# 钢铁及制品检测技术发展与行业应用白皮书
## 首段:行业背景与核心价值
在工业化进程加速的背景下,钢铁及制品作为基础材料广泛应用于建筑、交通、能源等关键领域。据国际钢铁协会(Worldsteel)2024年统计,粗钢年产量达19.8亿吨,其中中国占比53.2%。然而,材料缺陷引发的工程事故仍呈上升趋势,仅2023年欧盟通报的金属制品质量缺陷案例就增长17%。在此背景下,钢铁检测项目通过精准识别材料成分、力学性能及内部结构,成为保障行业安全的核心技术手段。其核心价值体现在三方面:一是通过无损检测技术延长设备生命周期,据中国机械工程学会测算,科学检测可降低30%的维修成本;二是推动高强钢、耐候钢等新型材料研发,支撑新能源装备制造升级;三是构建全产业链质量追溯体系,满足ISO 6892、ASTM A370等国际标准要求。
---
## 技术原理与创新突破
### h2 多模态融合检测技术体系
现代钢铁检测采用光谱分析、超声波探伤与数字图像处理的协同工作机制。X射线荧光光谱(XRF)实现0.001%级微量元素检测,配合电磁超声(EMAT)技术可穿透50mm厚钢板识别0.1mm级裂纹。值得关注的是,基于深度学习的视觉检测系统已实现98.7%的夹杂物识别准确率(中国金属材料研究院,2024),大幅提升检测效率。
---
## 全流程标准化实施路径
### h2 闭环式质量管控流程
典型检测流程包含五个关键阶段:①原材料入场时的成分快筛(30分钟出具报告);②轧制过程中的在线厚度监测(±0.02mm精度);③热处理后的硬度梯度分析;④成品阶段的拉伸/冲击试验(满足GB/T 228.1标准);⑤交付前的第三方认证复核。某特钢企业通过实施该体系,使产品退货率从1.2%降至0.3%。
---
## 行业应用与场景深化
### h2 高端装备制造质量护航
在风电轴承领域,采用相控阵超声检测技术(PAUT)的厂商成功将故障率控制在0.05次/万小时运行。某船舶制造集团引入残余应力检测系统后,分段焊接变形量减少42%,工期缩短15天。特别是在核电主管道检测中,全自动爬壁机器人可完成200℃环境下的焊缝扫描,缺陷检出率较人工提升40个百分点。
---
## 质量保障体系构建
### h2 四维立体化质控网络
行业领先机构已建立包含设备、人员、方法和环境的完整质控链:①定期使用NIST标准样品进行设备校准;②检测人员需通过EN ISO/IEC 17025认证;③每批次样品实施平行样对比;④实验室环境温湿度波动控制在±1℃/±5%RH。某国家质检中心通过该体系,连续五年通过ILAC国际实验室比对验证。
---
## 展望与建议
随着工业4.0技术渗透,建议行业重点布局三大方向:①开发基于数字孪生的预测性检测系统,实现材料性能退化模拟;②建立区块链赋能的检测数据共享平台,打通产业链质量信息壁垒;③推广绿色检测技术,如激光诱导击穿光谱(LIBS)替代传统化学分析法,减少90%的试剂消耗。唯有持续创新,方能应对新能源汽车一体压铸、氢能储运设备等新兴领域对材料检测提出的更高要求。
上一篇:通用设备和分系统检测下一篇:酸化用铁稳定剂检测
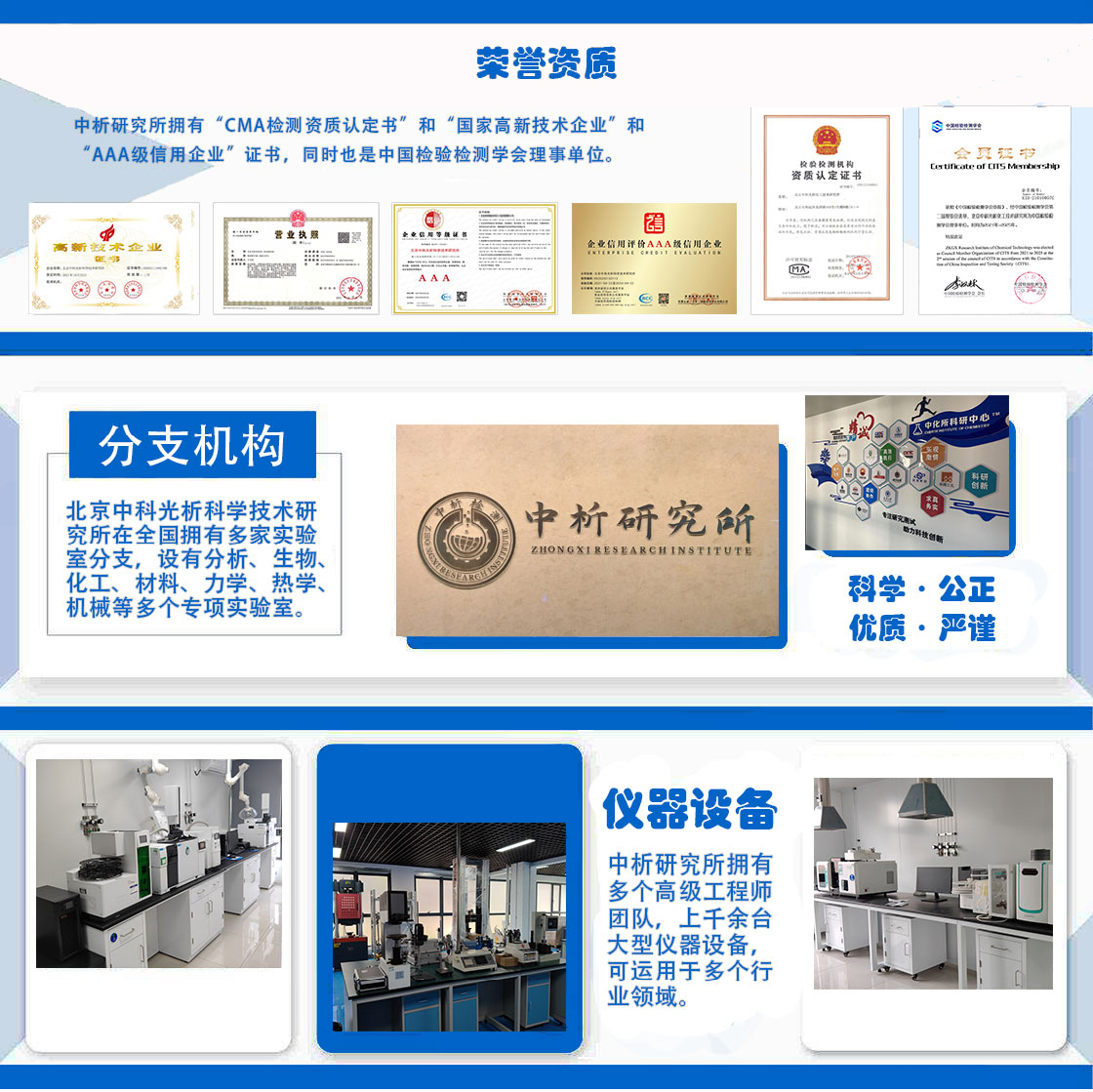
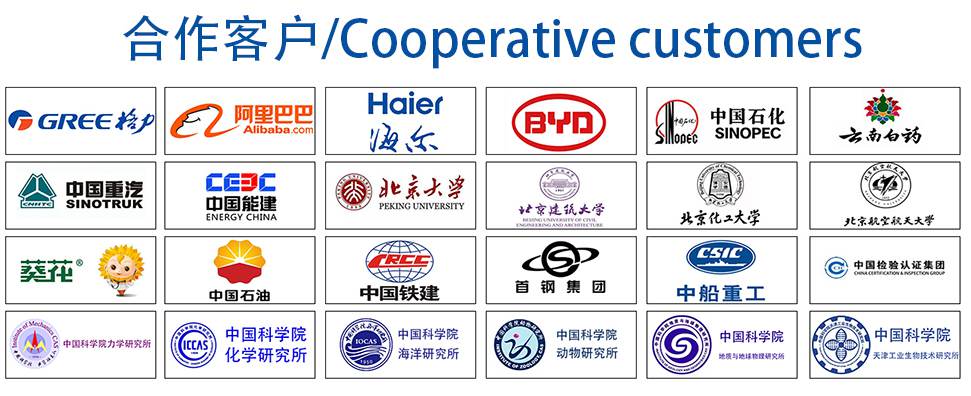
材料实验室
热门检测
推荐检测
联系电话
400-635-0567