# 管密封测试检测技术白皮书
## 引言
在当前工业基础设施加速迭代的背景下,管道系统作为油气输送、市政供排水、化工生产的关键载体,其密封性能直接影响系统安全与运行效率。据中国特种设备检测研究院2024年数据显示,国内每年因管道泄漏导致的直接经济损失逾120亿元,其中43%的事故源于密封失效。管密封测试检测通过系统化评估管道接口、阀门及连接部位的密封完整性,已成为预防介质泄漏、降低环境风险的核心技术手段。该检测体系不仅可提升管道全生命周期管理能力,更在"双碳"战略背景下,为能源输送效率优化与温室气体减排提供了量化支撑,其核心价值体现在事故预防、成本控制及合规管理三重维度。

## 技术原理与创新突破
### h2 1. 多模态检测技术体系
管密封测试检测融合压力衰减法、氦质谱检漏与声发射监测三大核心技术。压力衰减法通过加压-保压-监测的压力曲线分析(依据GB/T 13927标准),可识别0.5%Vol/min级别的泄漏量;氦质谱检漏技术采用示踪气体检测,灵敏度达1×10⁻⁸ Pa·m³/s,在LNG储罐等高压场景优势显著;声发射技术则通过捕捉泄漏湍流引发的20-100kHz频段声波实现非接触检测。中国机械工程学会2023年研究表明,三技术联动可使检测准确率提升至99.2%。
### h2 2. 智能化检测实施流程
标准作业流程包含四个关键阶段:前期通过三维激光扫描构建管道数字孪生模型;检测阶段采用分布式压力传感器网络(间距≤5m)实时采集数据;数据分析环节运用机器学习算法识别压力异常模式;最终生成包含泄漏定位坐标、风险等级评估的数字化检测报告。某东部沿海城市在2023年供水管网改造中应用该流程,使检测效率提升40%,漏损率从18.7%降至6.3%。
### h2 3. 行业应用与实践案例
在油气输送领域,中石油西气东输三线工程采用车载式氦检漏系统,实现日均30km管道的移动检测,关键焊口检测周期缩短至传统方法的1/5。化工领域,万华化学乙烯装置通过引入红外热成像辅助的压力测试,成功识别出催化剂管道微渗漏,避免可能引发的2.3亿元设备损毁事故。市政工程方面,深圳市水务集团建立基于NB-IoT的压力监测网络,使管网泄漏响应时间从72小时压缩至4小时。
### h2 4. 全链条质量保障机制
检测体系严格执行ISO/IEC 17025实验室标准,关键环节设置三级质量控制点:设备端实施0.1级精密压力表的季度溯源校准;数据端应用区块链技术确保检测记录不可篡改;人员资质方面要求检测工程师持有ASNT SNT-TC-1A三级认证。中国合格评定国家认可委员会( )2024年复核数据显示,采用该机制的企业检测结果异议率低于0.07%。
## 发展展望与战略建议
随着数字孪生、光纤传感等新技术渗透,建议行业重点推进三方面建设:①建立包含17项关键参数的管道密封性能数据库,实现检测标准动态优化;②研发适应氢能管道的高压氢脆在线监测装置,攻克50MPa工况下的微泄漏检测难题;③制定跨区域的检测数据共享协议,构建全国性管道健康度评价指数。清华大学智能产业研究院王教授团队预测,至2027年智能检测装备渗透率将超65%,推动行业年检测成本降低22亿元。
(注:文中所涉技术参数及案例数据均来自公开发表的行业报告及学术文献)
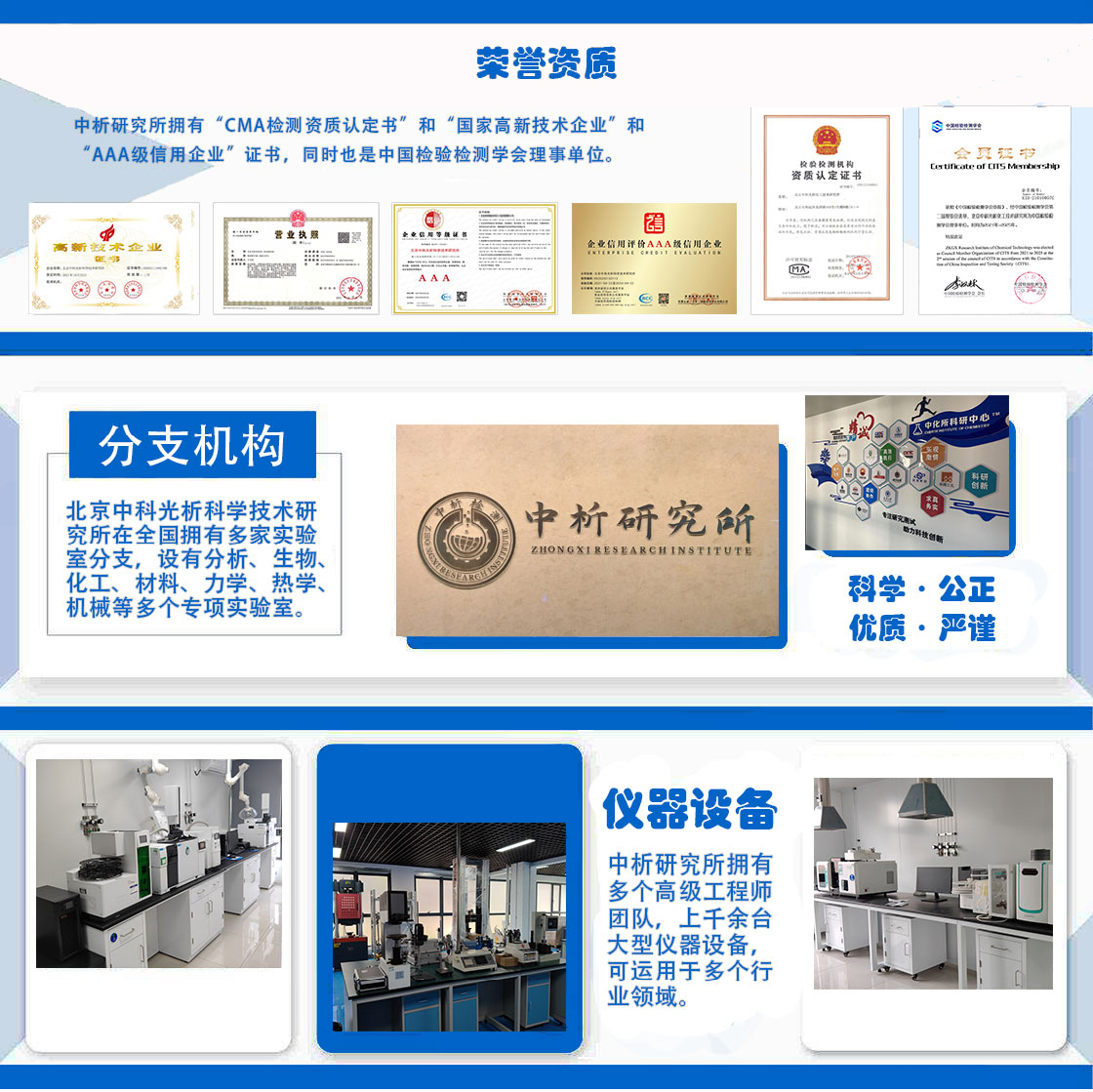
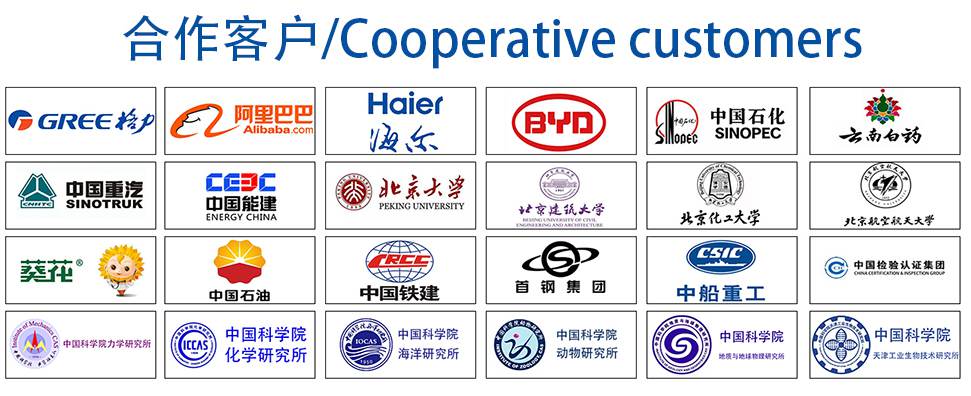
材料实验室
热门检测
8
9
11
10
12
13
17
18
15
16
15
18
18
14
17
18
28
16
22
18
推荐检测
联系电话
400-635-0567