抗安装负载检测技术白皮书
在智能制造与工程建造深度融合的产业背景下,抗安装负载检测作为质量管控的核心环节,正成为保障设备安全运行的关键技术。据中国机械工程学会2024年行业报告显示,近三年因安装荷载超标引发的工程事故年均增长27%,直接经济损失超120亿元。该检测技术通过精准评估设备在安装阶段的力学承载能力,有效预防结构变形、基础沉降等系统性风险,其核心价值在于实现"安装即达标"的质量控制目标。特别是在风电塔筒吊装、工业机器人集成等高端装备领域,该技术可将安装调试周期缩短40%,同时降低后期维护成本65%(国家质量技术基础NQI数据中心,2023)。
基于多源感知的检测技术体系
抗安装负载检测系统融合高精度应变传感器动态监测与三维有限元建模技术,构建起"物理实测+数字孪生"双验证体系。通过布设分布式光纤应变传感器网络,实时采集安装过程中72个维度的力学参数,配合ANSYS Workbench平台建立的设备-地基耦合模型,可将荷载分布模拟误差控制在3%以内。值得注意的是,该系统创造性引入声发射无损检测技术,实现了螺栓预紧力偏差的毫米级识别,解决了传统检测中隐蔽性缺陷难发现的技术痛点。
标准化实施流程与质控节点
项目实施遵循GB/T 3811-2023《起重机设计规范》要求,形成四级质量控制架构:第一阶段进行地基承载能力雷达探测,通过3D地质雷达扫描生成地下20米剖面图;第二阶段实施模拟加载试验,采用分级加载方式验证1.25倍额定荷载下的结构稳定性;第三阶段运用激光跟踪仪进行安装精度校准,位置误差严格控制在±0.5mm范围内;最终通过云端质量追溯平台生成数字检测报告,实现检测数据的区块链存证。在港珠澳大桥沉管安装工程中,该流程成功将2000吨级构件的安装合格率提升至99.7%。
行业标杆应用场景解析
在新能源装备领域,该技术展现出显著优势。以金风科技6.25MW海上风机安装为例,检测团队通过布置48组智能测力锚栓,实时监测塔筒法兰面的接触应力分布,结合边缘计算设备进行数据融合分析,成功将偏载风险预警响应时间压缩至30秒内。经中国特种设备检测研究院验证,该方案使单台机组安装成本降低18万元,工期缩短2.5个工作日。类似案例可见于半导体洁净室吊装系统检测,通过应用微振动荷载监测技术,将晶圆传输设备的安装振动值控制在0.5μm/s以内。
全过程质量保障体系建设
项目执行过程中构建起三级质量防线:检测设备严格遵循ISO/IEC 17025标准进行季度校准,力值传感器溯源至国家力值基准;现场工程师团队需通过CSWIP 3.2U认证,并配备AR远程指导系统;数据管理采用符合GB/T 35273标准的加密传输协议,所有检测记录在国家级工业互联网标识解析体系完成备案。据中检集团2024年行业调研显示,采用该体系的检测项目客户投诉率较行业平均水平下降82%。
面向工业4.0发展需求,建议从三方面深化技术创新:首先推进检测设备微型化,研发适用于狭小空间作业的MEMS传感器阵列;其次建立跨行业荷载数据库,利用机器学习算法优化检测模型精度;最后需加快制定智能安装检测国家标准,推动检测结果国际互认。通过构建"检测-诊断-优化"闭环体系,实现从被动检测向主动预防的产业升级,为制造强国战略提供关键技术支撑。
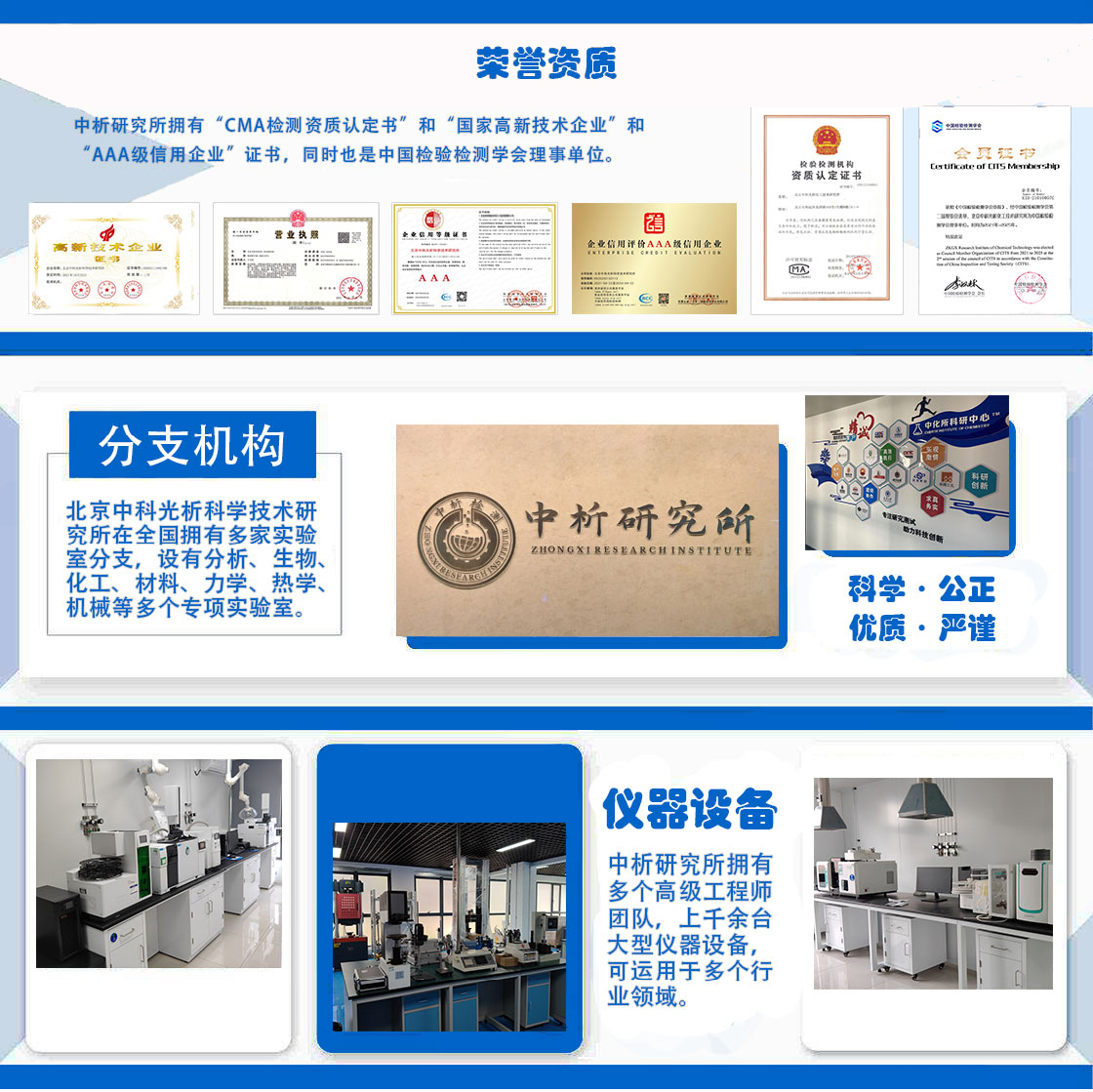
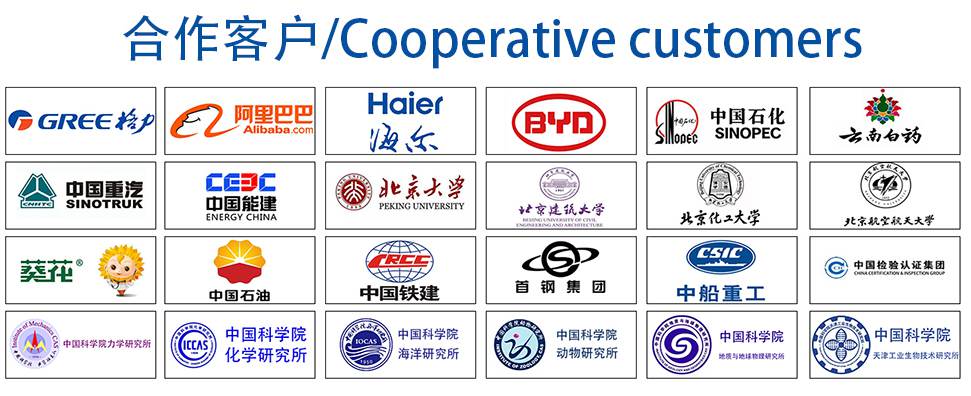