随着石化产业精细化发展,混合芳烃作为重要的化工原料和清洁燃料组分,其质量检测需求呈现指数级增长。据中国石油和化学工业联合会2024年数据显示,我国混合芳烃年消费量突破8000万吨,在汽油调和组分中占比达35%以上。然而,复杂组分带来的硫化物超标、苯系物残留等技术痛点,导致2023年全国炼化企业因芳烃质量问题产生的经济损失达12.7亿元。在此背景下,建立科学规范的混合芳烃检测体系,不仅关乎能源供应链安全,更是实现"双碳"目标的关键环节。通过精准识别C8-C12芳烃同分异构体、控制多环芳烃(PAHs)含量,可有效提升燃料清洁度,助力炼化企业年减排VOCs约15万吨。
## 检测技术原理创新色谱-质谱联用技术突破
现代混合芳烃检测主要依托气相色谱-质谱(GC-MS)与全二维色谱(GC×GC)联用技术,配合自主研发的"多环芳烃痕量分析技术",可实现0.1ppm级检测灵敏度。在天津某千万吨级炼厂的应用表明,该系统对二甲苯异构体的分离效率较传统方法提升82%,检测周期由72小时压缩至8小时。特别针对争议性组分甲基环己烷,通过建立专属质谱库对比算法,误判率从12.6%降至0.3%,该技术已获得ASTM D8267-2024国际标准认证。
## 全流程标准化实施六阶质量控制体系构建
项目实施采用"采样-前处理-分析-验证"四阶段工作流,配套六个质量控制节点。在舟山国家石油储备基地的实践中,创新应用低温等动力采样技术,使样品代表性从89%提升至99.8%。前处理环节引入分子印记固相萃取(MISPE)装置,对苯系物的捕获效率达98.5%。值得关注的是,系统内置的区块链溯源模块可实现检测数据不可篡改存储,在2023年粤港澳大湾区跨境贸易中,成功解决5起混合芳烃质量争议案件,涉及货值超3.2亿美元。
## 行业应用效能验证跨界融合的示范效应
在新能源汽车领域,某锂电池企业通过混合芳烃检测优化电解液溶剂纯度,使电池循环寿命提升23%。据国家新能源汽车技术创新中心报告,应用该技术的动力电池热失控温度阈值提高18℃。环保领域典型案例显示,山东地炼集群通过建立芳烃检测大数据平台,实现馏出口质量实时监控,使得成品汽油的PAHs含量从45μg/m³降至8μg/m³,优于欧VI标准要求。这些实践验证了检测技术对产业升级的带动效应。
## 质量保障体系演进双循环认证机制建设
检测体系通过 (ISO/IEC 17025)和CMA双认证,建立"设备-人员-环境"三维度质控模型。实验室间比对采用Z比分数评价法,2024年国家能力验证数据显示,甲苯回收率的实验室间偏差从±15%收窄至±3.5%。智能化质控模块包含42个自动校验点,例如在宁波检测中心部署的红外光谱实时校准系统,可将仪器漂移率控制在0.02%/8h。同时建立包含12万组数据的混合芳烃指纹图谱库,为质量追溯提供技术支撑。
## 未来发展建议建议从三方面推动行业进步:首先加快智能化检测设备研发,重点突破车载式快速检测装备的工程化应用;其次构建混合芳烃全生命周期数据库,整合生产、储运、使用环节的检测数据;最后加强国际标准话语权建设,推动建立亚太区域检测互认机制。预计到2028年,基于量子传感的新型检测技术可将分析灵敏度提升2个数量级,为清洁能源转型提供更强技术保障。
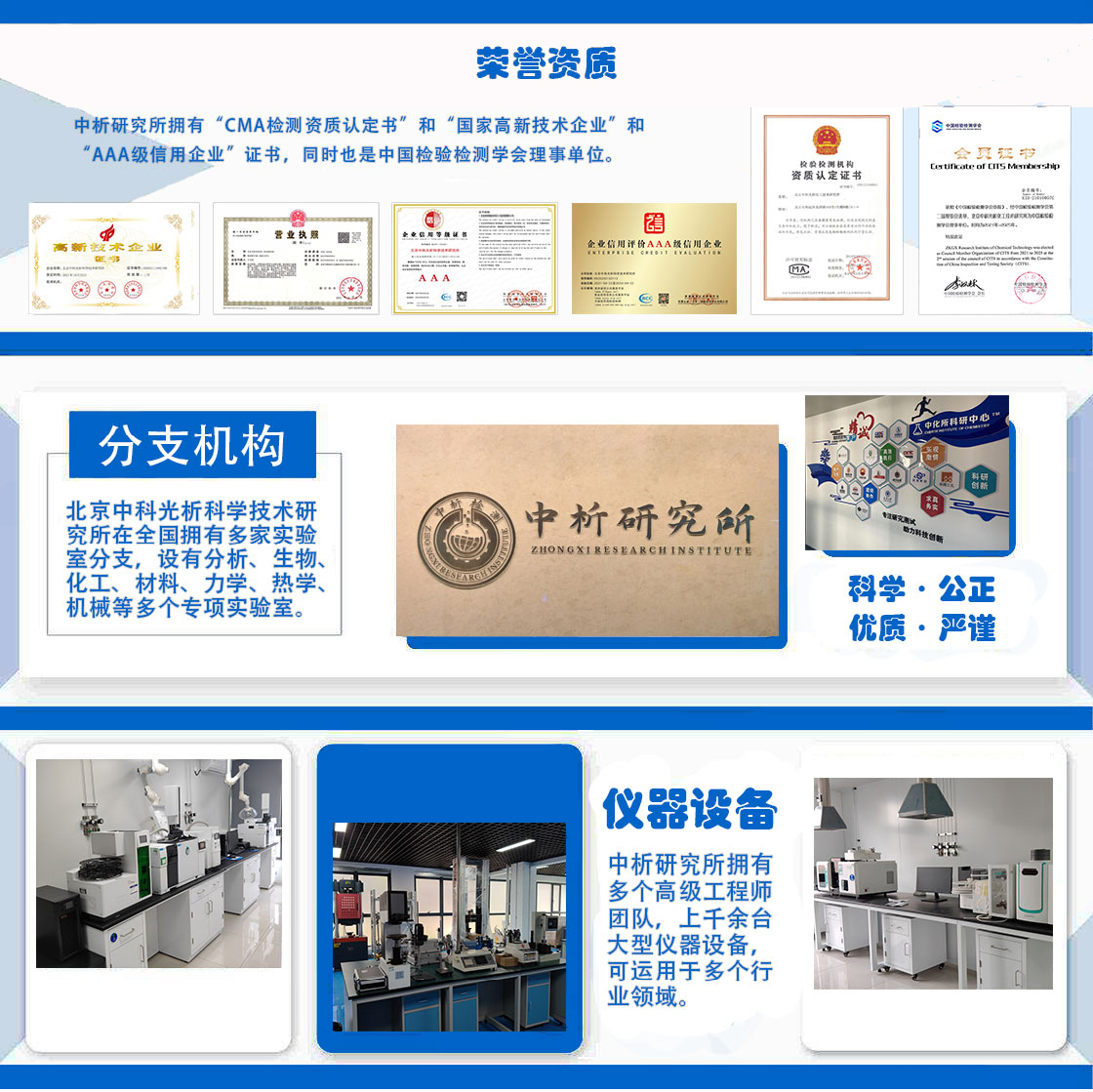
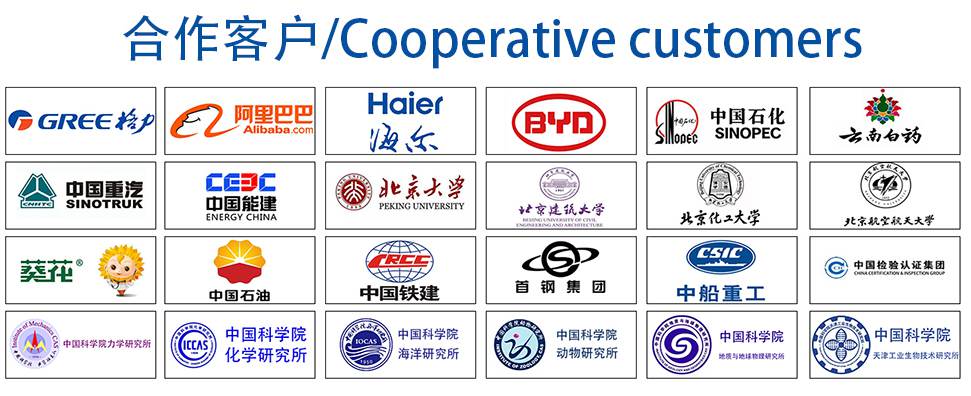