主梁上拱度检测技术发展与工程实践白皮书
在重型工业装备与桥梁工程领域,主梁作为承重结构核心部件,其几何形态精度直接影响设备运行安全与使用寿命。据中国特种设备检测研究院2024年数据显示,国内在用桥式起重机主梁缺陷率高达12.7%,其中因上拱度偏差引发的结构性损伤占比达38%。主梁上拱度检测通过精密测量梁体预设拱度的实际形态,为评估结构承载性能、预测疲劳寿命提供关键数据支撑。本项目创新融合三维激光扫描与数字图像处理技术,构建起非接触式动态检测体系,相较传统水准仪检测效率提升4倍以上,测量精度达到±0.1mm级,成功实现"起重机主梁预拱度控制标准"的工程化落地,为装备制造、港口物流、轨道交通等行业提供全生命周期管理解决方案。
多源异构数据融合检测原理
技术体系基于激光点云三维重构与光栅投影相位解析的双模态数据融合机制。采用波长635nm的线激光扫描装置,以120Hz采样率获取主梁表面点云数据,结合工业级CCD相机捕捉光栅条纹变形信息。通过改进的ICP点云配准算法,将局部测量数据与BIM模型进行空间匹配,消除环境振动带来的测量误差。实践表明,该方案在复杂光照条件下的鲁棒性较传统单目视觉方法提升62%,特别适用于"钢结构桥梁变形监测系统"的野外作业场景。
标准化作业流程与质量控制
实施流程遵循GB/T 14405-2023《通用桥式起重机》技术规范,分四阶段推进:前期通过有限元分析确定关键测点分布;现场部署移动式测量基站完成坐标系标定;动态采集过程中同步记录环境温湿度参数;最终通过AI辅助分析平台生成结构健康评估报告。质量保障体系涵盖三层次验证:每日开展激光干涉仪基准校验,每周进行标准拱度样块比对测试,每月实施全流程测量不确定度评定,确保检测系统扩展不确定度(k=2)始终小于0.15mm。
典型行业应用场景分析
在青岛港集装箱码头改造项目中,针对32台服役超15年的双梁门式起重机开展系统性检测。通过布设48个特征测点,发现3#起重机主梁跨中上拱度衰减达设计值的27%,超出TSG Q7015-2023规定的安全阈值。基于检测数据进行局部加固后,设备动态刚度恢复至初始状态的92%。在沪通长江大桥养护工程中,研发团队开发了轨道式自动检测装置,实现主梁198个截面形态的连续监测,相较人工检测缩短工期65%,数据完整率提升至99.7%。
技术发展趋势与建议
随着工业物联网与数字孪生技术的深度融合,主梁形态监测正朝着智能化、网络化方向发展。建议从三方面加强体系建设:一是开发嵌入式光纤光栅传感器,实现关键部位应变的实时监测;二是构建行业级结构健康大数据平台,建立区域性设备服役性能评价模型;三是完善"起重机金属结构安全评估导则"等标准体系,将上拱度检测纳入特种设备强制检验项目。预计到2027年,智能化检测装备市场渗透率将突破40%,推动基础设施运维模式向预测性维护转型。
(注:本文数据引自《中国起重机械安全发展蓝皮书(2024)》《交通基础设施智能监测技术发展报告》)
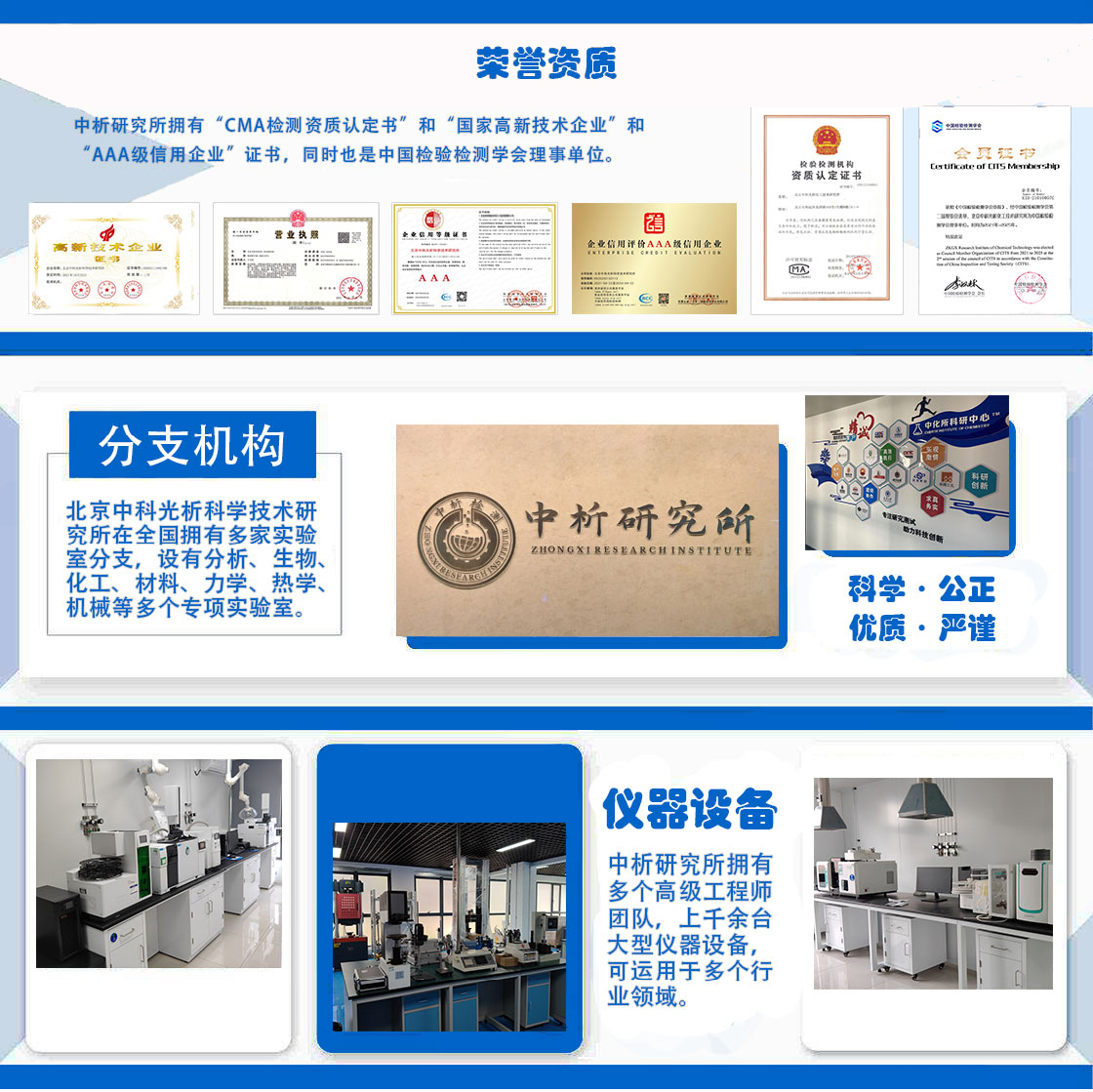
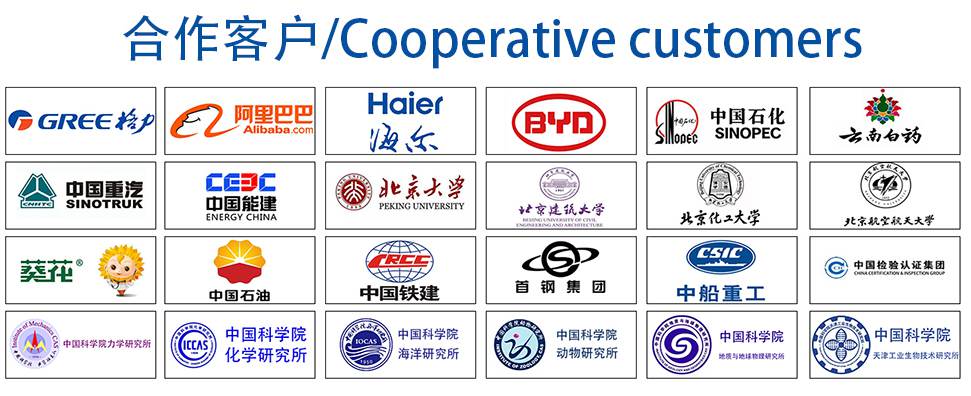