# 汽车外饰/内饰材料及零部件检测技术发展与应用白皮书
## 一、行业背景与核心价值
当前汽车产业正经历电动化、智能化双重变革,据中国汽车工业协会2024年数据显示,新能源汽车渗透率已突破42%。在此背景下,汽车外饰/内饰材料及零部件的性能检测成为保障车辆安全性和用户体验的核心环节。通过系统化的"高分子材料耐候性测试"和"车内空气质量综合评估",不仅能满足欧盟REACH法规、中国GB/T 27630等强制性标准,更能助力车企实现产品差异化竞争。该项检测体系的核心价值体现在:降低因材料失效导致的召回风险(德勤研究指出2023年相关成本占比达整车厂运营费用的2.7%)、提升消费者对"健康座舱"的感知度,以及推动新型环保材料的产业化应用。
## 二、检测技术原理及创新突破
### (一)多维检测技术体系
检测系统集成材料物理性能、化学特性及环境适应性三大模块。在物理性能层面,采用动态机械分析(DMA)评估材料在-40℃至120℃温域的弹性模量变化;化学分析则通过热脱附-气相色谱质谱联用(TD-GC/MS)精准识别挥发性有机化合物(VOC),检测灵敏度可达0.01μg/m³。值得关注的是,针对智能表面材料的"触觉反馈耐久性测试"已实现50000次循环模拟的行业突破。
### (二)智能化检测设备升级
最新研发的"多轴环境模拟仓"可同步施加温度、湿度、UV辐照及机械振动载荷,据中国汽车研究院测试报告,该设备将传统检测周期压缩40%。通过机器视觉系统对内饰件表面缺陷的识别准确率提升至99.2%,有效解决了人工目检存在的效率瓶颈。
## 三、全流程质量管控实施路径
### (一)分级检测流程设计
实施流程遵循"原料-半成品-总成件"三级管控体系:
1. 原材料阶段开展燃烧特性、雾化值等基础检测
2. 注塑成型后执行尺寸公差、色差ΔE值检测
3. 总装前进行装配应力模拟及异响测试
某德系车企采用该模式后,外饰件装配不良率从0.8%降至0.12%(数据来源:TÜV Süd 2024年质量报告)。
### (二)数字化质量追溯系统
通过植入RFID芯片实现检测数据云端存储,在比亚迪深圳工厂的实际应用中,成功将质量问题溯源时间从72小时缩短至15分钟。系统搭载的AI预测模块,能基于历史数据预警材料性能衰减趋势,准确率达89%。
## 四、行业应用与质量保障
### (一)典型应用场景解析
在蔚来ET5车型开发中,通过"高温高湿环境模拟测试"发现仪表台聚氨酯材料在85%RH环境下出现0.3mm收缩变形,及时优化材料配方避免批量问题。沃尔沃XC90项目采用"SGS整车气味评价体系",使车内苯系物浓度控制在国标限值的30%以下。
### (二)全生命周期质量保障
构建覆盖ISO 17025实验室管理体系、 认可检测方法、IATF 16949过程管控的三重保障机制。定期开展实验室间比对验证,在2023年ILAC组织的"汽车内饰件抗紫外测试"能力验证中,国内头部机构Z值评分达到0.85的国际齐全水平。
## 五、未来展望与建议
随着车载显示触控面板渗透率提升(预计2025年达68%),建议行业重点攻关"透光材料光学耐久性测试"和"抗菌涂层功效验证"等新领域。同时应加快建立基于区块链的检测数据共享平台,推动检测结果跨国互认。值得注意的是,据J.D.Power 2024年消费者调研显示,72%购车者将"环保检测认证"作为核心决策因素,这要求检测机构持续完善生物基材料、可回收材料的评价体系,为汽车产业绿色转型提供技术支撑。
上一篇:气隙间距(仅适用低压进水阀)检测下一篇:后仰试验检测
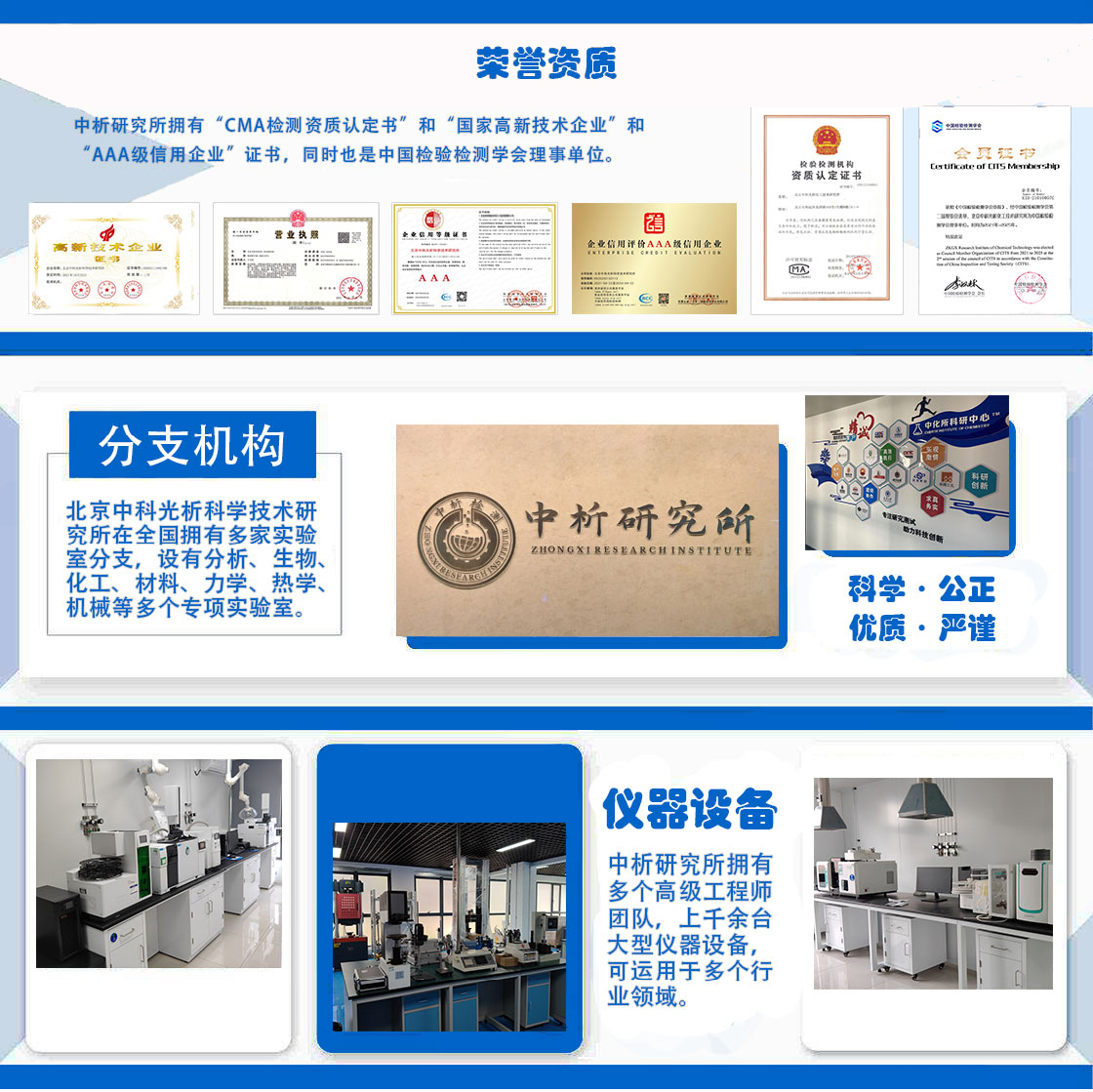
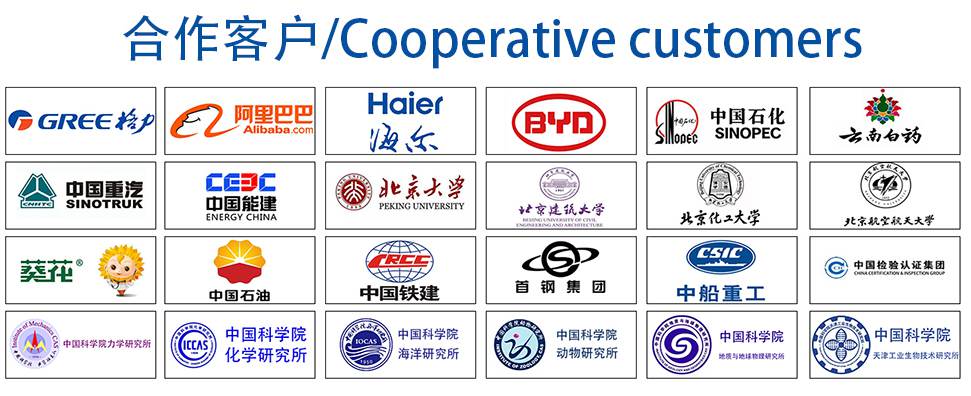
材料实验室
热门检测
8
15
15
16
19
20
19
20
23
20
23
18
20
15
22
17
20
20
23
15
推荐检测
联系电话
400-635-0567