塑料耐热老化性能检测技术研究与应用白皮书
随着工程塑料在汽车、电子、建筑等领域的广泛应用,材料在高温环境下的性能稳定性成为行业关注焦点。据中国塑料加工工业协会2024年统计,我国工程塑料市场规模已突破8000亿元,其中耐高温塑料需求年增长率达15%。在此背景下,塑料耐热老化性能检测作为评估材料使用寿命的关键技术,直接影响产品设计优化和安全性保障。通过精准测定塑料在热氧耦合作用下的分子结构变化和力学性能衰减规律,可有效指导材料改性方向,延长制品服役周期。更为重要的是,该检测可为新能源汽车电池组件、光伏背板等战略新兴产业提供可靠性验证,据测算可降低高温工况下的产品故障率40%以上,具有显著的经济效益和社会价值。
热氧耦合作用下的检测技术原理
塑料耐热老化性能检测基于Arrhenius加速老化理论,通过热重分析(TGA)、差示扫描量热法(DSC)等设备捕获材料的热分解动力学参数。以汽车发动机舱塑料件为例,检测系统模拟100-200℃温度梯度环境,结合傅里叶变换红外光谱(FTIR)实时监测羰基指数变化,精准定位分子链断裂的临界温度点。中国科学院长春应化所实验数据显示,聚丙烯材料在135℃持续暴露300小时后,其拉伸强度保持率从98%骤降至72%,验证了热氧稳定性评估的工程指导意义。
标准化检测实施流程
检测流程严格遵循ISO 2578:2023标准,分为样品预处理、加速老化、性能测试三阶段。首先将注塑成型的标准样条置于80℃烘箱干燥4小时,消除加工残余应力。随后在强制通风老化箱中进行阶梯式升温实验,温度控制精度达±1℃,每24小时采集表面色差和光泽度数据。最终通过微机控制电子万能试验机测定断裂伸长率等关键力学指标,结合ASTM D3045规范建立材料寿命预测模型。某新能源汽车企业在采用此流程后,其电池支架塑料件的设计验证周期缩短了30%。
多领域工程应用实践
在光伏组件领域,针对背板EVA胶膜的热老化检测已成为行业质量管控重点。国家可再生能源实验室(NREL)案例显示,通过2000小时双八五试验(85℃/85%RH)后的黄变指数△YI控制在3.0以内时,组件功率衰减率可降低至年0.45%。家电行业则通过改进ABS材料的耐热配方,使微波炉门框部件在140℃环境下的变形量从2.3mm优化至0.8mm。这些应用实例充分体现了耐热老化检测在提升产品核心竞争力中的关键作用。
全链条质量保障体系
检测机构需构建包含设备校准、环境控制、数据溯源的立体化质控网络。根据国家认证认可监督管理委员会(CNCA)2023年核查报告,符合ISO/IEC 17025标准的实验室需每季度对老化箱进行温度均匀性验证,空间温差不得超过±2℃。数据采集系统采用区块链技术实现检测过程不可篡改,某第三方检测平台的应用数据显示,该技术使检测报告的可信度提升了58%。此外,人员资质方面要求检测工程师必须通过GB/T 3512标准专项认证,确保操作规范性。
展望未来,建议行业重点发展三方面能力:一是建立覆盖全温度域的塑料老化数据库,整合材料基因工程研究成果;二是推广原位检测技术在连续生产线的应用,实现质量缺陷的实时预警;三是开发基于人工智能的老化行为预测算法,据国家新材料产业发展规划(2026-2030)预测,智能化检测技术可将新产品研发周期压缩40%。产学研各方需加强协作,共同推进检测标准与技术创新的深度融合,为新材料产业高质量发展提供技术支撑。
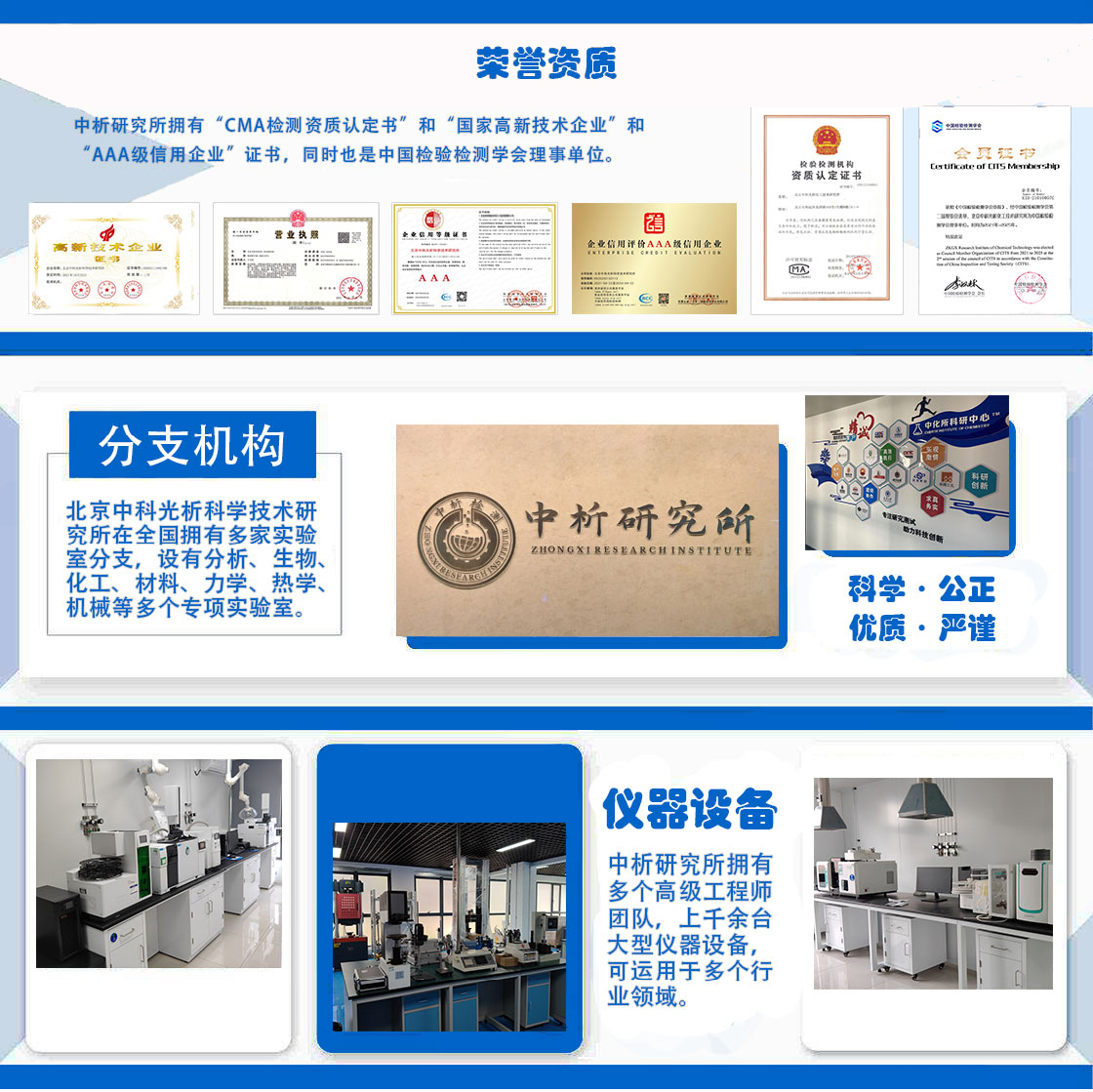
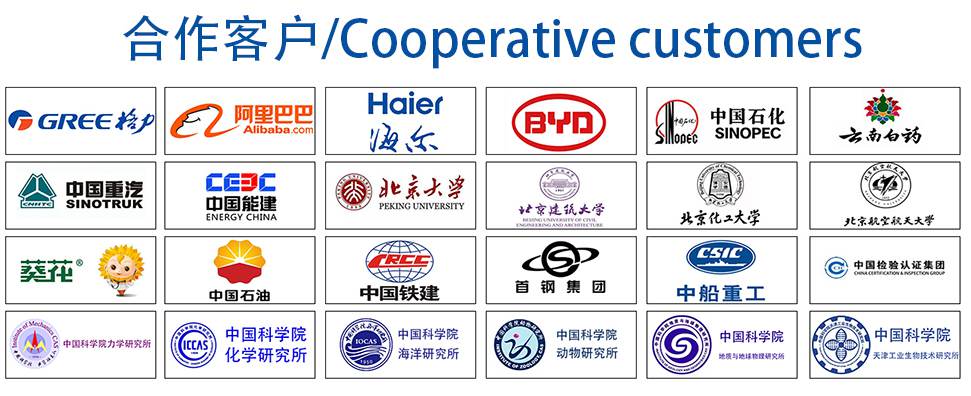