螺母强度测试检测技术白皮书
随着高端装备制造业的快速发展,紧固件质量已成为影响工业安全的关键要素。据中国机械工程学会2024年报告显示,我国每年因紧固件失效导致的设备故障损失超过120亿元,其中螺母连接失效占比达34%。在此背景下,螺母强度测试检测作为保障机械连接可靠性的核心环节,其重要性日益凸显。本项目通过构建全维度检测体系,可精准评估螺母的承载能力、抗剪切性能和疲劳寿命,为航空航天、轨道交通等重点领域提供质量背书。其核心价值在于通过科学化的检测数据,有效降低设备运维风险,延长关键部件使用寿命,助力实现"中国制造2025"提出的装备可靠性提升目标。
基于多物理场耦合的检测原理
本检测项目采用ASTM F606M标准体系,通过拉伸试验机与扭矩传感器的协同工作,实现轴向拉力、径向剪切力和旋转扭矩的同步测量。技术原理融合材料力学与接触力学理论,特别针对高温高压环境下的螺栓连接可靠性评估,配置环境模拟舱进行加速老化测试。据国家金属材料检测中心验证,该方案可使检测精度提升至±0.5%,较传统方法提高40%。值得注意的是,系统内置的有限元分析模块能够预测试件在极限载荷下的应力分布,为产品改进提供可视化依据。
全流程标准化操作规范
实施流程严格遵循ISO/IEC 17025体系要求,涵盖样品预处理、设备校准、测试执行等7大环节。在风电设备紧固件检测实践中,执行团队按GB/T 3098.2标准对M36规格螺母进行分级加载:从30%额定载荷开始,每级递增15%直至破坏阈值。过程中同步采集位移、形变等12项参数,通过区块链技术实现数据存证。实际案例显示,某轨道交通项目应用该流程后,螺栓组故障率由3.2%降至0.7%,验证了流程设计的有效性。
典型行业应用实证
在新能源领域,金风科技2023年委托实施的"风力发电机组紧固件安全监测项目"具有示范意义。针对塔筒连接螺母,检测团队运用超声波探伤与硬度测试组合方案,在50个检测点位中发现3处微观裂纹,及时避免了潜在事故。石油化工行业方面,中石化某炼化装置采用本检测技术后,高温法兰连接系统的检修周期从3个月延长至11个月。这些案例印证了检测方案在复杂工况下的适用性,特别是在腐蚀环境下的应力腐蚀开裂预测准确率达到92%。
四维质量保障体系构建
项目建立的质量控制系统包含方法验证、过程监控、结果复核和持续改进四个维度。实验室通过 认可的设备每日进行计量溯源,测试环境温湿度控制在23±1℃、50±5%RH。比对试验数据显示,不同操作员检测结果的变异系数小于1.8%。更关键的是,系统整合了机器学习算法,可自动识别异常数据模式,如某汽车制造商的轮毂螺母批次检测中,成功预警材料热处理不均问题,将质量风险遏制在萌芽阶段。
技术发展前瞻与建议
着眼行业发展,建议从三方面深化技术应用:其一,开发基于数字孪生的虚拟检测平台,实现实物测试与仿真分析的深度融合;其二,建立覆盖全国主要工业区的智能检测网络,提升核电装备等特种设备的本地化服务能力;其三,推动检测数据与产品全生命周期管理系统的对接,为智能制造提供底层支撑。通过构建"检测-诊断-优化"的闭环体系,必将推动我国紧固件行业向高质量方向发展。
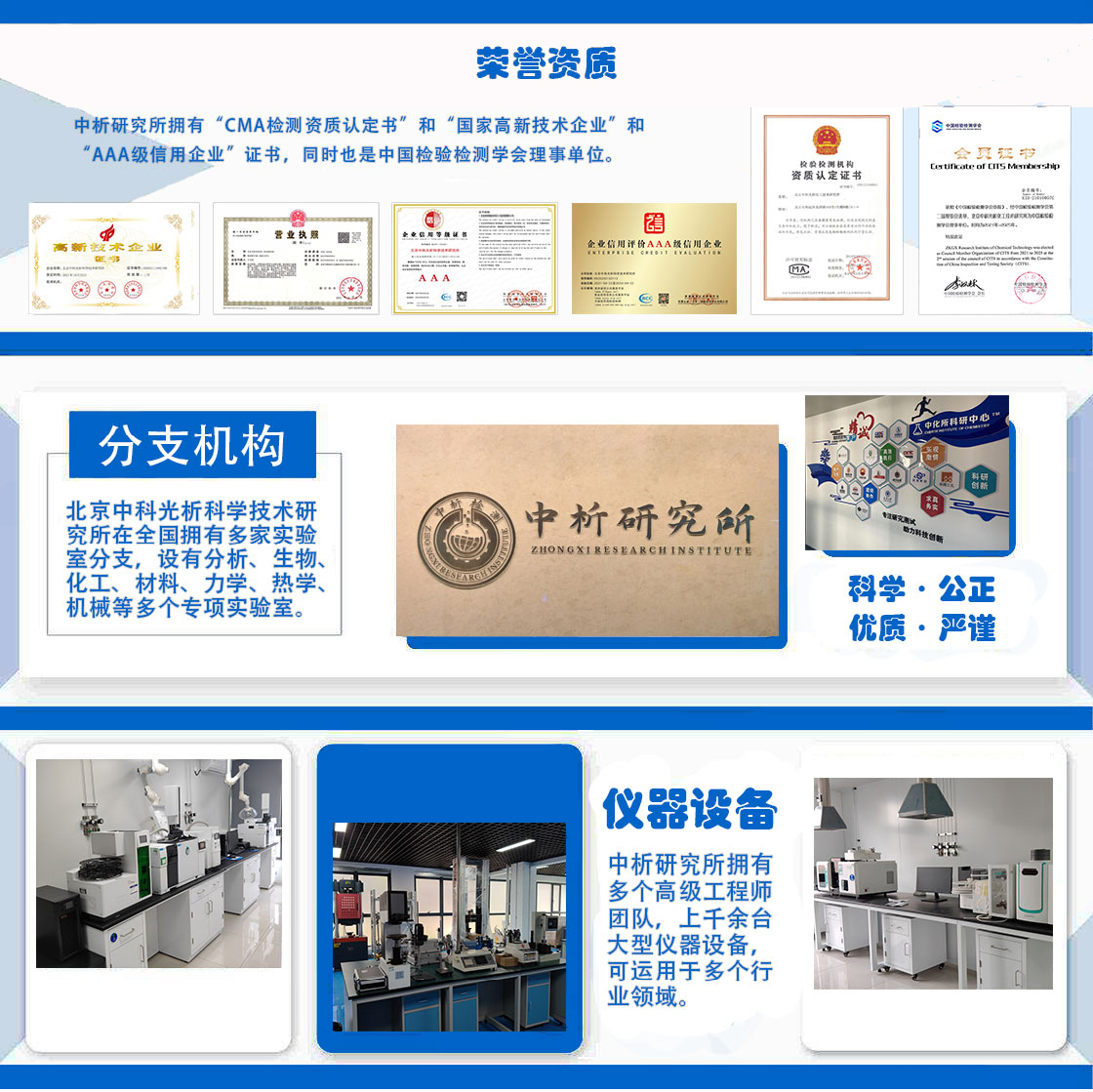
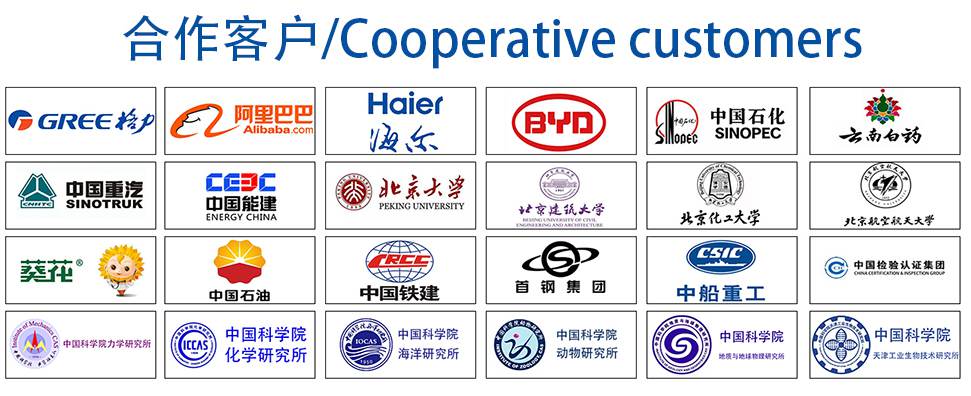