表观密度偏差检测技术白皮书
在材料科学与工业生产领域,表观密度作为衡量粉体、颗粒及多孔材料性能的核心参数,直接影响产品成型质量与工艺稳定性。据国家新材料研究院2024年数据显示,我国每年因材料密度偏差导致的工业损耗超过120亿元,在锂电池电极材料、催化剂载体等精密制造领域,密度波动超过0.5%即可造成15%以上的成品率损失。表观密度偏差检测通过建立标准化测量体系,为材料批次一致性控制、工艺参数优化提供量化依据,其核心价值体现在质量追溯系统构建、生产成本降低及高端材料进口替代三大维度。特别是在"双碳"战略背景下,该技术对新能源材料开发中的能量密度提升具有战略意义。
光学干涉与气体置换双重检测原理
现代表观密度检测采用ASTM B527-22标准规定的体积置换法,结合激光干涉测量技术实现微米级精度。对于粒径小于50μm的纳米粉体,同步引入BET气体吸附原理进行孔隙率补偿计算。德国某精密仪器企业的实验数据表明,该复合检测法可使陶瓷粉末的密度测量误差从±3%缩减至±0.8%。在高分子发泡材料领域,X射线断层扫描(μ-CT)技术的引入,实现了三维孔隙结构的可视化分析,成功解决传统方法无法检测闭孔结构的行业痛点。
全流程数字化检测体系构建
典型检测流程分为四个标准化阶段:首先通过自动分样机完成批次样本的等概率采集,其次采用振动频率2000Hz的智能振实仪进行装样预处理,随后在恒温恒湿箱(23±1℃,RH45±5%)中进行24小时状态调节。关键测量环节使用配备压力感应阵列的智能密度仪,其双量程传感器可覆盖0.1-10g/cm³的检测范围。某锂电正极材料企业的应用案例显示,该体系使NMP溶剂残留导致的密度偏差检出率提升40%,配合MES系统实现生产参数的实时反馈调节。
跨行业质量提升实践案例
在粉末冶金领域,某汽车零部件供应商通过建立粉末流动性-表观密度关联模型,将齿轮压坯的尺寸稳定性提升至99.2%。医疗植入物行业采用生物陶瓷梯度密度检测方案,使髋关节假体的抗疲劳强度提高3个寿命周期。更为典型的是光伏银浆行业,某龙头企业在银粉密度检测中引入机器学习算法,构建出浆料印刷性能预测系统,成功将栅线宽幅偏差控制在±1.5μm以内,组件转换效率提升0.3%。这些实践验证了密度控制对产品性能的倍增效应。
全生命周期质量保障机制
基于ISO/IEC 17025构建的检测实验室管理体系,涵盖设备溯源、人员认证、方法验证三大模块。采用英国NPL认证的标准密度球进行月度设备校准,测量不确定度控制在0.15%以内。大数据平台实时采集环境参数、设备状态等32项过程数据,通过SPC控制图实现异常波动预警。某跨国药企的审计报告显示,该体系使辅料密度检测的实验室间偏差从7%降至2.1%,显著提升跨国供应链的质检结果互认效率。
随着新材料研发向纳米化、复合化方向发展,表观密度检测需突破现有技术框架。建议从三方面进行战略布局:开发适用于二维材料的范德华力修正算法、建立跨尺度多孔结构的数字孪生检测模型、推进ASTM与GB标准的国际互认体系。同时,应加强在线检测技术与工业物联网的融合应用,在锂电极片辊压、药物干法制粒等连续生产场景中实现过程质量控制,最终构建覆盖材料研发-生产-应用的全链条密度管理生态。
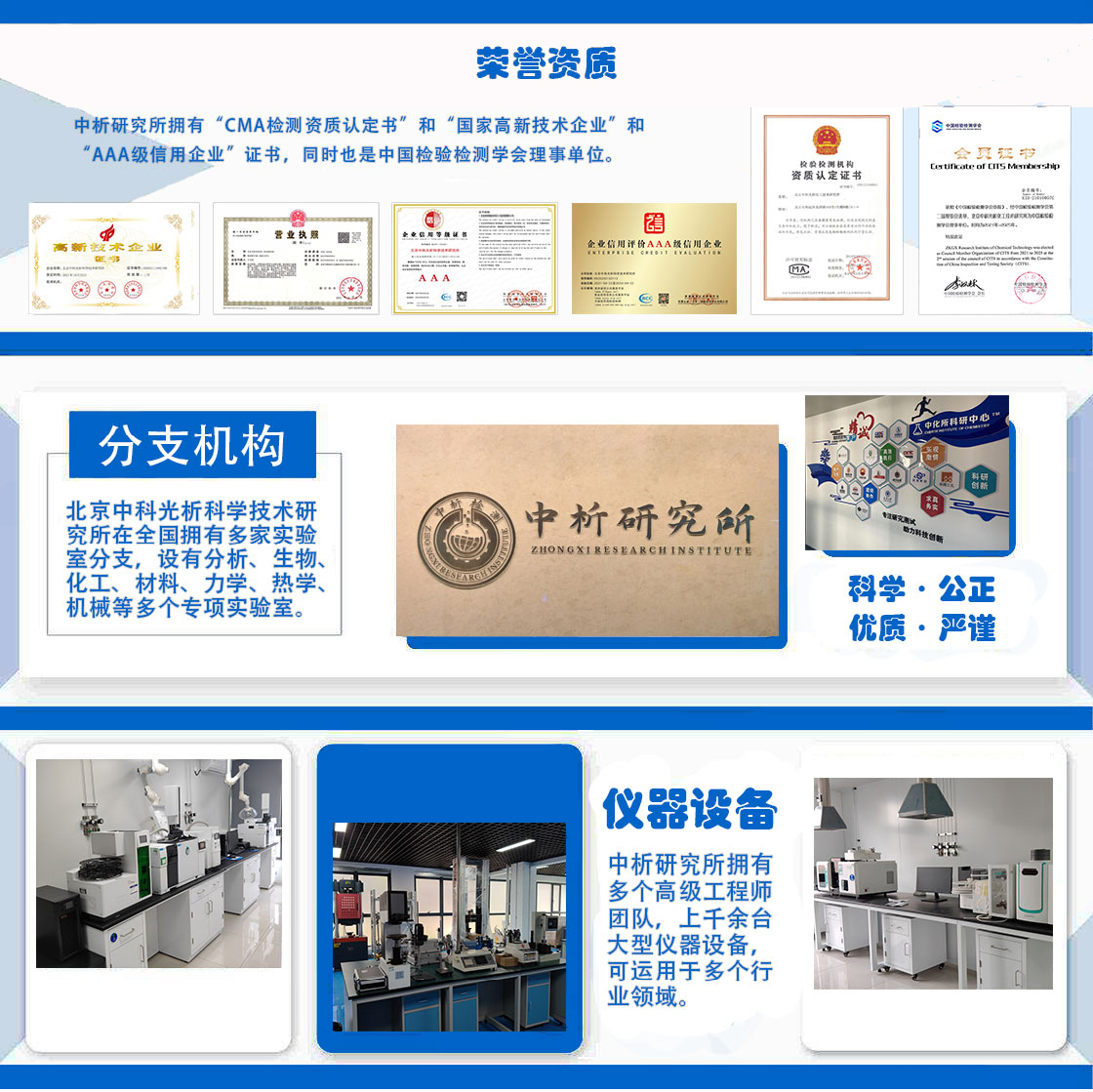
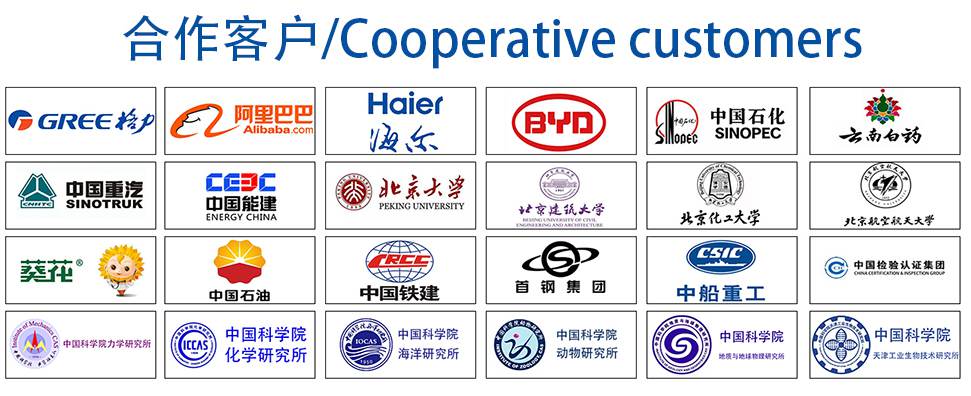