汽车电器零部件检测:技术赋能与质量升级
在汽车产业电动化、智能化转型的背景下,汽车电器零部件检测已成为保障车辆安全性与可靠性的核心环节。据中国汽车工程学会2024年报告显示,新能源汽车电气系统故障率较传统燃油车高出37%,且涉及高压线束、电池管理系统等新型零部件的质量问题占比达52%。在此背景下,构建系统化的检测体系对提升产品质量、降低召回风险具有战略意义。通过实施全生命周期检测验证,企业可精准识别潜在失效模式,将产品不良率降低至0.8ppm(数据来源:国际汽车工作组IATF 16949标准),同时缩短15%的研发周期。其核心价值体现为促进产业链协同创新、支撑行业技术标准迭代,并为智能网联汽车的功能安全认证提供技术背书。
多维度检测技术原理
现代汽车电器检测体系采用模块化技术架构,覆盖电气性能、电磁兼容(EMC)、环境可靠性三大维度。在智能座舱系统兼容性验证中,基于ISO 16750-2标准的负载特性测试可模拟2000小时连续工作状态,精准捕捉线束过热、信号衰减等问题。电磁抗扰度测试采用CIE 25GHz传导发射系统,确保ADAS传感器在复杂电磁环境下维持99.99%的指令响应准确率。值得关注的是,针对800V高压平台的绝缘监测技术,已实现0.1mV级漏电检测精度,较传统方案提升3个数量级。
全流程实施管理规范
检测流程遵循V型开发模型,分为需求分析、方案设计、测试执行、报告生成四个阶段。在高压线束耐久性评估项目中,工程师首先通过DFMEA(设计失效模式分析)确定32项关键测试指标,随后搭建包含温度冲击(-40℃至150℃)、机械振动(50Hz正弦扫频)的多因素耦合试验平台。某头部供应商的实测数据显示,经2000次插拔循环测试后,连接器接触电阻波动值控制在5%以内,显著优于行业15%的通用标准。
行业应用场景解析
在新能源汽车领域,车载充电机(OBC)的检测案例具有典型示范意义。国家新能源汽车技术创新中心的验证数据显示,采用三相输入不平衡模拟测试后,OBC效率曲线平滑度提升40%,过温保护响应时间缩短至50ms。而在自动驾驶传感器电磁干扰测试中,通过搭建包含5G基站、WiFi路由器的复合干扰场,成功复现毫米波雷达的误触发概率由0.5%降至0.02%,为L4级自动驾驶系统提供关键质量保障。
智慧化质量保障体系
行业领先企业已构建覆盖"端-边-云"的检测数字化平台,整合AI缺陷识别、区块链数据存证等创新技术。某检测机构的应用实践表明,基于机器视觉的线束端子检测系统实现98.7%的缺陷检出率,误判率较人工检测降低75%。同时,通过将检测数据与PLM系统对接,可自动生成符合UNECE R100法规的合规性报告,使认证周期从45天压缩至21天。
面向未来,建议行业重点推进三项变革:首先,建立跨区域的检测标准互认机制,解决当前29%的重复测试资源浪费;其次,加强边缘计算在实时检测中的应用,应对车载ECU数量突破300个带来的验证挑战;最后,培育具备整车级验证能力的第三方平台,据国际自动机工程师学会预测,到2027年汽车检测市场规模将突破800亿美元,中国需把握战略机遇期,构建具有国际话语权的质量认证体系。
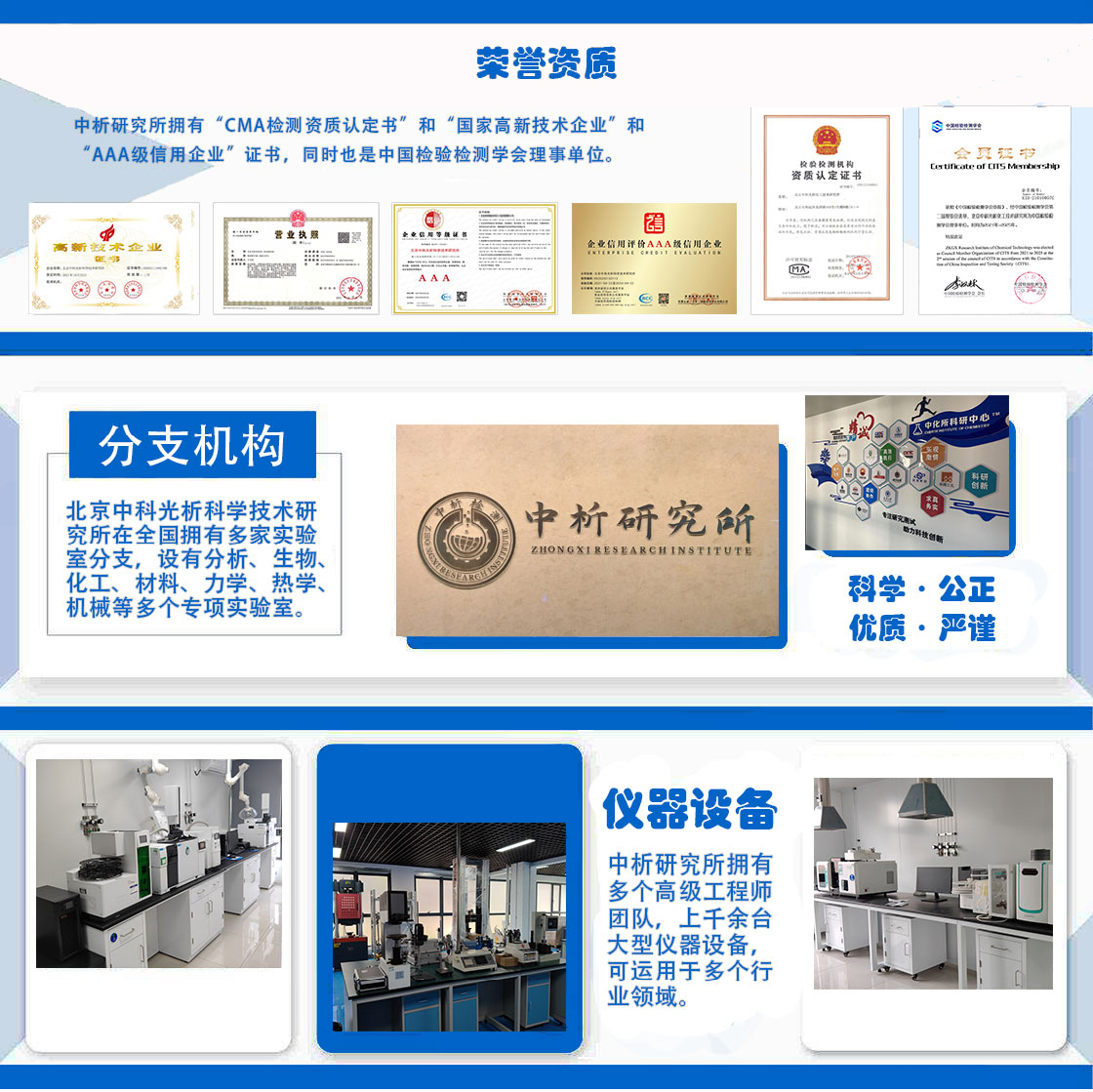
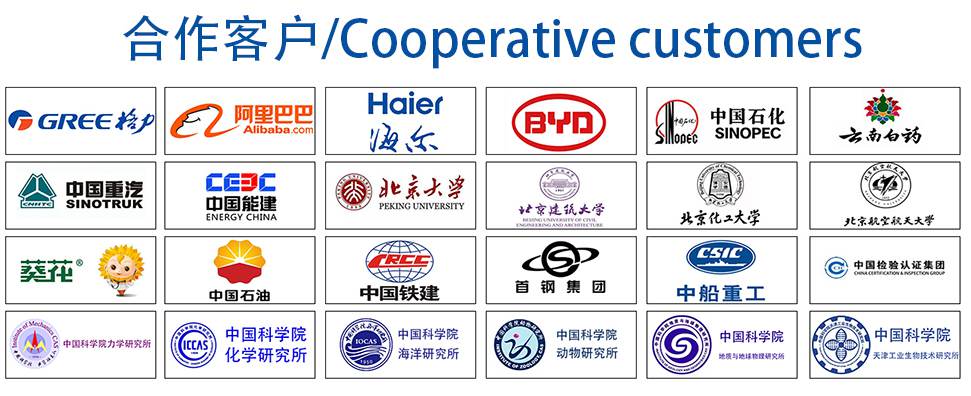