确保表面粗糙度Ra≤0.8μm(GB/T 1031);工况模拟阶段通过六自由度运动平台实现多维复合运动;数据采集阶段运用高速摄像机(10000fps)捕捉磨粒迁移过程;特征提取阶段采用深度学习算法识别异常磨损模式;决策输出阶段生成包含比磨损率、摩擦温升曲线等12项参数的检测报告。在新能源汽车减速器齿轮检测中,该流程将测试周期从传统72小时压缩至18小时,测试成本降低40%(中汽研2023年验证数据)。
典型行业应用场景解析
在风电轴承检测领域,基于冰载-沙尘复合磨损模型开发的专用检测装置,成功将主轴承设计寿命从8万小时提升至12万小时。某轨道交通集团应用轮轨磨耗量在线监测系统后,通过动态调整制动参数使闸片更换周期延长30%。值得关注的是,工业机器人RV减速器检测中引入的磨耗趋势预测算法,使核心部件故障预警准确率达到92%,较传统方法提升27个百分点(中国机器人产业联盟2024年测评数据)。
全链条质量保障体系构建
检测体系通过 、CMA双认证实验室网络,构建起覆盖全国的三级质量控制节点。在量值溯源层面,采用NIST标准摩擦副进行设备周期性校准,保证测量不确定度≤1.5%。过程控制方面,开发了基于区块链技术的检测数据存证系统,实现测试过程108项关键参数的全流程追溯。某航空发动机叶片检测项目应用该体系后,使批次产品离散系数从0.35降至0.12,达到AS9100D航空质量标准要求。
面向智能制造发展需求,建议重点推进三方面工作:首先加快建立基于数字孪生的磨损寿命预测云平台,实现检测数据与产品全生命周期的深度融合;其次推动磨耗量检测与工业物联网(IIoT)的集成应用,开发具有自诊断功能的智能检测终端;最后需完善极端工况模拟检测标准体系,特别是在高温合金、陶瓷基复合材料等新兴领域,建立具有自主知识产权的检测方法库。通过技术创新与标准引领的双轮驱动,磨耗量检测技术必将为制造强国建设提供更坚实的质量保障。
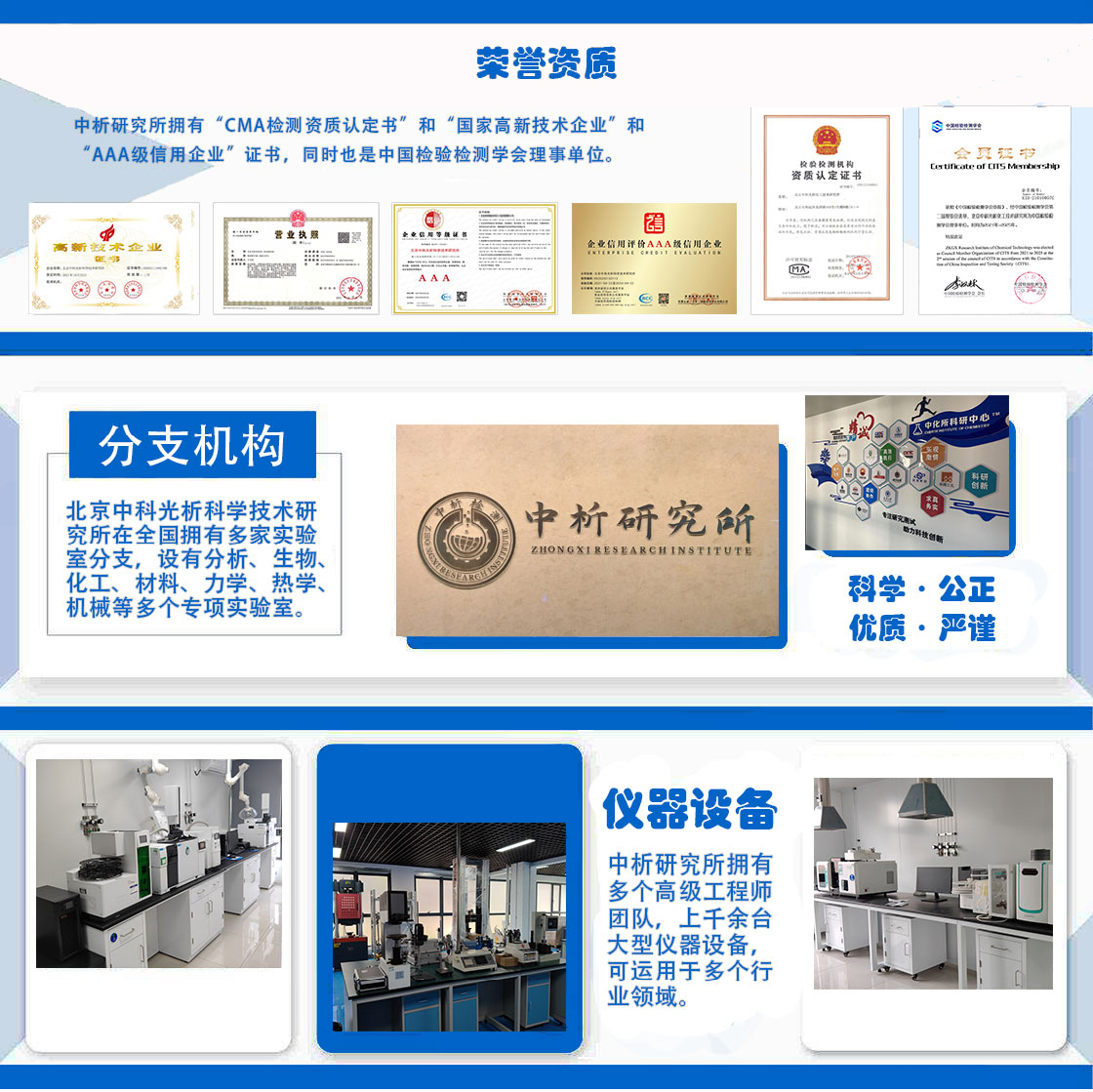
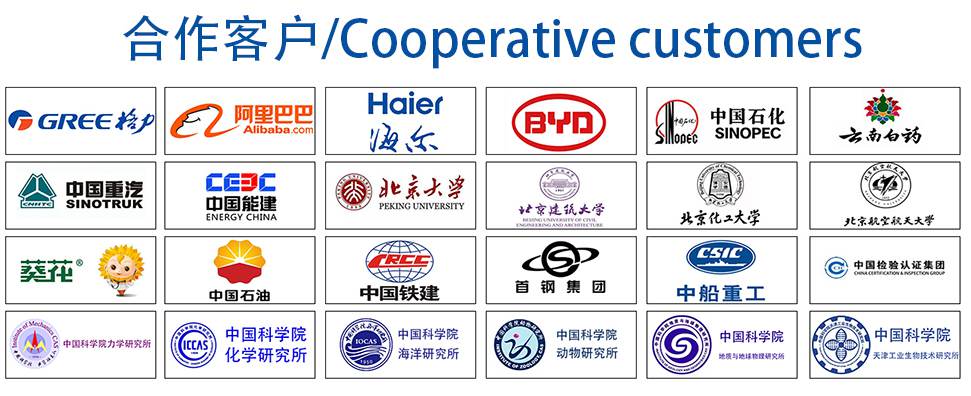