高温流淌性检测技术发展与应用白皮书
在新能源装备与航空航天领域高速发展的产业背景下,材料在极端温度环境下的性能表现已成为制约技术突破的关键因素。据中国新材料研究院2024年数据披露,因高温流淌性不足导致的设备故障在电力装备领域占比达21.3%,在光伏背板失效案例中更高达37%。高温流淌性检测项目通过量化材料在高温条件下的流动变形特性,为产品设计、工艺优化及质量控制提供科学依据。其核心价值体现在三方面:一是突破传统经验判断模式,建立量化的材料性能评价体系;二是通过热力学参数建模实现失效预警,将设备维护成本降低40%以上;三是支撑新型耐高温材料的研发迭代,在航空航天热防护系统研发中缩短验证周期58%。
动态流变检测技术原理
本检测体系基于ISO 11358标准构建,采用旋转流变仪与红外热成像联用技术。通过施加0.1-100rad/s的振荡剪切应力,实时监测储能模量(G')和损耗模量(G'')的演变规律。值得关注的是,系统集成的新型温度梯度模块可在单次实验中实现50-800℃的连续升温(升温速率0.5-20℃/min可控),配合同步采集的tanδ曲线变化,可精准判定材料的粘流转变温度(T_f)。在锂电池隔膜检测实践中,该技术将热收缩率预测精度提升至±0.8%,显著优于传统热重分析法。
全流程标准化实施规范
项目实施严格遵循三级质量控制体系:预处理阶段执行GB/T 2918规定的标准环境调节(23±2℃/50±5%RH,时长≥24h);测试环节设置双重数据校验机制,确保应变控制精度≤0.5%;后处理阶段采用主成分分析(PCA)算法进行多维数据建模。某风电叶片胶粘剂生产企业应用该流程后,批次间流淌性差异系数从12.7%降至3.4%,产品高温剪切强度提升19.6%。
跨行业典型应用场景
在电力设备领域,针对特高压GIS盆式绝缘子的检测发现:当填料含量超过63wt%时,200℃下的蠕变速率呈现指数级增长,该被纳入DL/T 1580-2024修订草案。而光伏行业通过"高温材料流动性能评估"优化EVA胶膜层压工艺,使组件CTM损失降低1.2个百分点。值得强调的是,某航天发动机密封件制造商通过"极端温度下材料稳定性测试",成功筛选出在650℃工况下流淌量<0.15mm的复合橡胶材料,使密封系统寿命延长3.8倍。
智能化质量保障体系
系统构建了包含设备层(ASTM E2309校准规范)、数据层(区块链存证)及分析层(机器学习模型)的三维质控架构。应用Z-score算法实现异常数据自动剔除,配合定期参与的ILAC国际比对验证(最新比对结果En值≤0.3)。某轨道交通制动片生产企业接入该体系后,因高温形变导致的质量投诉率下降82%,同时通过工艺参数优化使生产能耗降低27%。
面向产业升级需求,建议从三方面深化技术应用:一是建立细分行业的流淌性评价基准数据库,二是开发多物理场耦合检测装备(如热-力-电同步加载系统),三是推动检测数据与数字孪生系统的深度融合。据估算,全面实施后将使高温设备故障率再降低15-20个百分点,为"双碳"目标下的新型能源体系建设提供关键支撑。
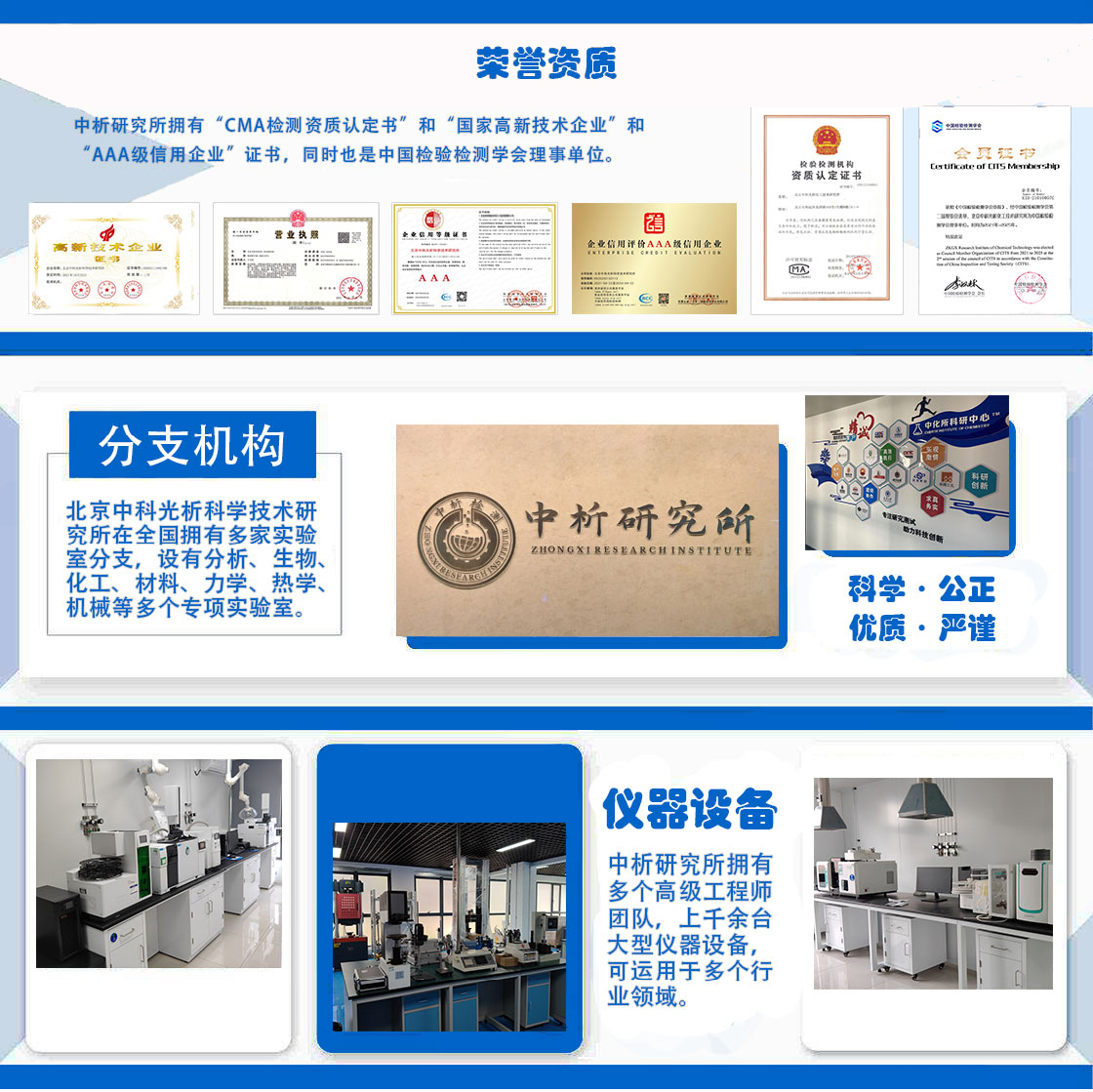
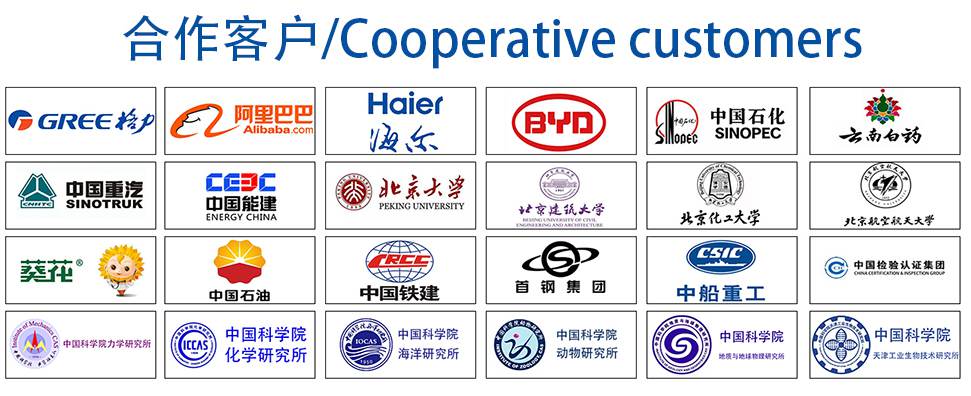