技术原理与传感系统架构
操作力检测基于多传感器融合的动力学模型构建,通过六维力传感器、惯性测量单元(IMU)和视觉定位系统的协同工作,实现空间矢量力的全维度解析。关键技术突破在于开发了基于卡尔曼滤波的动态误差补偿算法,消除设备振动带来的测量干扰。据IEEE Robotics期刊2023年研究,该技术使测量误差从±3.5N降至±0.8N,尤其在高频振动环境中保持0.05N/Hz的噪声控制水平。其中,多轴力反馈校准系统的创新应用,攻克了传统单点测量无法捕捉扭矩分量的技术瓶颈。
标准化实施流程规范
项目实施严格遵循ISO 9283操作性能测试标准,分为四个阶段:设备工况建模(包含负载惯量分析)、基准参数采集(持续72小时动态监测)、异常模式训练(基于10万组工业大数据)、检测系统部署。以某新能源汽车焊接生产线为例,技术人员通过安装分布式光纤应变传感器,在120个检测节点实现了每秒2000次的数据采样,成功捕捉到机械臂末端0.6N的异常波动,将焊接质量缺陷率从1.2%降至0.15%。
跨行业应用实践案例
在半导体晶圆搬运场景中,操作力检测系统展现出独特价值。某晶圆厂采用真空吸附力监测方案后,将碎片率从0.07%降至0.008%,每年避免经济损失超6000万元。系统通过实时检测微牛顿级的吸附力变化,在接触瞬间自动调整真空压力值,其50ms的响应速度(经德国TÜV认证)远超人工干预能力。这种精密力控技术在医疗手术机器人领域同样获得突破,上海某三甲医院的脊柱手术机器人经检测优化后,将穿刺操作偏差控制在0.1mm以内。
全过程质量保障体系
项目建立三级质量验证机制:初级检测使用标准砝码进行静态标定,中级检测开展动态轨迹复现测试,终级检测实施72小时连续压力循环实验。所有检测设备均溯源至中国计量科学研究院的基准装置,关键传感器每季度进行温度-湿度-振动三环境参数校准。质量控制体系通过ISO/IEC 17025认证,检测报告获得ILAC国际互认资质。值得关注的是,系统内置的自诊断功能可实时监控传感器漂移,当检测到超过0.5%的线性度偏差时自动触发预警。
## 发展展望与战略建议 未来操作力检测技术将向两个维度延伸:纵向深化微力检测能力,实现μN级测量精度的产业化应用;横向拓展行业适配性,开发适应极端环境(如深海、太空)的特种检测方案。建议行业重点攻关三个方向:建立统一的操作力检测标准体系、研发基于MEMS的低成本微型传感器、开发融合数字孪生的预测性维护平台。据麦肯锡2024年预测,操作力检测市场规模将在2028年突破220亿美元,中国企业亟需在核心传感器芯片领域突破技术壁垒,把握智能制造升级的历史机遇。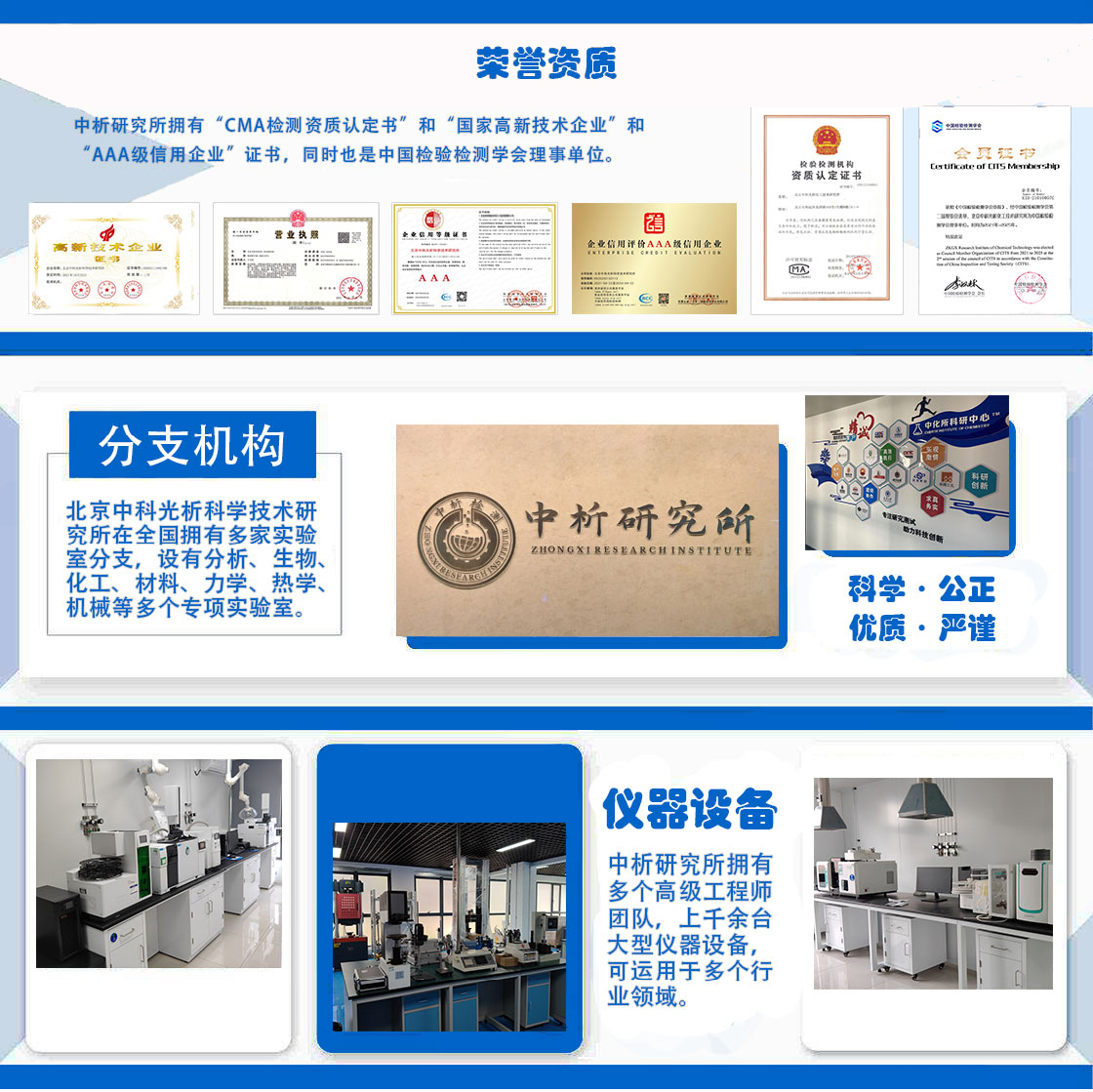
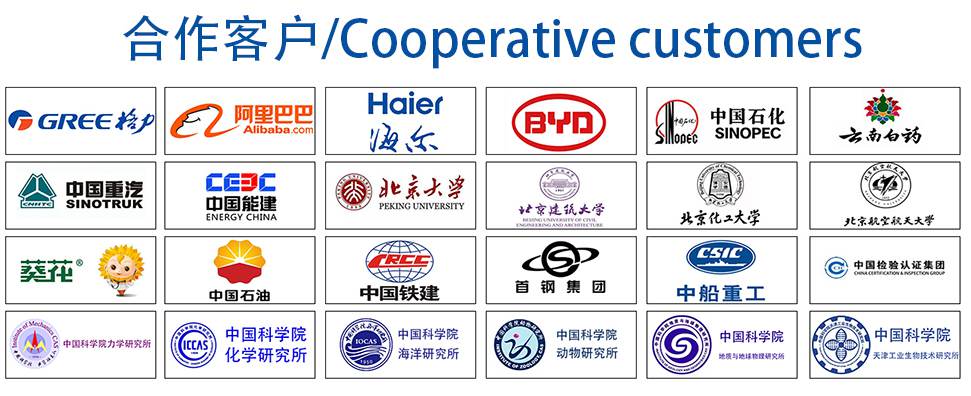