尺寸和体积密度检测在现代制造业中的关键作用与技术实践
随着工业4.0和智能制造的快速发展,尺寸和体积密度检测已成为齐全制造领域质量管控的核心环节。据中国计量科学研究院2024年发布的《高端装备制造质量白皮书》显示,我国精密零部件行业因尺寸偏差导致的质量损失年均超120亿元,而体积密度波动直接影响新能源电池、航空航天复合材料等产品的性能稳定性。实施精准的尺寸和体积密度检测不仅关系产品合格率提升,更是实现制造过程数字化、智能化的基础。通过非接触式光学测量系统和智能算法平台,企业可建立覆盖设计验证、过程监控到成品检验的全生命周期质量追溯体系,其核心价值体现在工艺优化、成本控制及标准符合性等维度,为高端装备国产化提供技术保障。
多模态融合检测技术原理
现代尺寸检测采用激光三角测量与结构光三维扫描相结合的技术方案,通过百万级像素工业相机采集物体表面点云数据,结合三维点云重构算法实现微米级精度测量。体积密度检测则融合X射线断层扫描(CT)与质量-体积换算模型,据清华大学精密仪器系实验数据,该方案对多孔材料的密度检测误差可控制在±0.3%以内。值得关注的是,基于深度学习的异常检测算法突破了传统阈值判定的局限性,在汽车发动机缸体铸造缺陷识别中实现98.7%的检出准确率,大幅提升复杂结构件的检测效率。
智能化检测实施流程
典型检测流程包含设备自动校准、多传感器数据同步采集、数字孪生建模三大阶段。以新能源汽车电池模组检测为例,首先通过激光跟踪仪建立全局坐标系,随后六轴机械臂带动线阵相机进行360°全景扫描,检测系统同步处理超过2000个特征点的尺寸数据。在航空复合材料检测场景中,采用工业CT设备每15秒可完成300×300×200mm³构件的断层扫描,结合GPU加速重建算法,3分钟内即可输出包含内部孔隙率的完整密度报告。整个流程依托MES系统实现与生产节拍的实时联动,确保检测数据与制造过程的无缝对接。
行业应用与质量保障体系
在锂电负极材料领域,体积密度检测直接关系电池能量密度指标。某头部企业引入在线X射线密度检测系统后,极片压实密度控制精度从±0.05g/cm³提升至±0.02g/cm³,据赛迪顾问2024年调研显示,该技术使电池组能量密度提升8.3%。质量保障体系方面,通过建立包含设备定期计量(符合JJF 1353-2012标准)、算法模型验证、人员技能认证的三级管控机制,确保检测结果的可追溯性。某航天部件供应商采用六西格玛管理方法,将涡轮叶片尺寸检测CPK值从1.23提升至1.67,缺陷流出率降低至0.12ppm。
技术发展趋势与行业建议
面向智能制造发展需求,建议行业重点突破三项关键技术:基于量子传感的纳米级尺寸测量、多物理场耦合的密度检测模型、检测数据与数字孪生的深度融合。德勤2024年《齐全制造趋势报告》指出,集成AI的智能检测设备市场规模将以26.5%的年增长率持续扩大。企业应加快构建包含标准数据库、智能诊断引擎的质量分析平台,同时培养兼具计量知识和AI技能的新型检测人才。值得强调的是,建立跨行业的检测标准互认体系将成为推动产业链协同创新的关键举措。
展望未来,随着5G+工业互联网的深度应用,尺寸和体积密度检测将向实时化、网络化方向发展。建议制造企业优先布局在线检测数据与工艺参数的闭环优化系统,探索区块链技术在检测报告存证中的应用,同时关注ISO 22439:2024等国际标准的更新动态,以检测技术创新驱动产品质量跃升,助力我国高端制造业实现从"合规合格"到"精准卓越"的转型升级。
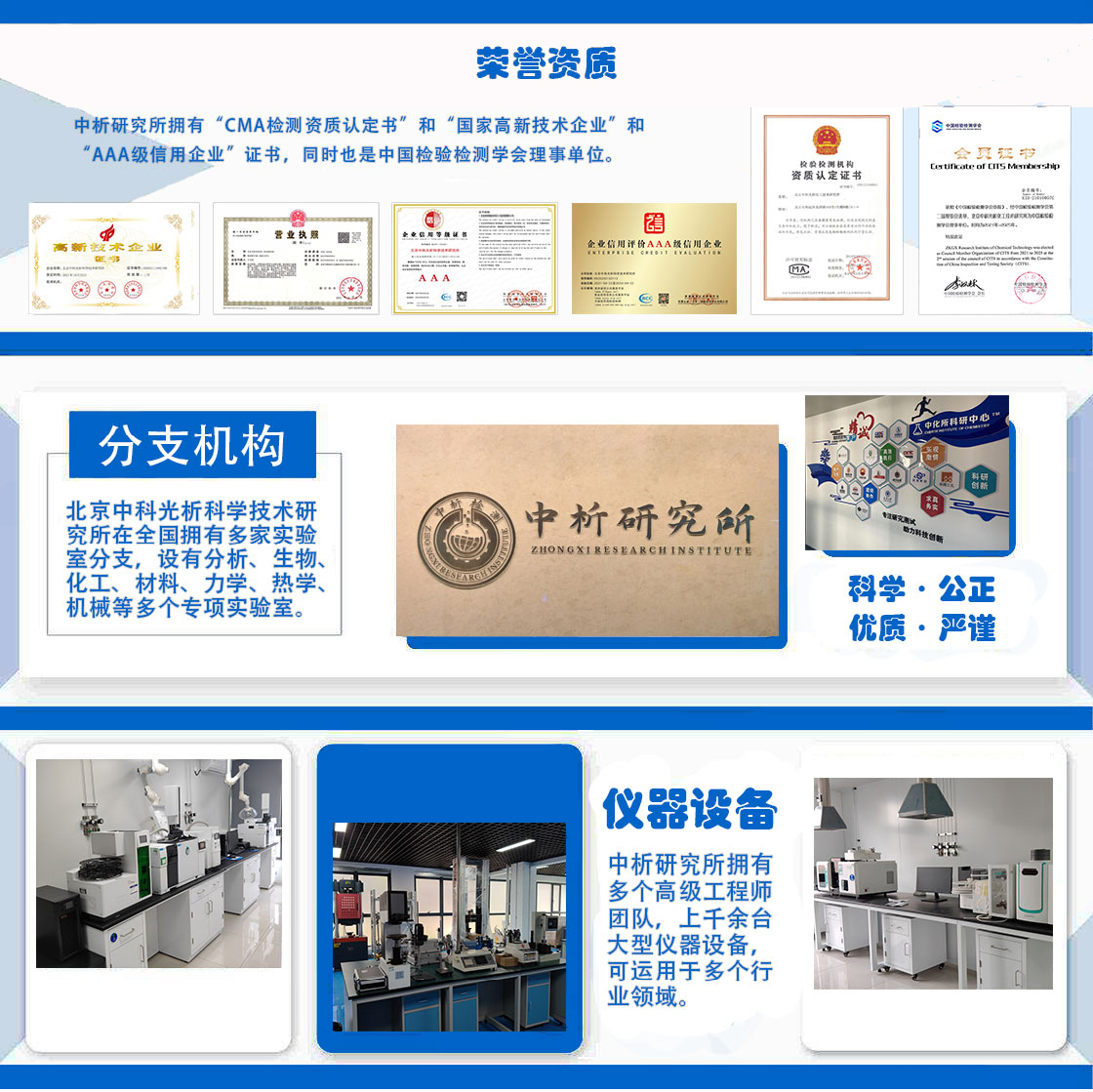
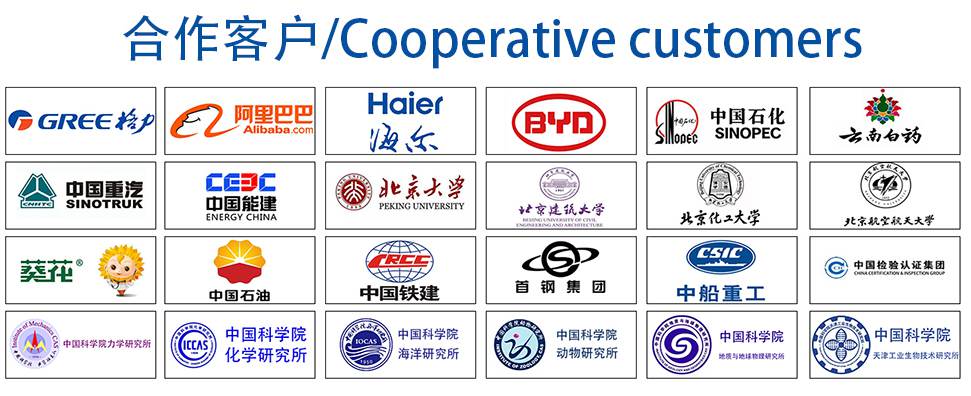