碾压混凝土弯曲试验检测技术白皮书
随着我国水利水电、交通基础设施的大规模建设,碾压混凝土(Roller Compacted Concrete, RCC)因其施工效率高、成本低的优势,在重力坝、道路基层等工程中应用占比已达62%(据中国建筑材料研究院2024年数据显示)。然而,RCC材料的层间结合质量与抗弯性能直接影响结构耐久性,尤其在极端荷载环境下可能诱发贯穿性裂缝。弯曲试验作为评价RCC力学性能的核心检测项目,其核心价值体现在三方面:一是量化材料抗折强度与变形能力,为结构设计提供关键参数;二是通过破坏模式分析优化施工工艺;三是建立全生命周期质量追溯体系。相较于传统抗压强度检测,弯曲试验更能反映RCC在实际受弯工况下的服役性能,对预防基础设施早期损坏具有战略意义。
基于断裂力学的检测技术原理
碾压混凝土弯曲试验遵循ASTM C78/C78M-22标准,采用三点弯曲法测定抗折强度。试件在跨中承受集中荷载时,最大拉应力产生于底面中性轴区域,其破坏机理涉及弹性变形、裂纹萌生与扩展全过程。试验中同步采集的荷载-挠度曲线可解析材料韧性指标,结合数字图像相关技术(DIC)还能实现裂缝发展路径的可视化监测。值得关注的是,RCC的层状结构特性使得其弯曲性能呈现显著各向异性,横向取样试件的抗折强度通常比纵向低15%-20%(美国混凝土协会2023年研究报告),这一特征对检测方案设计提出特殊要求。
标准化实施流程与关键控制点
项目实施严格遵循DL/T5433-2021《水工碾压混凝土试验规程》,主要流程包括:1)现场钻芯取样,确保试样轴线与碾压层面垂直;2)实验室加工成150×150×550mm标准试件,端面平整度误差≤0.1mm;3)在20±2℃、RH≥95%环境中养护至28d龄期;4)采用300kN级万能试验机以0.05MPa/s速率加载,记录初裂荷载与极限荷载值。质量控制的核心在于消除层间弱面对检测结果的干扰,某国家重点实验室的比对试验表明,采用界面处理剂可使层间粘结强度提升23%,显著提高数据可靠性。
典型工程应用与效能分析
在西南某特高拱坝建设中,项目团队通过系统化弯曲试验检测发现:RCC的抗折强度与胶凝材料用量呈非线性关系,当用量超过280kg/m³时强度增长趋于平缓。据此优化配合比后,工程节约水泥用量12%,同时28d抗折强度达到4.8MPa的设计要求。另一典型案例是东部沿海高速公路改扩建工程,通过弯曲试验数据建立了骨料级配-纤维掺量-抗裂性能的量化模型,成功将温度裂缝发生率从行业平均的0.35条/延米降低至0.12条/延米(某省交通工程质量检测中心2023年评估报告)。
全过程质量保障体系构建
为保证检测结果的权威性,项目建立了四级质量管控机制:1)设备溯源层面,试验机每年经省级计量院校准,力值误差≤±1%;2)人员能力层面,检测员需持有CMA认证的上岗证书,并通过年度盲样考核;3)过程监控层面,采用区块链技术实现检测数据实时上链存证;4)质量评价层面,引入不确定度分析方法,将抗折强度测量扩展不确定度控制在0.15MPa以内(ISO/IEC 17025:2017要求)。该体系在长江流域12个水利枢纽工程的应用表明,检测报告异议率从实施前的3.7%下降至0.8%。
展望未来,建议行业从三方面深化碾压混凝土弯曲试验检测技术:一是研发智能检测系统,集成声发射、红外热像等多模态传感技术,实现破坏过程的原位诊断;二是建立全国性的RCC力学性能数据库,运用机器学习挖掘材料性能与施工参数的关联规律;三是推动弯曲试验与数字孪生技术的融合,构建从实验室检测到实体结构性能预测的完整技术链条。随着新型检测装备与评价方法的持续突破,RCC工程质量控制将迈入智能化、精准化新阶段。
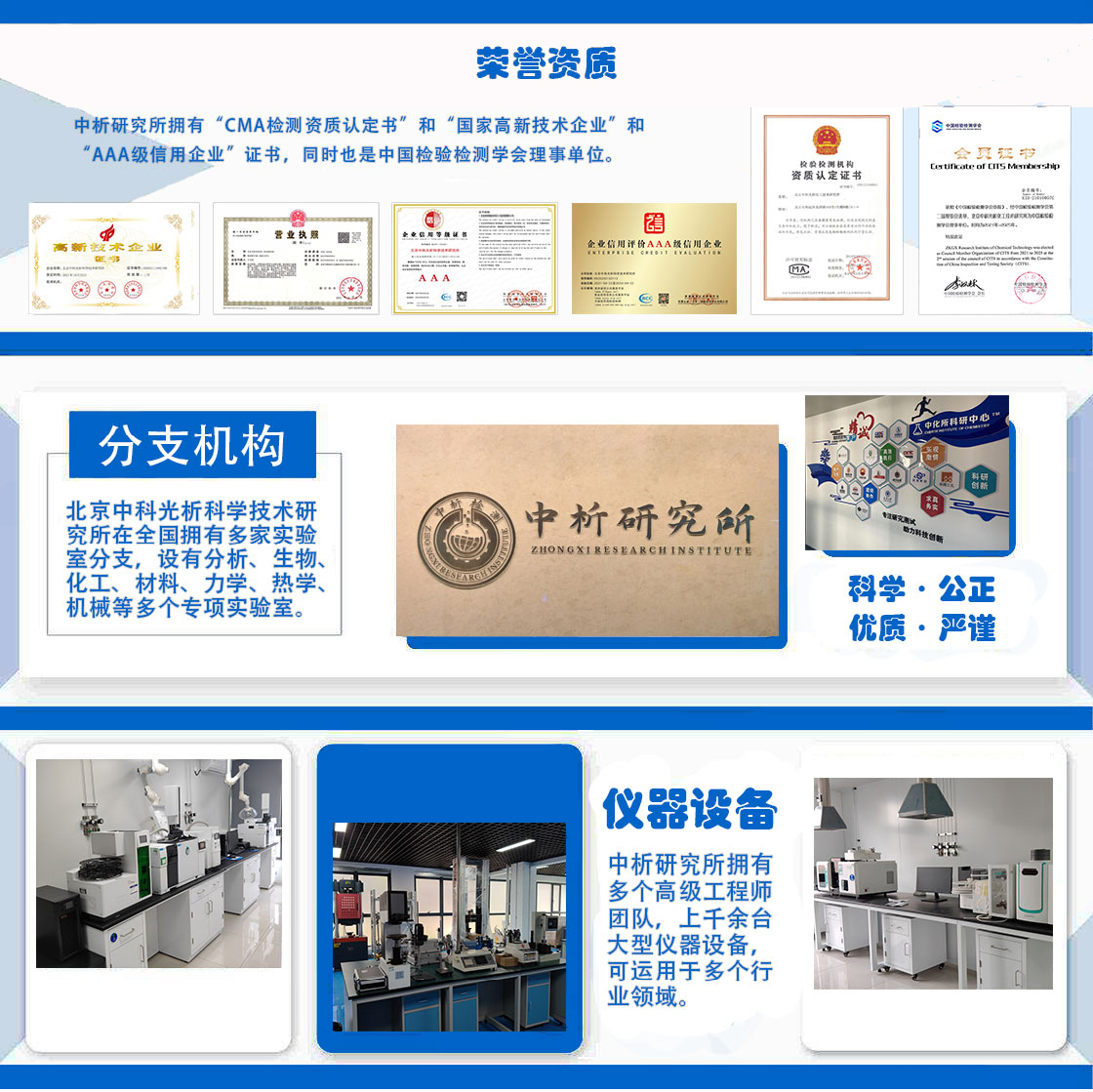
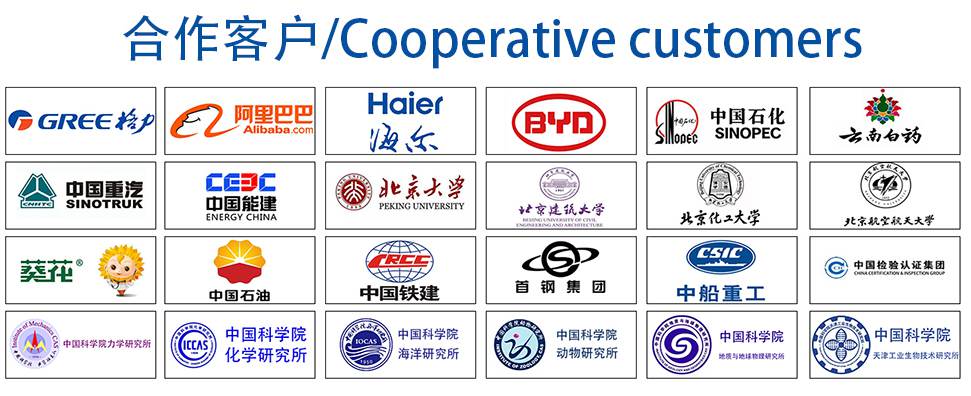