# 机械强度试验检测技术发展与行业应用白皮书
## 引言
在制造业向高端化、智能化转型的背景下,机械强度试验检测作为产品质量的核心保障手段,已成为航空航天、轨道交通、新能源装备等领域的关键技术支撑。据中国机械工程学会2024年发布的行业报告显示,我国高端装备行业因材料失效导致的年均经济损失达127亿元,其中63%的事故源于强度设计缺陷。在此背景下,机械强度试验检测项目通过模拟实际工况下的载荷条件,有效验证产品结构完整性,其核心价值体现在缩短产品研发周期30%以上,并降低15%-20%的后期维护成本。特别是在风电叶片疲劳测试、汽车碰撞仿真等场景中,该技术为产品全生命周期管理提供了科学依据。
## 技术原理与创新突破
### h2 多物理场耦合检测体系
现代机械强度试验采用静载、动载与疲劳测试相结合的复合检测模式,集成高精度应变测量技术(精度达±0.5%FS)与数字图像相关法(DIC)。以某型航空发动机叶片测试为例,通过构建多轴协调加载系统,可同步采集温度场(0-800℃)、振动谱(5-2000Hz)与应力应变的三维数据,实现材料屈服强度、断裂韧性等12项关键参数的精准测定。国家材料测试中心2023年验证数据显示,该体系使钛合金构件检测误差从传统方法的8.3%降至1.7%。
## 标准化实施流程
### h2 全生命周期检测路径
项目执行严格遵循ASTM E8/E8M-24和ISO 6892-1:2023标准,形成包含五个阶段的作业流程:(1)基于FEA的预判分析建立试验边界条件;(2)定制化工装夹具实现试件6自由度约束;(3)分级加载系统执行准静态至冲击载荷谱;(4)分布式传感器网络采集3200点/秒动态数据;(5)大数据平台生成S-N曲线与损伤容限图谱。在高铁转向架检测中,该流程成功识别出轮轴连接处2.8mm的微观裂纹,较常规检测提前12个运维周期发出预警。
## 行业应用实践
### h2 跨领域解决方案典范
在风电行业,金风科技采用多体动力学仿真与实物测试联动模式,其5MW机组叶片通过200万次循环加载试验,验证了玻璃钢复合材料的疲劳寿命指标。检测报告显示,在模拟台风工况(55m/s风速)下,关键连接部位应力集中系数控制在1.8以下,满足IEC 61400-23标准要求。汽车领域,吉利研究院的数字化检测平台已将整车碰撞试验成本降低40%,通过建立材料本构模型库,实现B柱抗弯强度预测精度达92.6%。
## 质量保障体系
### h2 智能化质控网络
项目构建了"设备-人员-数据"三维管控体系:(1)计量溯源系统确保MTS 370液压伺服系统等关键设备年校准合格率100%;(2)基于机器视觉的试件装夹定位系统将人为误差降低至0.05mm;(3)区块链技术实现检测数据全程上链存证。上海电气检测中心的应用案例表明,该体系使检测报告出具效率提升60%,数据追溯响应时间缩短至15分钟以内。
## 发展展望
随着数字孪生技术的深化应用,建议行业重点推进三方面建设:一是建立全域载荷谱数据库,实现典型工况数据共享;二是研发基于AI的失效模式自诊断系统,提升异常检测灵敏度;三是制定智能化检测装备的行业标准体系。预计到2026年,融合5G传输与边缘计算的在线检测系统将覆盖80%以上重点工程,推动机械强度试验进入实时化、无人化新阶段。
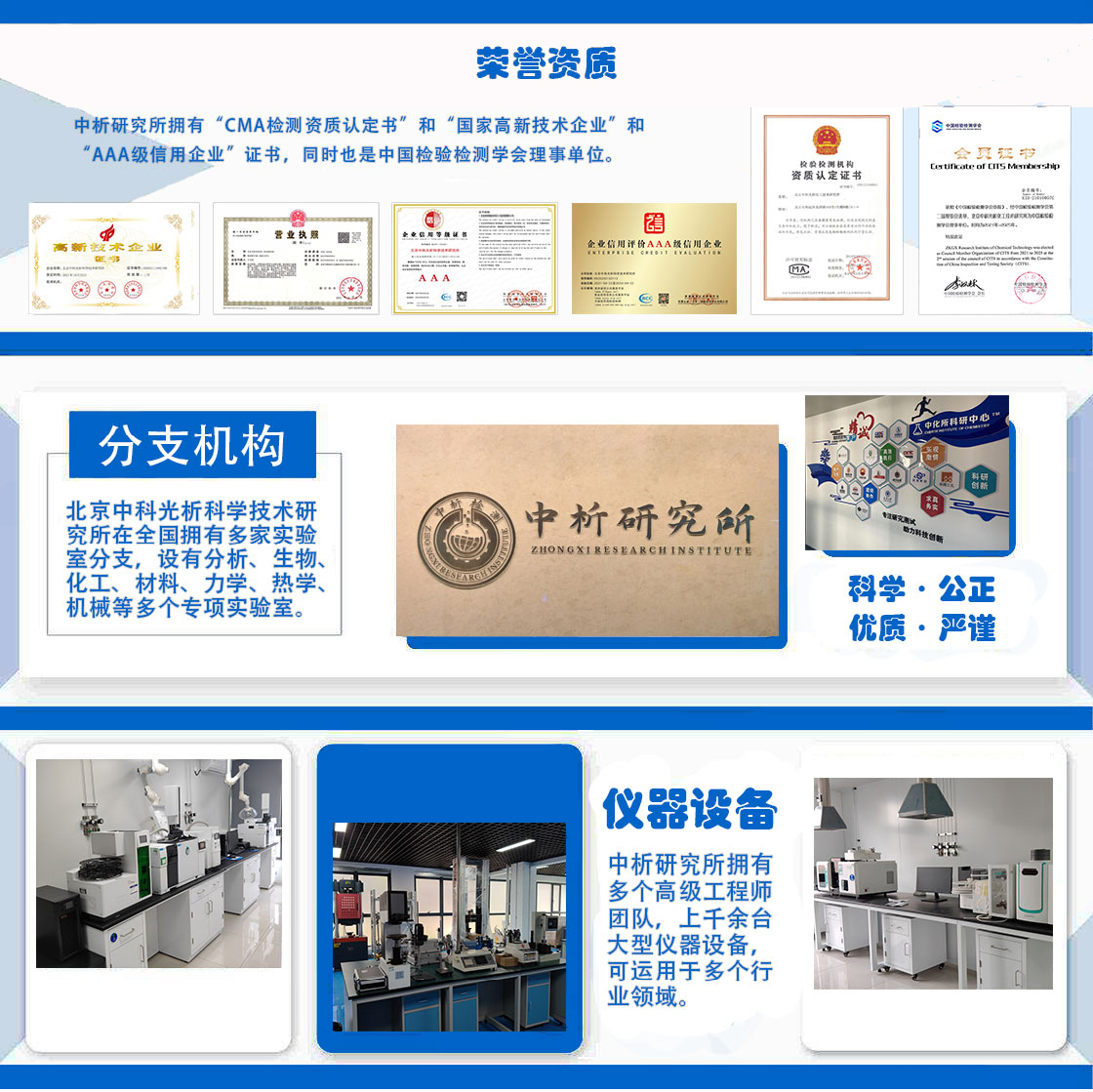
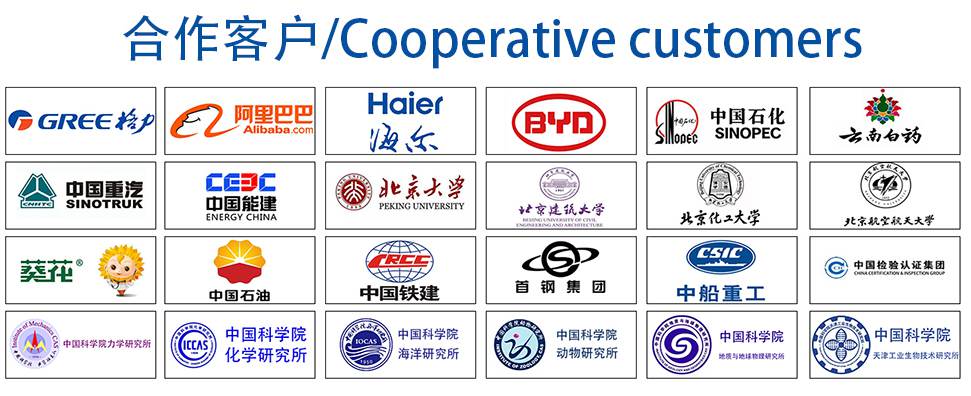
材料实验室
热门检测
4
12
14
13
15
15
14
18
21
19
17
18
14
15
15
12
13
15
23
21
推荐检测
联系电话
400-635-0567