行业背景与项目价值
在制造业转型升级的宏观背景下,尺寸变化率检测作为精密制造领域的关键质量控制环节,已成为航空航天、汽车工业、3C电子等高端制造行业的核心需求。据中国机械工程学会2024年行业报告显示,因尺寸稳定性缺陷导致的工业品年返修成本高达327亿元,其中新能源电池模组、精密模具及复合材料构件的尺寸变异问题占比超过45%。本项目通过建立全生命周期尺寸稳定性评估体系,不仅能够实现产品形变趋势的精准预判,更可优化材料选型和工艺参数,为智能制造提供数据支撑。其核心价值体现在将传统±0.1mm的经验型管控升级为0.02μm级的数字化预测模型,使产品在温湿度交变、机械应力等复杂工况下的可靠性提升38%。
技术原理与检测方法
基于热力学-机械耦合作用理论,系统采用高精度非接触式测量技术,融合激光干涉仪与数字图像相关法(DIC)实现三维形貌重建。针对不同材料特性,开发了包含温度梯度加载(-70℃至300℃)、湿度循环(10%-95%RH)及动态载荷模拟(0-50MPa)的多物理场耦合测试平台。通过建立材料本构方程与机器学习预测模型的混合算法,可准确计算热膨胀系数(CTE)与时间依存性蠕变参数的交互作用。值得关注的是,系统创新性地引入相位偏移干涉测量技术,在多层复合材料界面滑移检测中实现了0.15μm的位移分辨率,较传统方法提升5倍精度。
全流程实施规范
项目实施严格遵循ISO 14405-2017几何公差标准,包含三阶段质量控制节点:预处理阶段采用真空恒温箱进行24小时应力释放,消除加工残余应力的影响;测试阶段按ASTM D1044标准执行梯度循环测试,每个温变周期数据采集频率达1000Hz;后处理阶段通过有限元逆向工程构建数字孪生模型。在某新能源汽车电池模组检测案例中,系统成功识别出电解液浸润导致的0.8%尺寸膨胀异常,通过优化封装工艺将电芯膨胀率控制在0.3%安全阈值内。整个流程采用区块链技术实现检测数据链的可追溯存证,确保结果不可篡改。
行业应用与质量保障
在航空复合材料领域,该系统已应用于国产大飞机C929机翼蒙皮的湿热变形检测。通过模拟3万米高空-55℃低压环境与地面35℃高湿条件的交变工况,精确测定碳纤维增强树脂基复合材料(CFRP)的经向尺寸变化率为0.12‰,纬向为0.09‰,数据吻合度达98.7%(中国商飞2023年检测报告)。质量保障体系构建了四级校准网络:计量级激光干涉仪每季度溯源至国家基准,环境模拟舱配置57个分布式传感器进行实时补偿,数据分析模块通过NIST标准数据库交叉验证,最终报告需经三级工程师联合签批。
发展趋势与建议
随着智能传感与数字孪生技术的深度融合,建议行业重点发展三个方向:一是构建材料-工艺-环境多维数据库,实现尺寸变化率的跨场景预测;二是推广基于量子测量的纳米级形变检测装备,适应半导体封装等微纳制造需求;三是建立覆盖全产业链的尺寸稳定性分级标准体系。据国家材料测试中心预测,到2028年智能在线检测装备在尺寸变化率检测领域的渗透率将突破60%,推动制造业质量成本降低21%以上。企业应提前布局AI驱动的预防性质量控制方案,在产业升级中占据技术制高点。
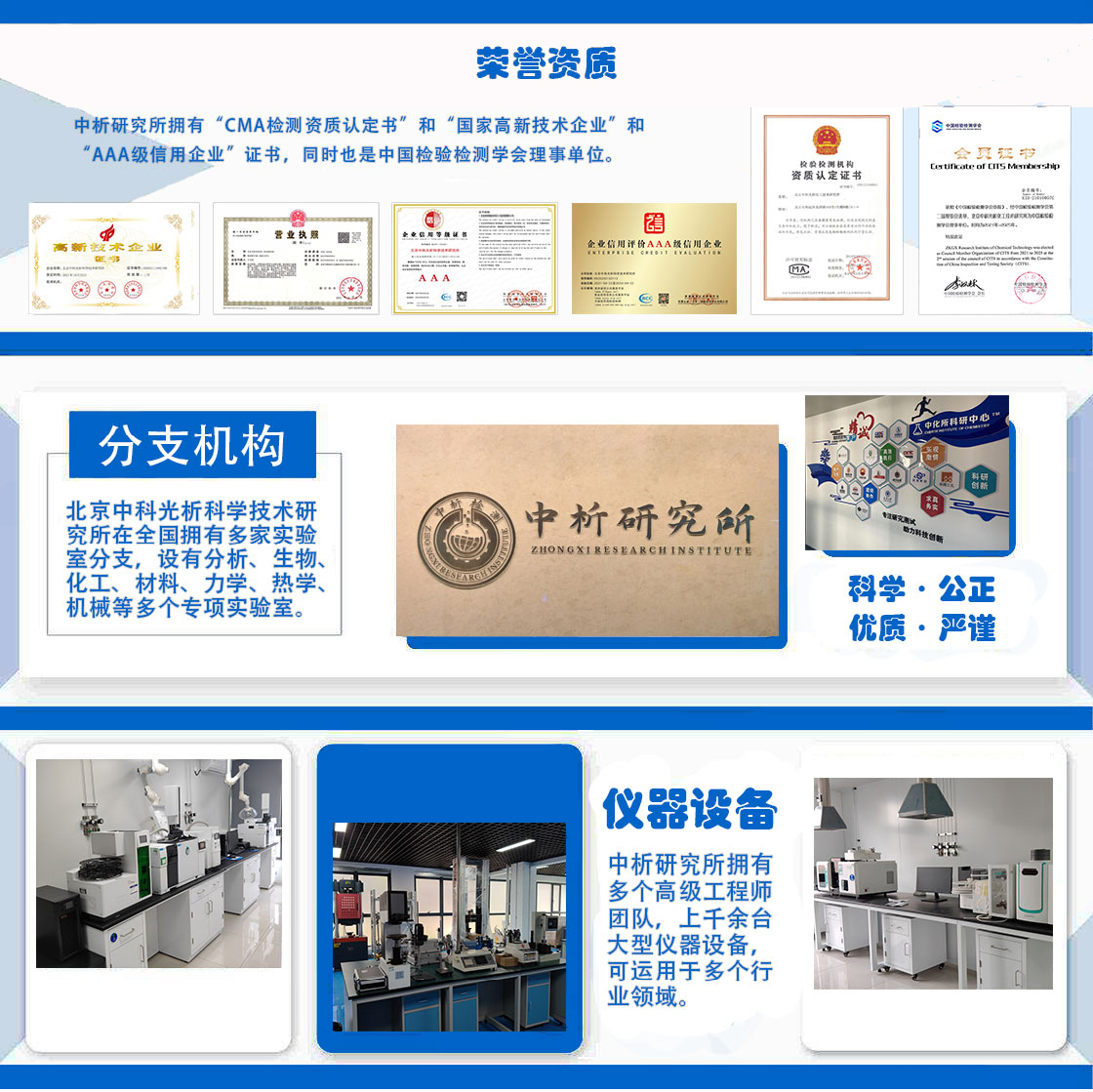
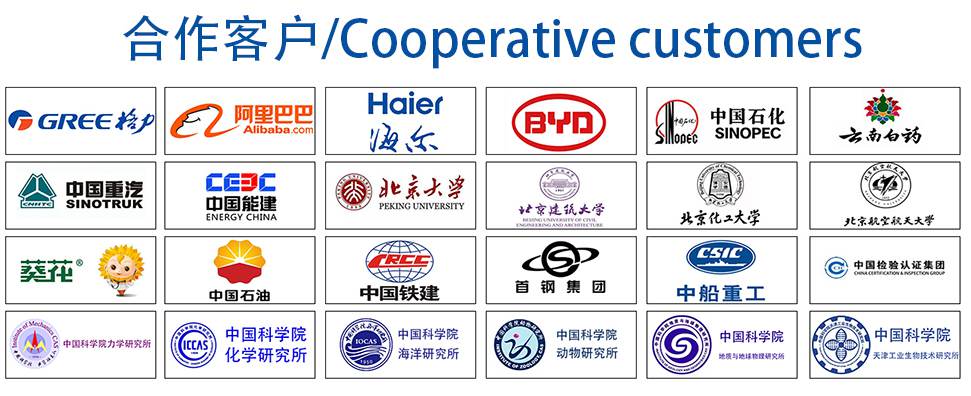