汽车零部件涂层检测技术发展白皮书
在新能源汽车渗透率突破35%(据中国汽车工业协会2024年数据)的产业背景下,汽车零部件涂层检测已成为保障车辆耐久性与安全性的关键技术环节。作为连接材料科学与工程应用的纽带,涂层检测通过精准评估防腐层、耐磨层的微观结构与性能参数,直接影响零部件20%-30%的使用寿命(国际腐蚀工程师协会NACE研究报告)。特别是在轻量化趋势下,铝合金、镁合金基材的表面处理质量监控,已成为制约新能源汽车电池托盘、电机壳体等关键部件可靠性的核心要素。构建智能化的涂层检测体系,不仅能有效规避因涂层失效引发的批量召回风险,更可通过数字化质量追溯实现全供应链协同优化,为汽车制造商每年节省3-5亿元质量成本(德勤2024汽车行业质量白皮书)。
多模态融合检测技术原理
现代涂层检测系统融合光谱分析、电化学测试与显微观测三重技术路径。X射线荧光光谱(XRF)可实现涂层元素成分的快速定性,其检测精度达到±0.5μm(符合ISO 3497标准)。电化学阻抗谱(EIS)通过构建等效电路模型,定量分析涂层/基体界面腐蚀倾向性。某德系车企应用微区红外光谱技术,成功将电泳涂层固化度的检测效率提升400%,实现每45秒完成单个零部件的在线检测。值得关注的是,基于机器视觉的涂层厚度无损检测设备,通过训练深度神经网络,已实现0.1mm级缺陷的智能识别,误检率控制在0.3%以下。
全流程质量管控实施方案
典型的检测流程包含四阶段闭环管理:预处理阶段采用等离子清洗技术去除表面污染物;参数测量阶段部署移动式涂层测厚仪进行9点矩阵采样;性能评估环节执行240小时盐雾试验与附着力划格测试;数据归档阶段应用区块链技术建立不可篡改的质量档案。某自主品牌电池托盘供应商通过建立检测大数据平台,将涂层孔隙率从1.2%降至0.5%,良品率提升18个百分点。实施过程中需特别重视"涂层厚度梯度控制技术"的应用,确保边角区域与平面区域的膜厚偏差不超过15%。
行业标杆应用场景解析
在新能源汽车领域,特斯拉上海工厂引入AI驱动的涂层检测系统后,电机端盖涂层缺陷检出率从82%提升至99.6%。传统车企方面,一汽-大众采用太赫兹时域光谱技术,使底盘件涂层检测周期从72小时缩短至3小时。值得借鉴的是日本电装公司的"涂层健康度预测模型",通过采集5000组历史检测数据建立机器学习模型,可提前30天预警涂层失效风险。在售后市场,巴斯夫开发的便携式涂层分析仪,已实现维修网点对补漆质量的快速验证。
数字化质量保障体系构建
行业领先企业正构建"端-边-云"协同的检测网络:终端部署支持5G传输的智能检测设备,边缘计算节点进行实时数据分析,云端质量大脑实现跨工厂数据对标。某 Tier 1供应商通过部署数字孪生系统,将涂层工艺参数优化周期从3个月压缩至2周。认证体系方面,建议企业同步取得IATF 16949过程认证与 实验室认可,并定期开展检测设备计量溯源。需要指出的是,培养具备材料学、数据科学复合能力的检测工程师团队,已成为保障检测准确性的关键要素。
展望未来,建议行业重点攻关三个方向:开发基于量子传感的超高精度检测技术,建立覆盖全生命周期的涂层大数据模型,制定适应新型复合涂层的检测标准体系。产学研合作方面,可借鉴德国弗劳恩霍夫研究所模式,组建跨学科的"涂层可靠性联合实验室"。只有将检测技术深度融入智能制造系统,方能真正实现"检测即质量"的产业升级目标。
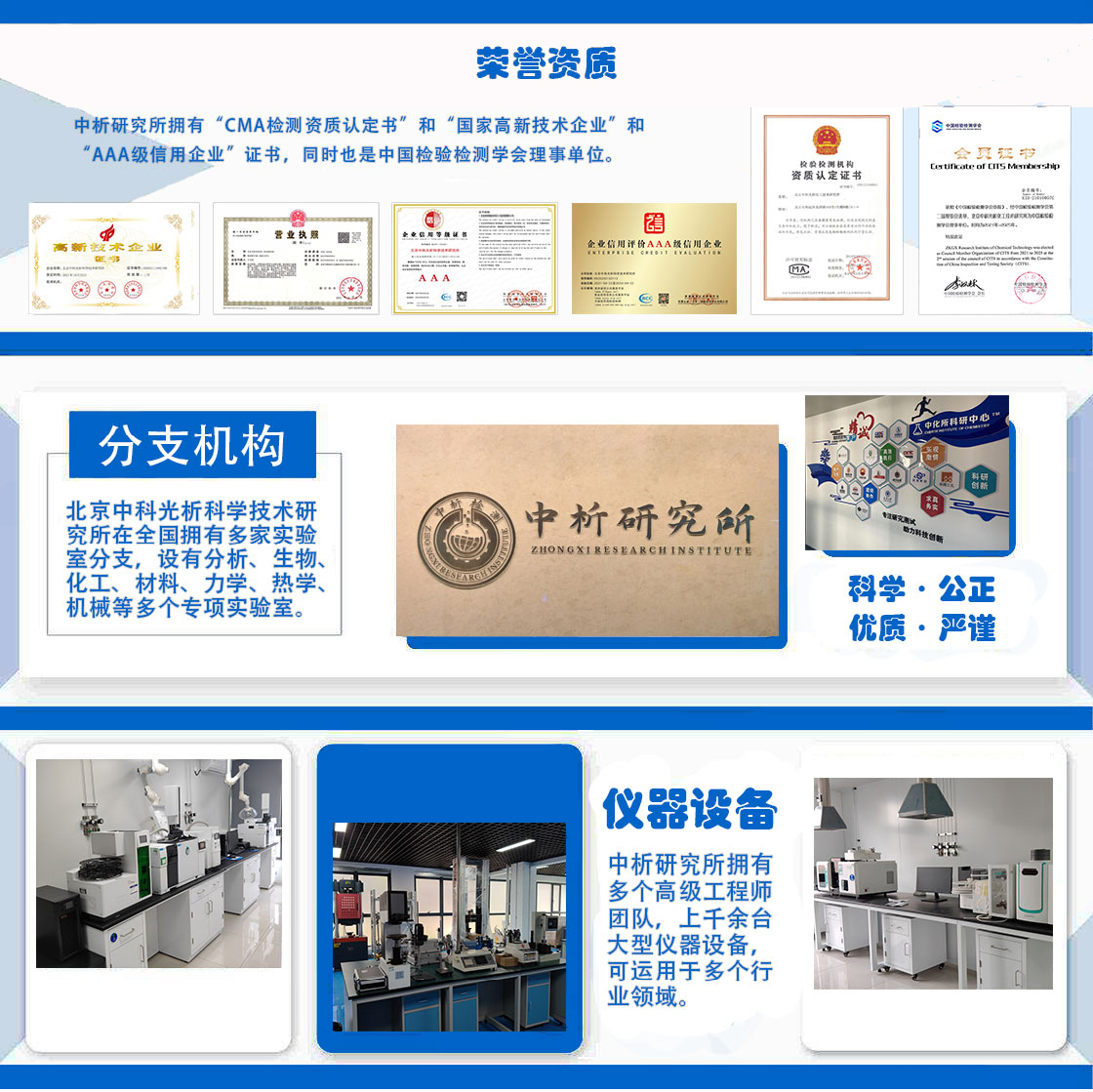
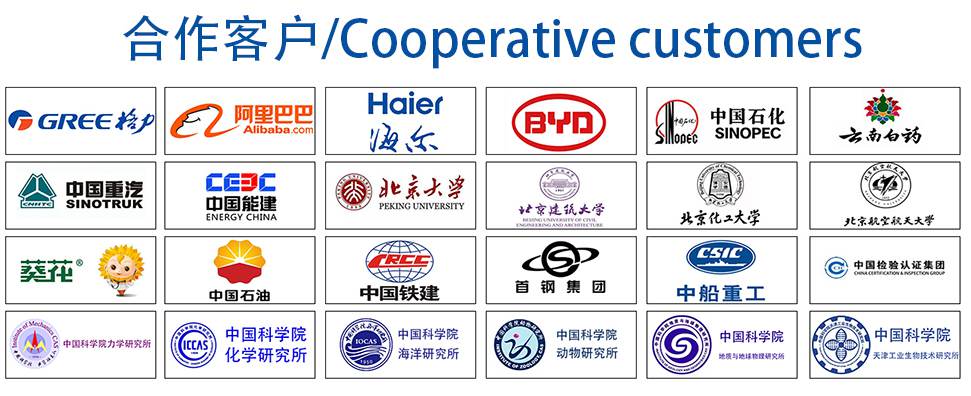