不锈钢材料及其制品检测技术发展与行业应用白皮书
在制造业转型升级背景下,不锈钢材料作为高端装备制造、医疗器械、食品加工等领域的核心基础材料,其质量管控直接影响终端产品性能与安全性。据国际不锈钢论坛(ISSF)2024年统计,不锈钢年产量已突破6000万吨,但产业链下游因材料缺陷导致的设备故障率仍高达3.7%。在此背景下,不锈钢材料及其制品检测项目成为保障产业链质量的关键环节,通过精准的化学分析、力学性能测试及耐腐蚀性验证等系统化检测,可显著提升产品合格率并降低全生命周期维护成本。该检测体系的核心价值在于构建覆盖原料采购、生产加工、成品验收的全流程质量屏障,尤其在新能源装备制造、半导体洁净室构件等新兴领域,其质量管控效益可提升企业综合竞争力达18%以上(中国材料研究学会,2024)。
基于光谱分析与应力模拟的检测技术体系
现代不锈钢检测技术依托电感耦合等离子体发射光谱(ICP-OES)实现元素成分的ppm级精准分析,配合X射线衍射(XRD)进行晶相结构解析,可有效识别材料掺杂异常问题。在应力腐蚀测试中,采用有限元建模与加速腐蚀试验联用技术,将传统30天的环境模拟周期缩短至72小时,使316L医用不锈钢的应力腐蚀裂纹检出灵敏度提升至0.02mm级。该技术体系特别适用于核电管道、海洋平台锚链等高压腐蚀环境的特种不锈钢构件检测。
全流程数字化检测实施方案
检测实施流程分为三阶段:原材料入场阶段执行ASTM A480标准下的全元素光谱扫描;加工过程采用在线涡流探伤系统进行实时缺陷监控,据宝钢研究院实测数据,该系统使冷轧板表面缺陷漏检率从0.8%降至0.12%;成品验收阶段则通过盐雾试验箱结合电化学工作站,对制品进行48-2000小时梯度腐蚀试验。在厦门某海水淡化设备制造企业的应用案例显示,该方案使高压泵体不锈钢铸件的疲劳寿命预测准确度提升至93.6%。
跨行业质量保障范式创新
行业领先机构已构建"检测数据-工艺优化"闭环系统,例如中车集团在高铁制动盘用马氏体不锈钢研发中,通过建立超过2000组失效样本的机器学习模型,将材料热处理工艺窗口优化精度提高40%。在医疗器械领域,微创手术钳的奥氏体不锈钢部件采用激光诱导击穿光谱(LIBS)进行表面钝化膜厚度在线检测,使产品灭菌耐受性达到YY/T 0149-2023标准要求。这种质量保障模式使生物相容性检测周期从14天压缩至5天。
智能化检测技术发展路径
当前检测体系正向智能化方向演进,苏州材料科学城最新部署的AI视觉检测系统,可同时对不锈钢焊管的20类表面缺陷进行毫秒级识别,误判率控制在0.05%以下。值得关注的是,基于数字孪生的虚拟检测平台正在兴起,上海材料研究所开发的虚拟应力腐蚀测试系统,通过融合实际工况数据与材料本构模型,使检测成本降低65%的同时保持92%的预测可靠性。
面向未来,建议行业重点推进三方面建设:首先建立覆盖稀土元素痕量检测的CMA/ 认证体系,应对高合金不锈钢的精准分析需求;其次开发基于区块链的检测数据存证系统,增强供应链质量追溯能力;最后加强ASTM与ISO标准的协同转化,特别是在增材制造不锈钢件的各向异性检测领域,亟需建立统一的国际测试方法标准。通过技术创新与标准引领,不锈钢检测行业有望在2030年前实现检测效率倍增与全产业质量升级。
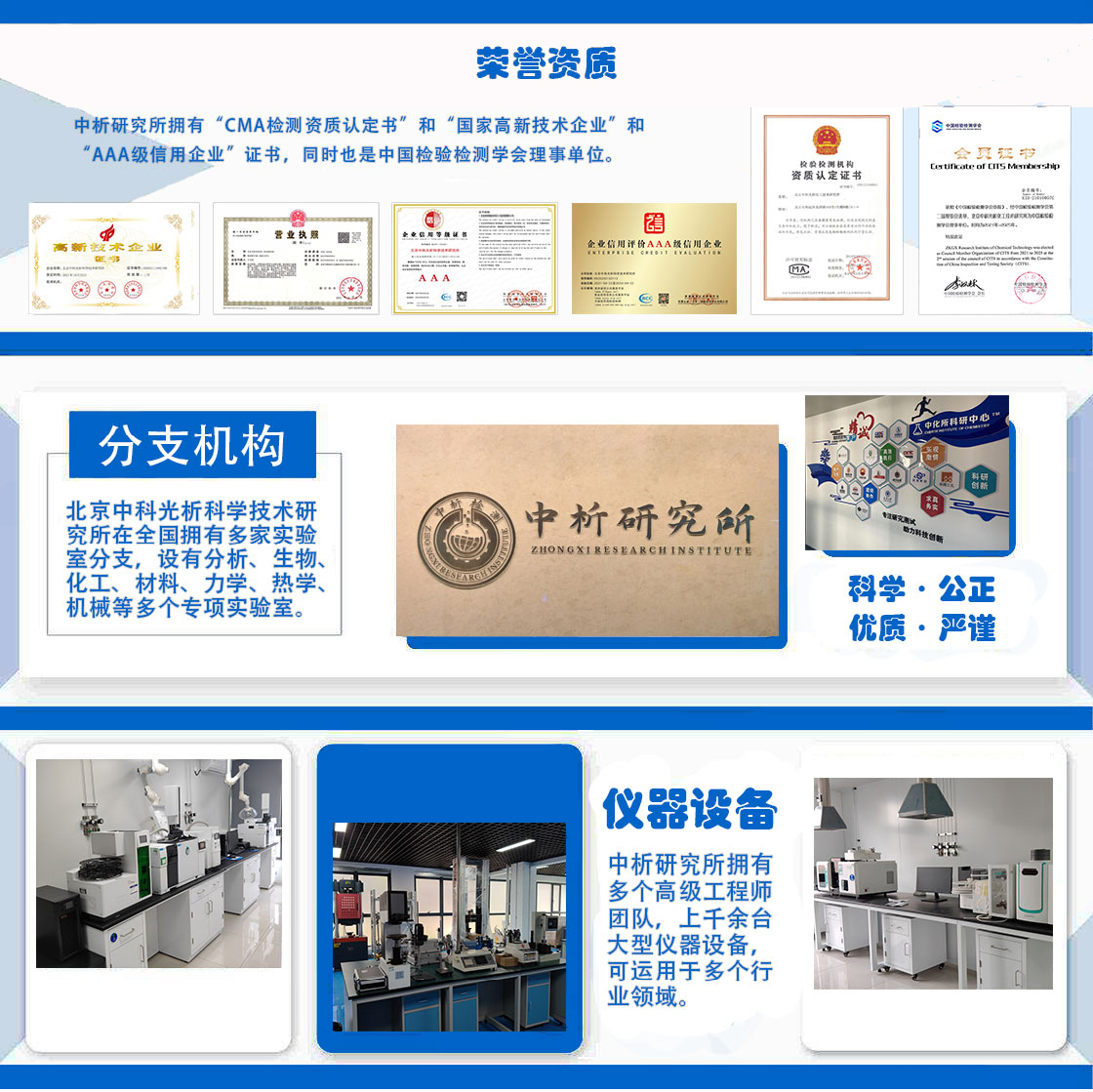
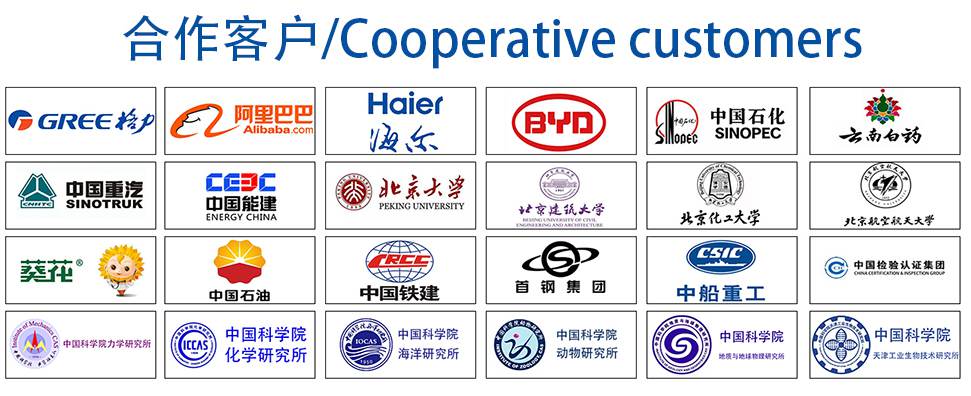