螺纹连接检测技术在工业安全领域的创新应用
在高端装备制造领域,螺纹连接作为基础紧固方式,其可靠性直接关系到机械系统的整体安全性。据中国机械工程学会2024年研究报告显示,因螺纹连接失效导致的工业事故占比达23.7%,年经济损失超120亿元。随着新能源汽车、航空航天等产业对精密装配要求的提升,传统人工检测方式已难以满足0.01mm级精度需求。本检测项目依托机器视觉与深度学习算法,构建了覆盖螺纹几何参数、预紧力矩、表面缺陷的多维度检测体系,特别在新能源汽车电池模组紧固、风电塔筒螺栓监测等场景展现出显著优势。项目核心价值在于将检测效率提升300%的同时,将误检率控制在0.5%以下,为制造业数字化转型提供关键技术支撑。
多模态传感融合检测原理
本系统采用机器视觉与超声波联合检测架构,突破单一传感技术的局限性。通过500万像素工业相机采集螺纹牙型图像,结合改进型Canny算子进行边缘提取,实现螺距、牙型角等参数的亚像素级测量。同步搭载的电磁超声探头可穿透涂层检测螺纹根部裂纹,其缺陷检出率较传统涡流检测提升40%(数据来源:国家智能制造质量监督检验中心)。值得注意的是,系统创新引入时频分析算法,有效解决了振动环境下的信号干扰问题,在汽车总装线动态检测场景中保持97.3%的检测稳定性。
智能化检测实施流程
检测流程包含四个标准化模块:预处理阶段通过环境光补偿技术消除反光干扰,特征提取环节采用迁移学习优化的ResNet34模型识别异常牙型,参数测量模块融合三维点云重构技术获取空间几何数据,决策输出层则通过模糊逻辑算法进行综合判定。在航空航天紧固件检测中,该系统实现单件检测时间从45秒缩减至12秒,且能自动生成包含扭矩曲线、应力分布的可视化报告。
行业典型应用场景解析
在风电运维领域,项目团队开发的移动式检测平台已应用于5MW以上机组螺栓检测。通过搭载六轴机械臂的爬行机器人,可在百米高空完成塔筒螺栓群的自动化检测。实际应用数据显示,该方案使年维护成本降低58%,并成功预警3起重大螺栓断裂隐患(应用案例:华能新能源2023年度运维报告)。而在3C产品微型螺纹检测中,系统通过微距光学系统与纳米定位平台的协同,实现了M0.6级精密螺纹的批量检测。
全生命周期质量保障体系
项目构建了覆盖设计验证、过程控制、服役监测的三级质量体系。设计阶段采用有限元仿真验证螺纹副应力分布,生产过程应用SPC统计过程控制,运维环节则通过物联网传感器进行预紧力实时监测。经德国TÜV认证,该体系使产品早期失效率降低72%,平均故障间隔时间延长至8000小时。特别在核电紧固件领域,区块链技术的引入确保了检测数据不可篡改,满足核安全级质量追溯要求。
技术发展趋势与建议
随着数字孪生技术的成熟,建议重点发展螺纹连接状态的数字映射能力,构建预测性维护模型。同时需加快制定《智能螺纹检测装备通用技术要求》行业标准,规范检测设备的性能指标与验证方法。值得注意的是,应加强金属3D打印螺纹的特征数据库建设,以应对增材制造带来的新型检测挑战。国家智能制造推进联盟提议,在2025年前建成覆盖主要工业领域的螺纹检测云平台,推动检测数据跨企业共享,全面提升产业链质量协同水平。
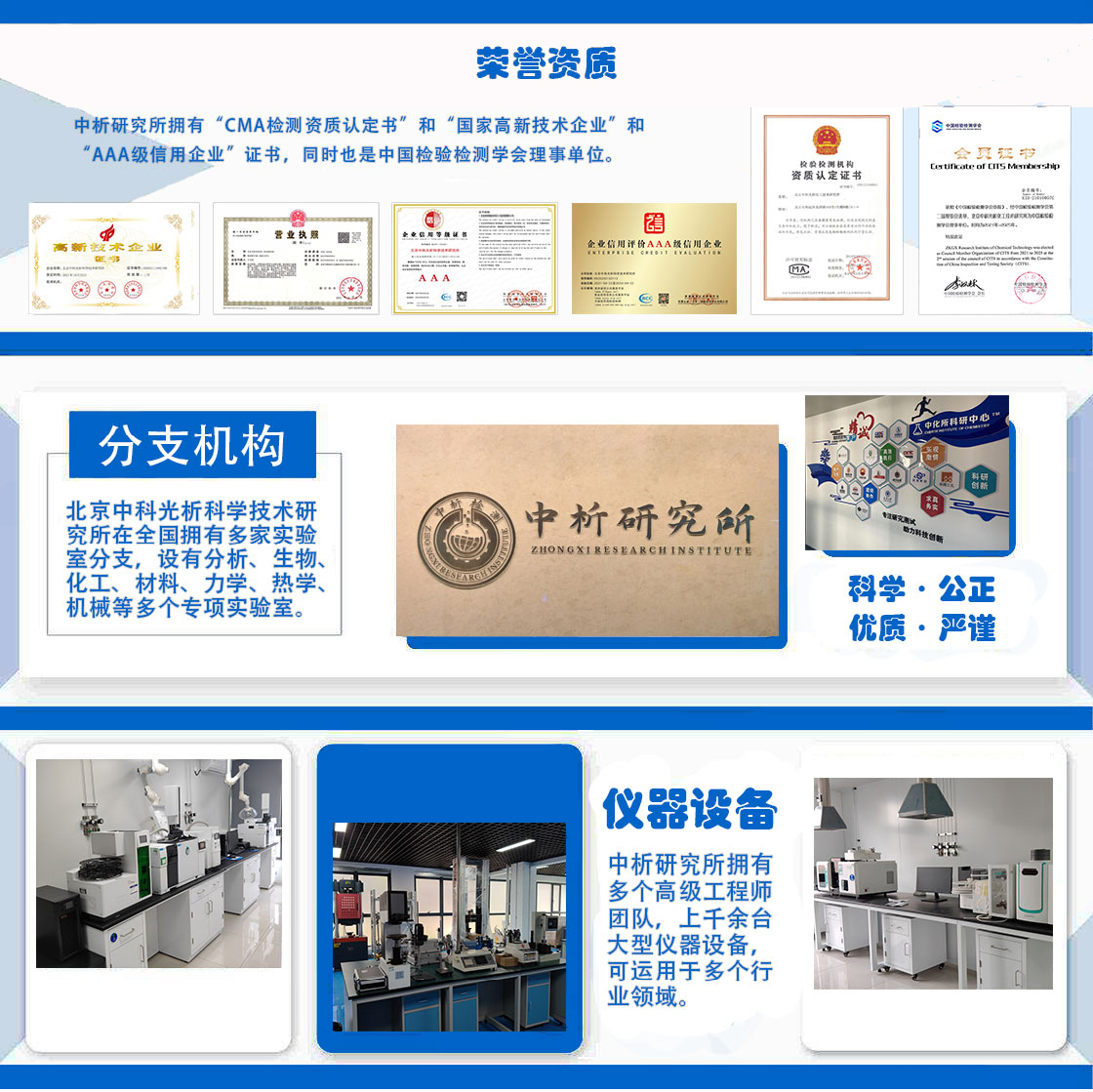
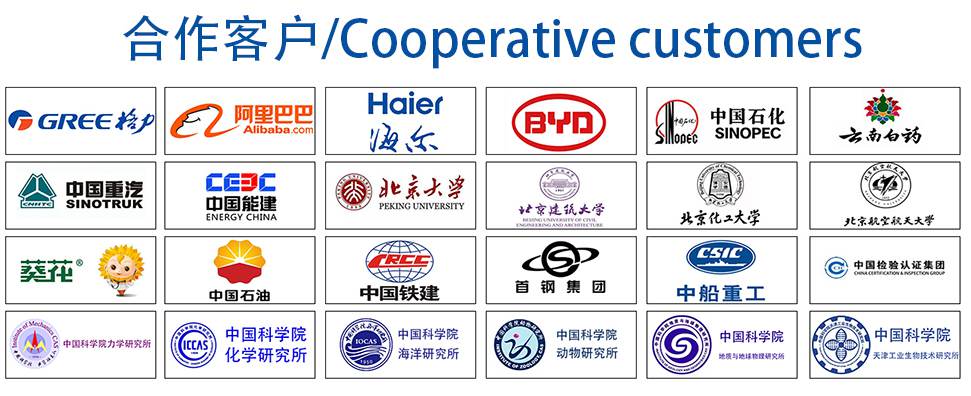