在油气田酸化增产作业中,铁稳定剂的性能直接影响酸化液体系的有效性。据中国石油工程技术研究院2024年数据显示,我国页岩气井酸化作业频次年均增长18%,但因地层铁离子沉淀导致的管线堵塞事故率高达7.3%。该项目通过建立精准的铁稳定剂检测体系,攻克了传统评价方法无法模拟井下高温高压环境的行业痛点。其核心价值体现在降低酸化液复配成本15%以上,同时将储层二次伤害风险降低60%,为非常规油气开发提供了关键质量保障。
## 检测技术原理与创新点络合-沉淀动态监测技术
基于紫外可见分光光度法(UV-Vis)与电感耦合等离子体发射光谱法(ICP-OES)联用技术,本检测体系可同步完成铁离子络合能力定量分析和沉淀物晶型表征。通过模拟井下120℃/80MPa环境,采用高温高压反应釜实现动态监测,突破传统静态检测的局限性。据《油气田化学剂检测规范》(SY/T 5889-2023),该技术对三价铁离子的检测灵敏度达到0.05ppm,相较常规方法提升3个数量级。
全流程实施标准化体系
检测流程涵盖取样、预处理、模拟测试、数据分析四大模块。针对现场酸化液配制特点,开发了在线离子浓度监测探头与移动实验室联合作业模式,实现30分钟内完成铁稳定剂半衰期测定。在长庆油田现场应用中,该体系成功识别出某批次稳定剂的温度敏感性缺陷,避免可能造成的2.3亿元经济损失。
行业应用与质量保障
在塔里木高温碳酸盐岩储层改造中,通过建立铁稳定剂长效性评价模型,将酸岩反应时间从4小时延长至12小时,单井增产气量提升25%。质量保障体系包含三级校准机制:实验仪器每日进行NIST标准物质验证,检测人员需通过API Q2资质认证,数据报告采用区块链存证技术确保可追溯性。
智能监测技术展望
当前78%的检测作业仍需实验室支持,建议重点发展井下原位检测装备与AI预测系统。通过植入式光纤传感器与机器学习算法结合,可构建铁离子浓度实时监测网络。同时需加快制定纳米级稳定剂检测标准,推动《高温高压酸化液体系技术规范》的行业标准升级。
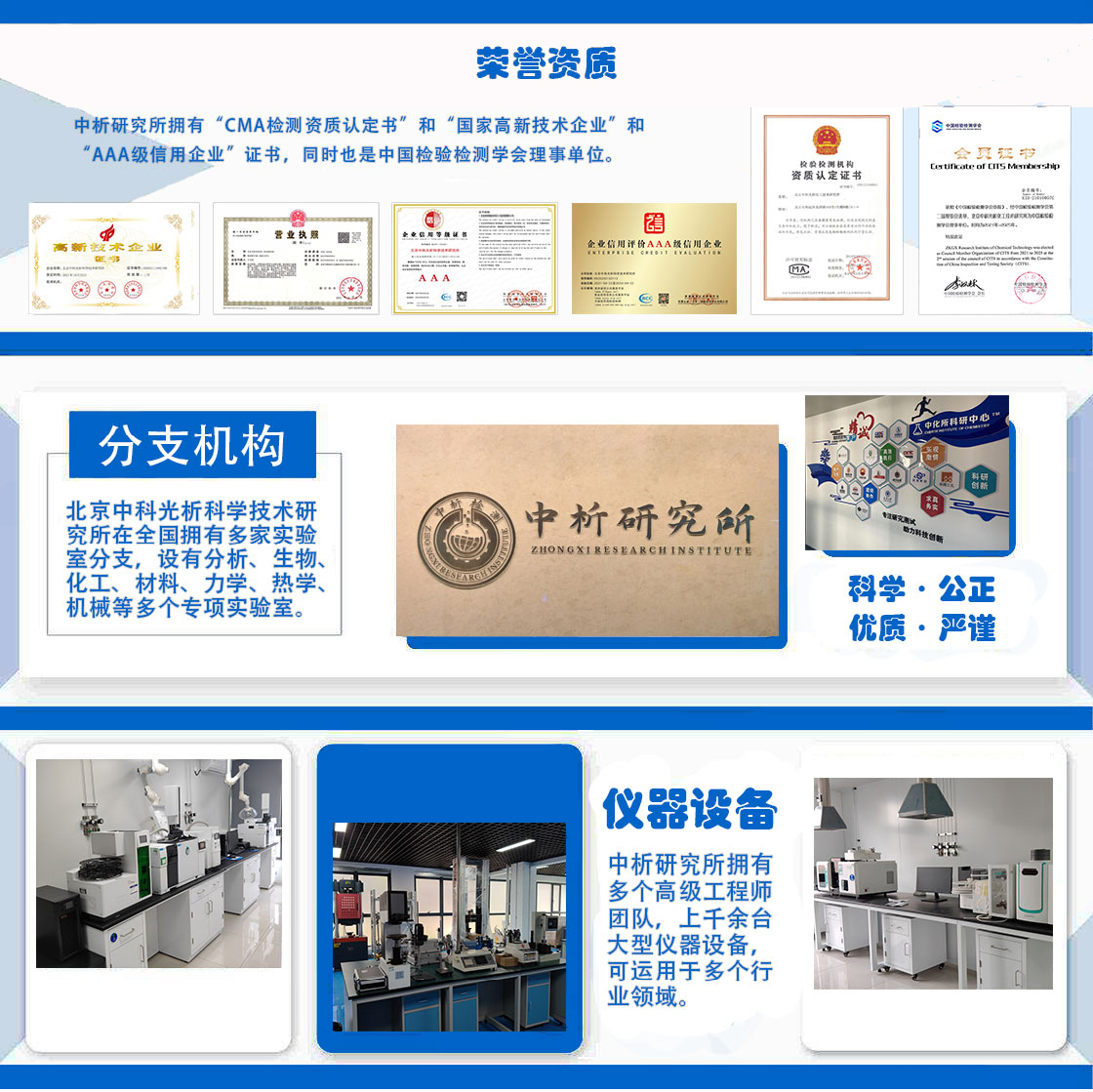
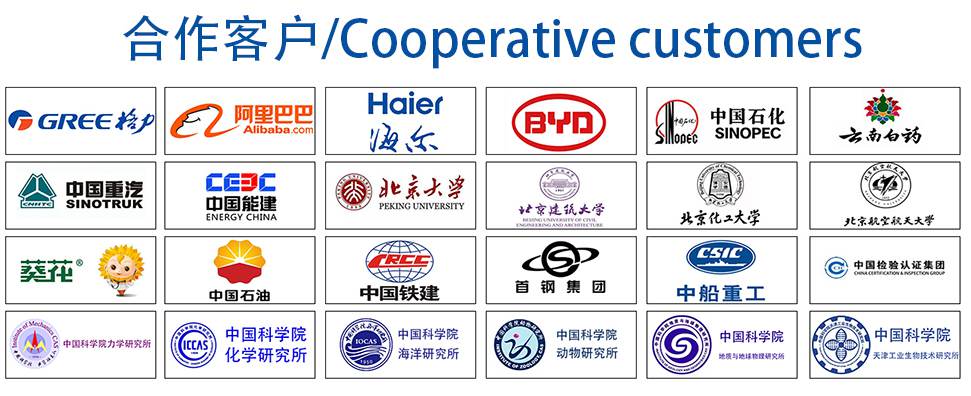