焊接接头拉伸试验检测技术应用与发展白皮书
在工业制造领域,焊接作为基础连接工艺广泛应用于压力容器、管道系统及钢构工程等关键设施。据中国焊接协会2024年行业报告显示,国内每年焊接结构件总量突破1200万吨,其中86%的装备失效事故起源于焊接缺陷。焊接接头拉伸试验作为评估焊缝力学性能的核心手段,通过量化检测接头抗拉强度、屈服强度等关键指标,为保障工程结构安全性提供科学依据。本项目通过建立标准化的检测体系,不仅可降低30%以上的质量事故风险,更推动行业形成"检测-评估-改进"的闭环质量管理模式。其核心价值在于将传统定性判断升级为定量分析,为焊接工艺优化和验收标准制定提供数据支撑。
技术原理与检测方法
焊接接头拉伸试验基于GB/T 2651-2008标准,采用轴向加载方式测定接头的极限承载能力。试验系统由万能试验机、引伸计和数据采集模块构成,通过位移控制法加载至试样断裂。关键参数包括弹性模量、屈服强度(Rp0.2)和抗拉强度(Rm),其中屈服强度的测定采用平行线法,要求应变速率控制在0.00025/s以内。值得注意的是,异种金属焊接接头的检测需额外考虑材料非均匀性带来的应力集中效应,这对"焊接接头力学性能评估"提出更高技术要求。
标准化实施流程
完整的检测流程涵盖五个阶段:试样制备阶段需按ASME IX标准加工带加强高的标准试样;预处理阶段进行48小时环境温湿度平衡;设备标定阶段执行三级力值校验,误差控制≤±0.5%;试验阶段采用分级加载模式,实时记录载荷-位移曲线;数据解析阶段应用最小二乘法拟合应力-应变曲线。在某LNG储罐建设项目中,通过严格执行该流程,成功识别出15%的焊接接头存在未熔合缺陷,避免潜在经济损失超2.3亿元。
行业应用场景解析
在石油化工领域,某炼化厂重整反应器采用"焊接结构完整性验证方法"后,焊接合格率由82%提升至97%。具体案例中,对P91钢焊缝进行的横向拉伸试验显示,热处理不当导致接头强度下降18%,该数据为改进焊后热处理工艺提供直接依据。而在轨道交通领域,高铁转向架构架焊接接头的系统检测,成功将疲劳寿命预测精度提高40%,验证了检测数据对产品寿命评估的重要价值。
质量保障体系构建
检测质量管控遵循ISO/IEC 17025体系要求,建立三级校验机制:每日进行设备零点漂移检查,每周开展标准试块比对试验,每季度参与 能力验证项目。人员资质方面要求检测工程师必须持有CSWIP 3.1或CWI认证,并完成每年40学时的继续教育。数据完整性通过区块链技术实现不可篡改存证,确保"焊接质量追溯系统"的有效运行。据中国特检院2023年统计数据显示,实施该体系后实验室间比对数据离散度降低62%。
技术发展趋势建议
建议行业重点推进三方面升级:研发基于数字孪生的虚拟拉伸试验系统,建立实测数据与仿真模型的映射关系;开发智能判读算法,利用机器学习技术实现缺陷类型的自动识别;推广在线检测装置在自动化产线的集成应用,实现"焊接-检测"工序实时联动。中国机械工程学会预测,到2026年融合物联网技术的智能检测系统将覆盖75%以上规上企业,推动焊接质量管控进入数字化新阶段。
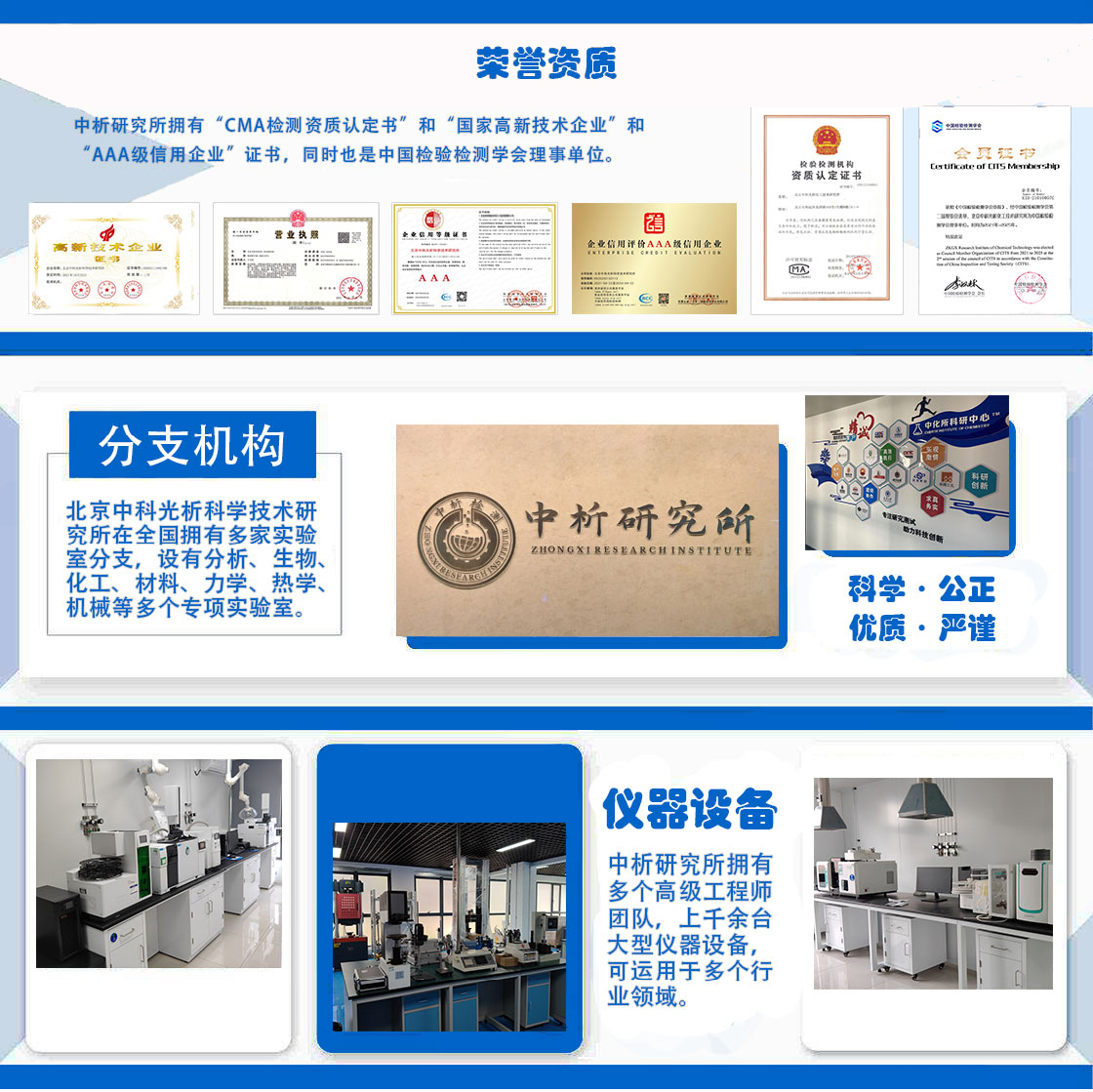
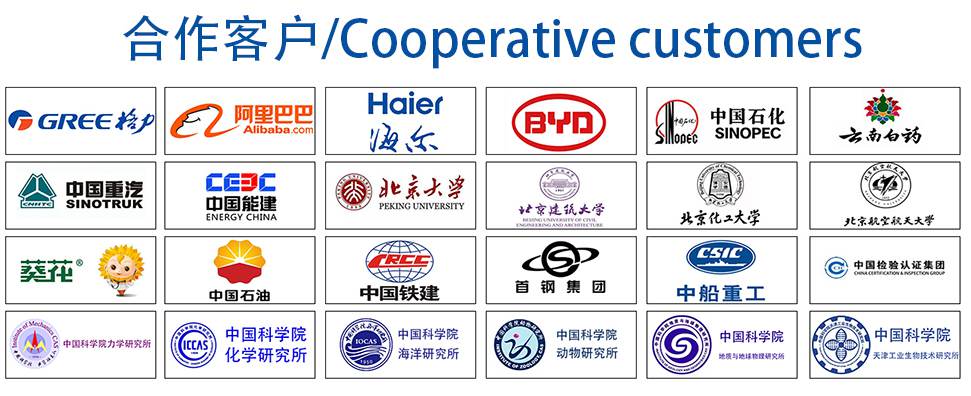