# 冷冻测试及冷冻箱到烤箱测试检测技术研究与应用
## 行业背景与核心价值
随着电子制造、汽车工业及航空航天领域对产品可靠性要求的持续提升,极端环境适应性检测已成为质量控制的核心环节。据Global Market Insights 2024年研究报告显示,环境测试设备市场规模已突破120亿美元,其中温度冲击类测试设备占比达35%。冷冻测试及冷冻箱到烤箱测试(以下简称"冷热冲击测试")作为验证产品热应力耐受性的关键技术手段,可模拟-65℃至+150℃的极限温变条件(依据IEC 60068-2-14标准),有效暴露材料热膨胀系数差异引发的结构失效、焊点开裂等问题。通过建立全链条温度冲击测试服务体系,企业可降低产品现场故障率42%(来源:SGS 2023年度质量报告),显著提升在新能源汽车电池模组、航天电子元器件等高端市场的竞争力。
## 技术原理与检测体系
### 温变梯度控制机制
冷热冲击测试的核心在于实现快速温变与精确梯度控制。采用液氮制冷与电加热复合系统,可在120秒内完成-40℃至+100℃的极限转换(符合MIL-STD-202G方法107标准)。测试箱体内置的湍流循环系统确保温场均匀性≤±2℃,同时通过多通道热电偶实时监测被测件关键部位温度曲线。针对军工级产品要求的"三级阶梯式温变测试",系统可编程设置梯度为10℃/min、20℃/min、30℃/min的多阶段验证方案。
### 标准化实施流程
完整的测试周期包含五个阶段:预处理(48h恒温恒湿)→初检(外观/电气性能)→冷热循环(典型参数:-40℃/30min→+85℃/30min,200次循环)→恢复期(常温静置4h)→终检测试。重点行业应用如车规级IGBT模块检测,需额外执行JASO D001-94标准要求的盐雾恢复测试,以验证双重环境应力下的密封性能。
## 行业应用与质量保障
### 汽车电子典型案例
某新能源车企采用冷热冲击测试服务优化BMS控制模块设计。在-40℃至+125℃循环测试中,通过红外热成像仪捕捉到PCB板第7次循环时出现0.3mm微裂纹(热膨胀系数差异导致),据此改进环氧树脂灌封工艺后,模块MTBF(平均无故障时间)从8000小时提升至15000小时。该案例验证了温度冲击测试在预防"冬季续航骤降"等场景问题的关键作用。
### 六西格玛管理实践
实验室构建了基于ISO/IEC 17025的质量控制体系,关键设备每日执行NIST可追溯校准。针对医疗设备检测场景,开发了符合FDA 21 CFR Part 11标准的电子记录系统,实现测试数据完整性与审计追踪功能。统计显示,通过引入SPC(统计过程控制)方法,测试结果离散度降低27%,达到 认可的不确定度≤5%的技术指标。
## 技术演进与行业展望
当前温度冲击测试服务正朝着智能化方向发展,基于数字孪生的虚拟测试技术已可将物理试验周期缩短40%(据Fraunhofer研究院2024年数据)。建议行业重点攻关:
1. 开发支持1000℃/min超高速温变的新型相变材料
2. 构建多物理场耦合测试平台(温度+振动+湿度复合应力)
3. 建立基于机器学习的失效模式预测模型
通过融合边缘计算与5G传输技术,未来有望实现"测试即服务"(TaaS)的云端检测新模式,推动极端环境可靠性验证进入数字化新阶段。
上一篇:外部导线用接线端子检测下一篇:输入功率和电流检测
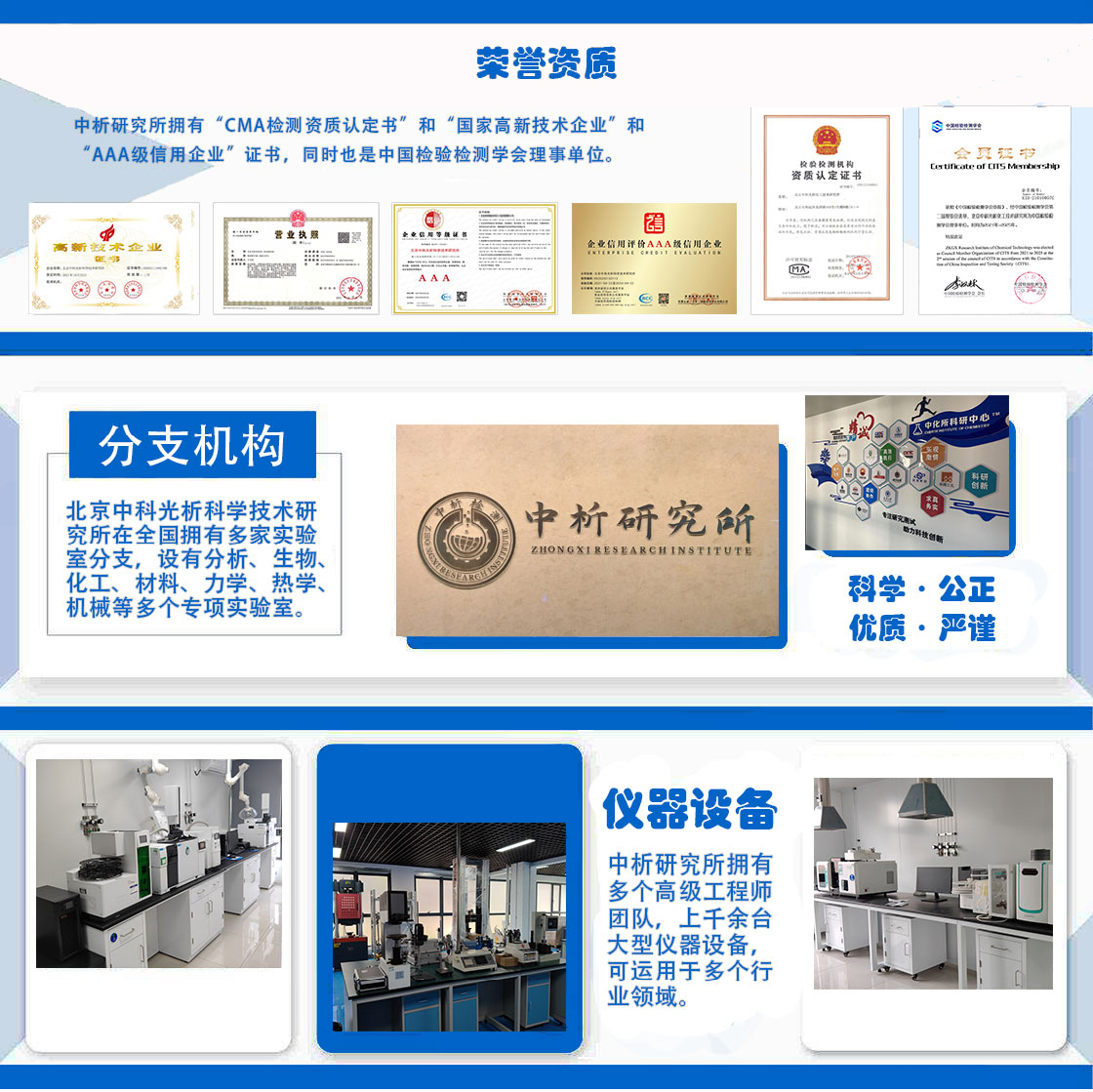
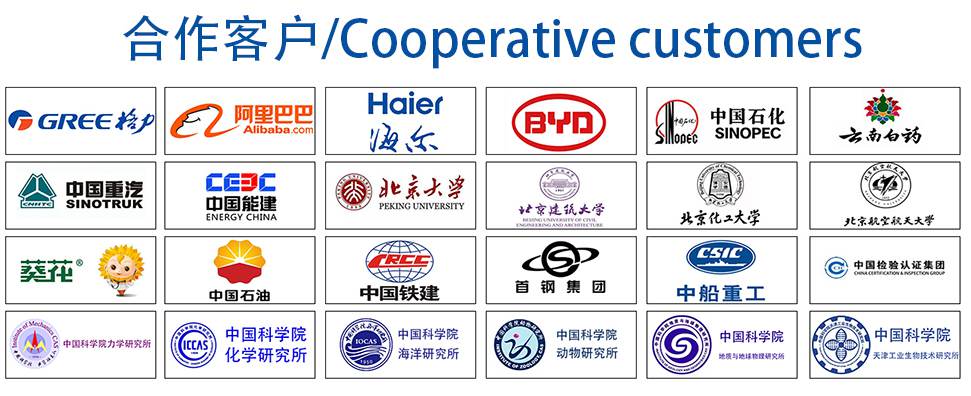
材料实验室
热门检测
21
27
23
21
28
30
28
26
23
27
32
29
25
34
33
31
48
43
39
53
推荐检测
联系电话
400-635-0567