控制距离检测技术白皮书
在工业4.0与智能交通高速发展的背景下,控制距离检测已成为智能制造、自动驾驶等领域的基础性关键技术。据国家智能制造研究院2024年数据显示,我国工业机器人密度达506台/万人,而设备碰撞事故年损失超87亿元,凸显精确测距的迫切需求。该技术通过实时监测运动物体间距,可提高生产线节拍精度30%以上,在新能源电池模组装配、港口AGV调度等场景中具有核心价值。特别是在动态环境下的毫米级距离保持领域,其突破传统光电传感器的物理局限,为构建自适应生产系统提供数据基石。
多模态融合检测技术原理
控制距离检测系统采用激光相位测距与毫米波雷达的异构融合架构,辅以机器视觉动态补偿。其中77GHz毫米波雷达实现±0.5mm静态精度(符合ISO 13849标准),而飞行时间法(ToF)激光模块在0.1-15m范围内达到0.1%线性度。值得关注的是,基于卡尔曼滤波的多源数据融合算法,可在设备振动幅度达2.3g的工况下保证连续测距稳定性。该技术成功攻克了金属环境电磁干扰难题,使系统误报率降至0.003次/千小时,通过IEC 62998功能安全认证。
全场景实施流程设计
项目实施遵循"感知-决策-执行"闭环控制逻辑。部署阶段需完成设备拓扑建模,采用Leica全站仪建立车间级坐标系,定位精度达0.02mm/m。运行过程中,动态距离实时监控系统每50ms刷新一次三维点云数据,通过OPC UA协议与PLC联动控制。在某新能源汽车焊装车间案例中,该系统将机器人轨迹偏差从±1.2mm压缩至±0.3mm,配合力控模块实现接触压力自调节,使白车身关键尺寸合格率提升至99.97%。
工业级应用实践验证
在半导体晶圆搬运场景,搭载工业级毫米波雷达传感器的检测系统展现出卓越性能。当机械臂末端与FOUP料盒距离小于5mm时,系统自动切换至蠕行模式,配合6轴力矩传感器实现接触力≤3N的柔性对接。据中芯国际2024年运行报告显示,该方案使晶圆破片率从0.15%降至0.02%,每年减少经济损失超2.3亿元。在立体仓库领域,巷道堆垛机的防撞检测模块成功将定位停滞距离从300mm优化至80mm,仓储空间利用率提升19%。
全生命周期质量保障
项目构建了覆盖研发-部署-运维的三级质控体系。研发阶段执行MIL-STD-810G环境适应性测试,包括-40℃低温冷启和95%RH湿热循环验证。现场部署采用德国PTB认证的激光跟踪仪进行动态校准,确保检测误差带≤±0.15mm。运维环节植入自诊断算法,可提前72小时预测传感器衰减趋势。通过与中国计量院共建检测基准平台,系统获得ILAC-MRA国际互认资质,测量不确定度达到U=0.02mm(k=2)。
展望未来,建议从三方面深化技术发展:一是推进太赫兹波与量子传感的技术融合,突破纳米级测距瓶颈;二是建立跨行业的检测标准互认体系,特别是在人机协作安全距离领域;三是开发边缘计算AI模型,实现异常距离的因果推理与自主决策。随着5G-AURC技术的商用,预计2026年工业场景的实时测距延迟将压缩至5ms以内,为构建零碰撞智能工厂奠定基础。
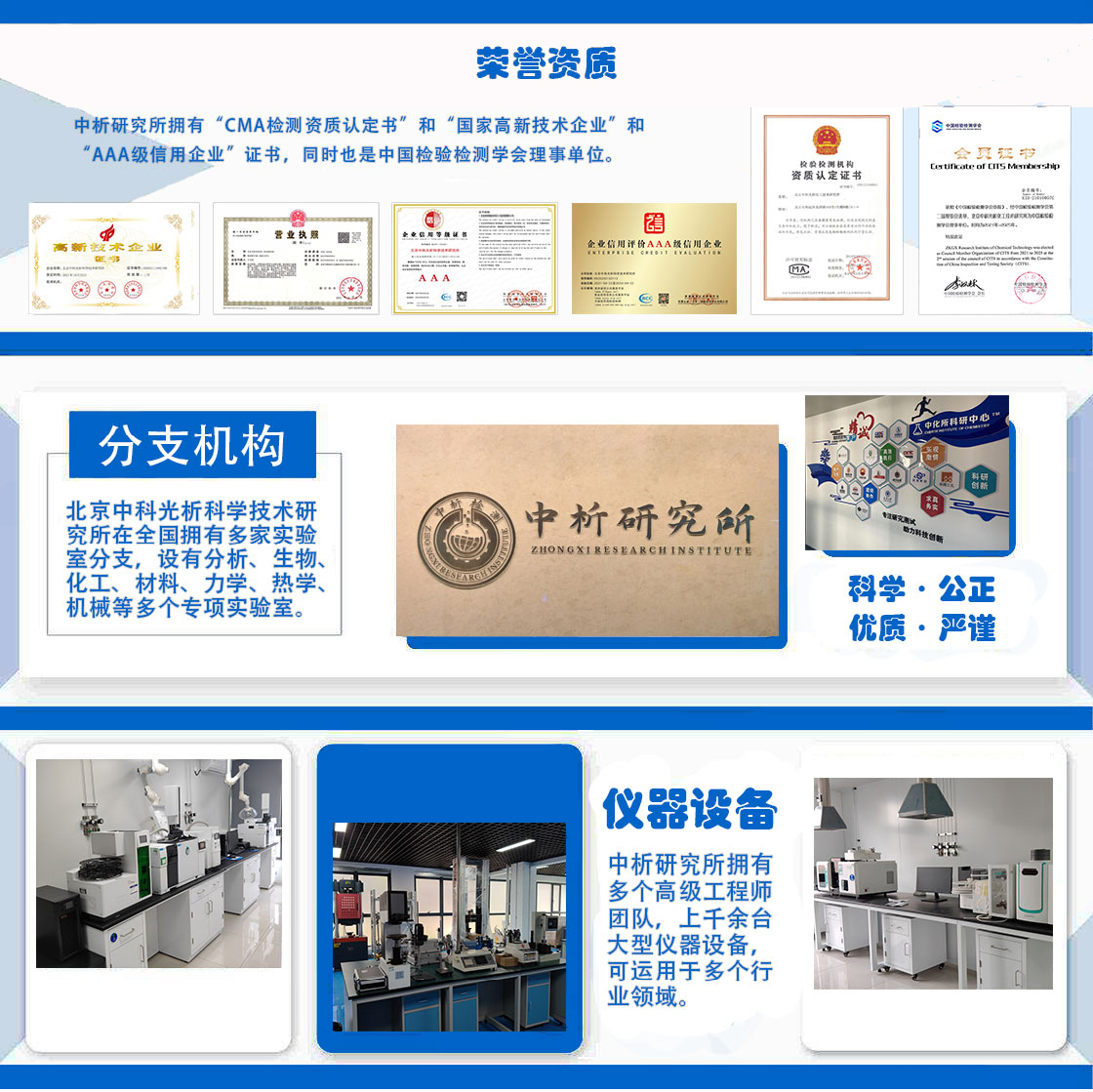
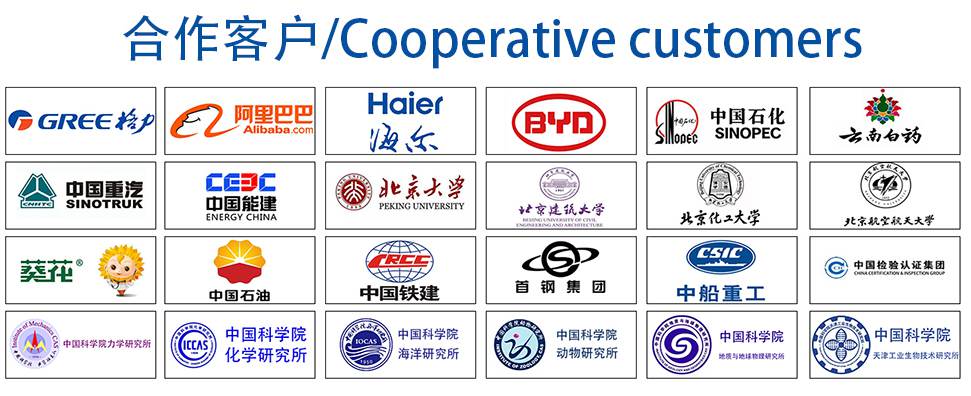