耐湿热检测在工业产品质量控制中的关键作用
在气候变暖及制造业转型升级的背景下,工业产品在高温高湿环境下的性能稳定性受到空前关注。据中国电器工业协会2024年报告显示,湿热环境引发的产品故障在工业设备失效案例中占比达37.2%,推动耐湿热检测成为现代工业品质量验证的核心环节。该项目通过模拟热带气候、沿海环境等极端湿热条件,系统评估材料耐腐蚀性、电气绝缘性能及机械强度衰减情况,为企业建立全生命周期质量预测模型提供数据支撑。其核心价值体现在降低产品环境适应性风险、延长设备服役周期以及提升国际市场准入合规性三个维度,特别是在新能源汽车三电系统、航空航天精密器件等战略领域,已成为保障产品可靠性的必要技术手段。
技术原理与创新突破
耐湿热检测基于环境应力筛选理论(ESS),通过温湿度耦合控制系统实现精准环境模拟。现代检测设备可将温度控制在±0.5℃精度,湿度波动范围≤3%RH(据国家环境适应性检测中心技术标准)。创新性体现在多应力协同加载技术,部分实验室已实现温湿度、振动、盐雾等多因素复合模拟,更真实还原南海岛礁、热带雨林等特殊工况。其中湿热交变应力测试方法(THCT)通过48小时循环测试,可加速模拟产品在东南亚气候条件下5年的老化过程,检测效率提升20倍。
标准化实施流程构建
项目执行严格遵循IEC 60068-2-30标准体系,分为预处理、初期检测、环境试验、恢复处理、最终检测五个阶段。以某新能源汽车电池包检测为例:首先在25℃/50%RH条件下进行8小时稳定,随后进入85℃/85%RH高温高湿箱进行168小时持续测试,其间每间隔8小时采集绝缘阻抗、外壳变形量等关键参数。值得注意的是,最新行业规范要求必须包含至少3次温度循环冲击,以检验材料界面热应力耐受能力。
行业应用场景解析
在轨道交通领域,中车集团采用GJB 150.9A-2009标准对高铁车厢连接器进行检测,成功将湿热环境下的接触故障率从0.12‰降至0.03‰(中国中车2023年技术白皮书)。消费电子行业典型案例是华为海洋通信设备,通过85℃/95%RH条件下的2000小时耐久测试,验证了海底光缆连接器在南海高温高盐环境的长期可靠性。值得关注的是,医疗设备检测正引入动态湿度波动技术,模拟手术室高频率温湿度变化对监护仪性能的影响。
全流程质量保障机制
行业领先机构构建了三维质量保障体系:设备层采用NIST可追溯的校准系统,每季度进行温湿度分布验证;过程层实施检测数据区块链存证,确保测试过程不可篡改;人员层要求检测工程师必须取得 -CL01:2018资质认证。上海材料研究所的创新实践显示,通过引入机器学习算法分析失效模式,可使检测故障定位准确率提升40%,误判率降低至0.7%以下。
未来发展趋势建议
随着复合环境检测需求的增长,建议重点发展三个方向:一是开发基于数字孪生的虚拟检测技术,构建真实环境与数字模型的动态映射;二是建立跨行业湿热环境谱数据库,实现失效数据的智能挖掘与共享;三是完善梯度化检测标准体系,针对不同气候带制定差异化评价指标。值得强调的是,应加快制定光伏组件湿热老化评价的专项标准,以应对新能源装备的化部署需求。
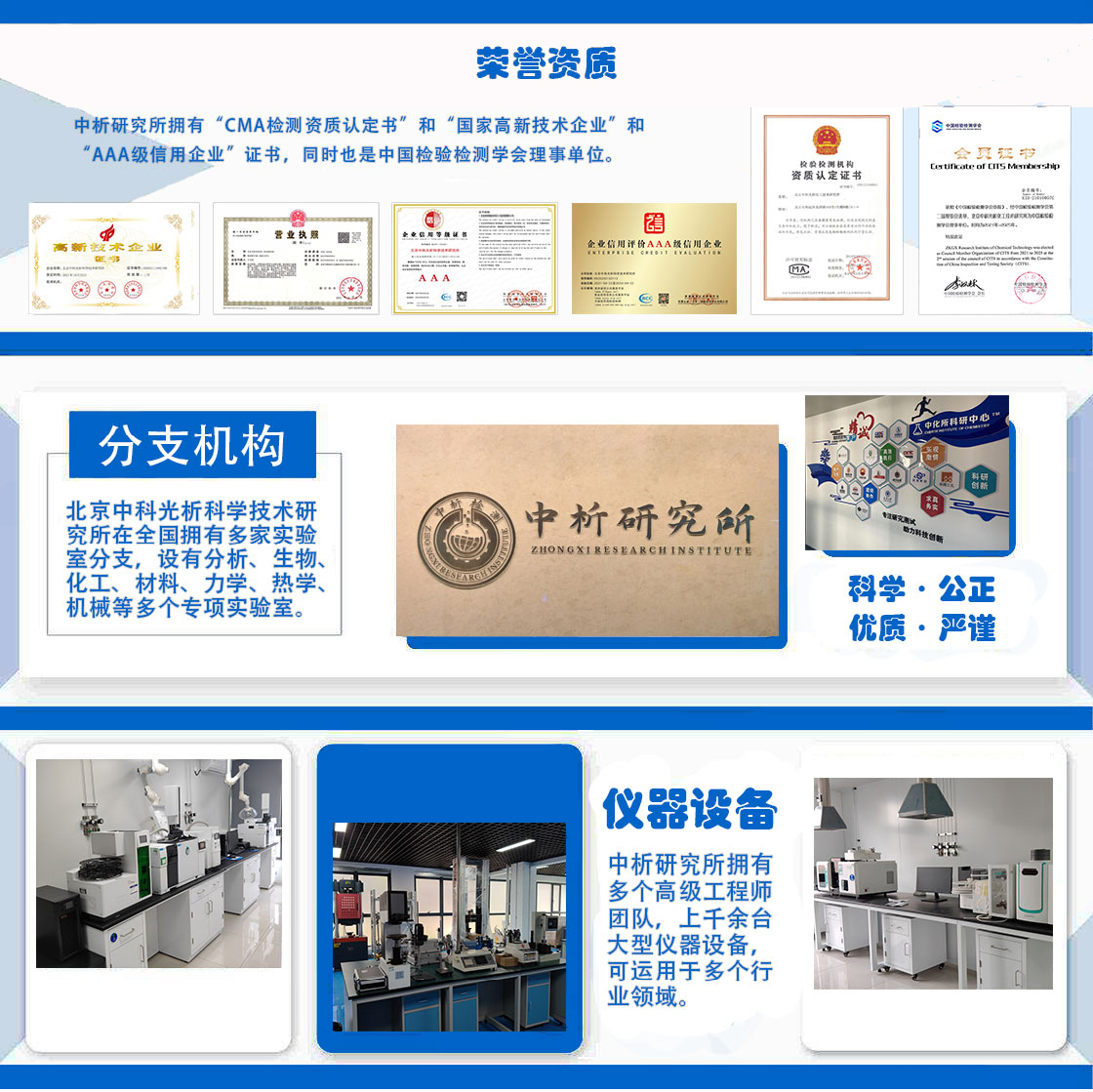
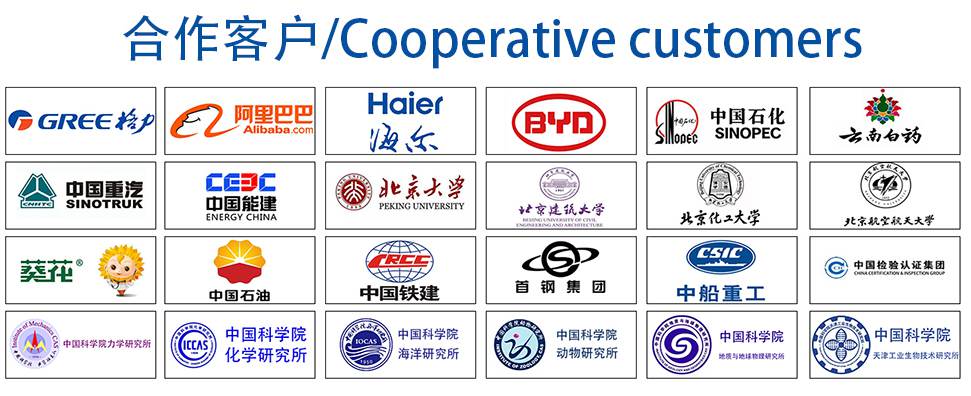