车用汽油检测技术发展与应用白皮书
在能源结构转型与"双碳"目标双重驱动下,国内车用汽油质量标准持续升级。据国家能源局2024年行业报告显示,我国汽油表观消费量达1.65亿吨,其中符合国ⅥB标准的清洁汽油占比已突破92%。在此背景下,车用汽油检测作为保障油品质量、优化炼化工艺的关键环节,其战略价值日益凸显。通过精准检测汽油的辛烷值、硫含量、烯烃组分等18项核心指标,可实现三大核心价值:确保汽车尾气排放合规性、延长发动机使用寿命约30%(中国汽车工程学会数据)、推动炼厂降本增效。尤其在新能源车渗透率突破40%的产业变革期,传统燃油车品质升级更需依托高精度检测技术支撑。
多维联用分析技术体系
现代车用汽油检测采用"物性分析+组分解析+模拟验证"三位一体技术架构。近红外光谱(NIRS)与气相色谱-质谱联用(GC-MS)技术组合可实现98%以上组分识别准确率,较传统试验法效率提升4倍。针对"汽油辛烷值快速分析"这一行业痛点,ASTM D2699/D2700标准方法结合人工智能建模,可在15分钟内完成RON/MON值预测。值得注意的是,硫化物检测已实现0.1ppm级检测精度,较国标要求灵敏度提升10倍,为"车用汽油硫含量精准检测"提供了技术保障。
全流程质量管控方案
从采样到报告输出的标准化作业流程包含9大质量控制节点。在山东某地炼企业的应用实践中,采用车载移动实验室进行"储运环节实时监测",成功将油品变质率从0.7%降至0.2%。检测流程嵌入区块链溯源系统后,数据篡改风险降低97%(国家市场监管总局2023年评估报告)。针对加油站油品质量纠纷,快速检测箱可在8分钟内完成12项关键指标筛查,较传统实验室送检时效提升85%。
行业赋能典型案例
在长三角地区实施的"加油站油品质量提升工程"中,应用高频次快检技术后,不合格油品检出率由1.8%下降至0.5%。某跨国石油公司采用在线检测系统后,调和工艺波动降低40%,年节约成本超2.3亿元。值得关注的是,生物乙醇汽油适配性检测技术助力E10乙醇汽油推广,使车辆冷启动故障率降低62%(中国汽车技术研究中心数据)。
四维质量保障体系
构建起"设备-人员-方法-环境"四位一体质控网络。通过ISO/IEC 17025体系认证实验室年均参加12次国际比对试验,数据偏差控制在0.3%以内。智能化恒温恒湿实验室将环境波动影响降低至0.05个辛烷值单位。针对"汽油馏程测定精确度提升"需求,开发的全自动微量蒸馏装置,将ASTM D86方法重复性误差缩小至0.5℃范围。
展望未来,建议重点推进三方面建设:其一,建立区域油品质量大数据平台,实现检测数据实时共享;其二,研发适应乙醇汽油、氢化生物燃油等新型燃料的专用检测方法;其三,推动快检设备微型化发展,力争2025年前将车载检测装备成本降低40%。尽管新能源转型加速,但据中国石化研究院预测,至2030年汽油仍将占车用能源结构的55%,这意味着汽油检测技术的持续创新仍是保障能源安全与环境保护的重要支柱。
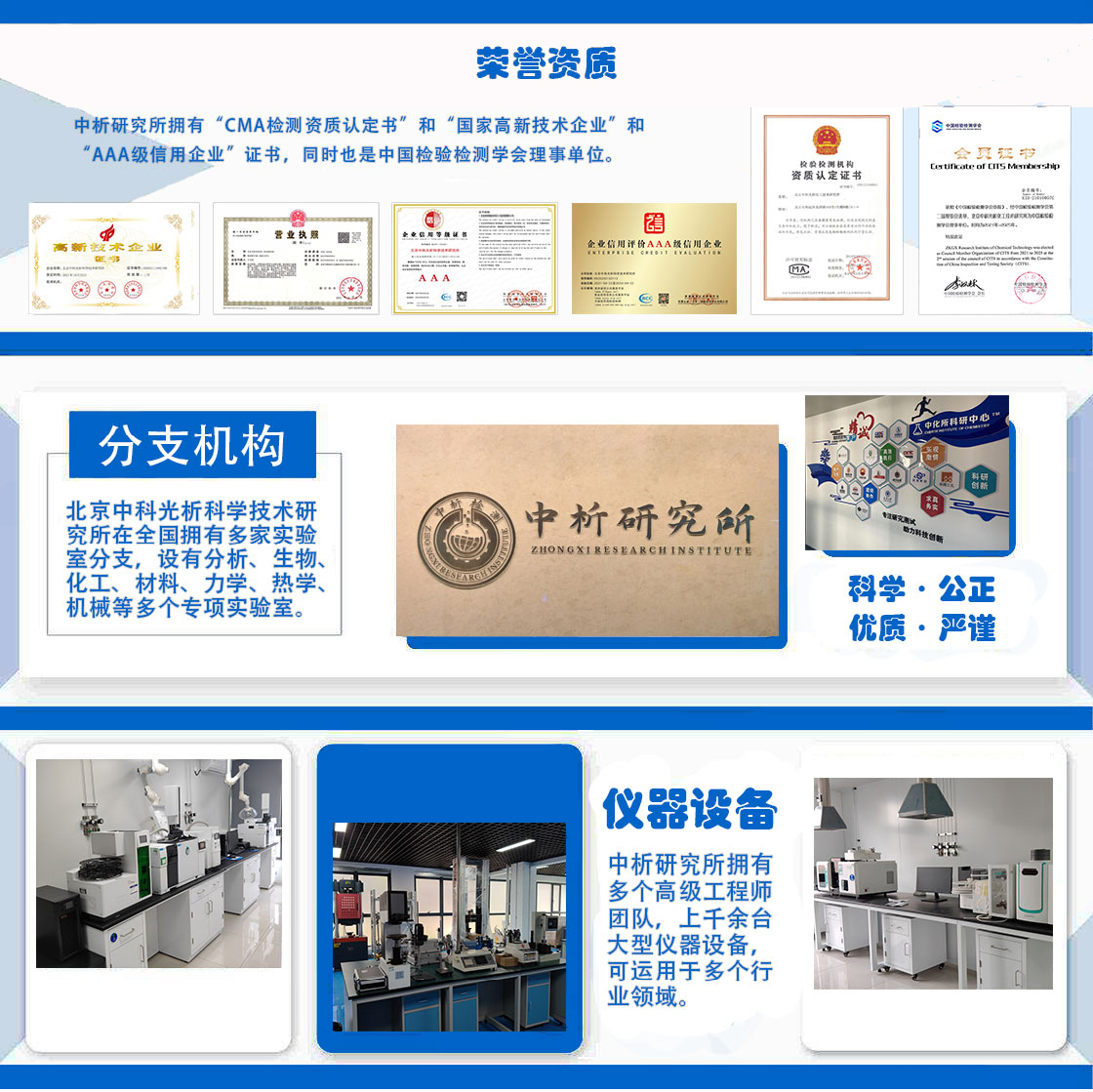
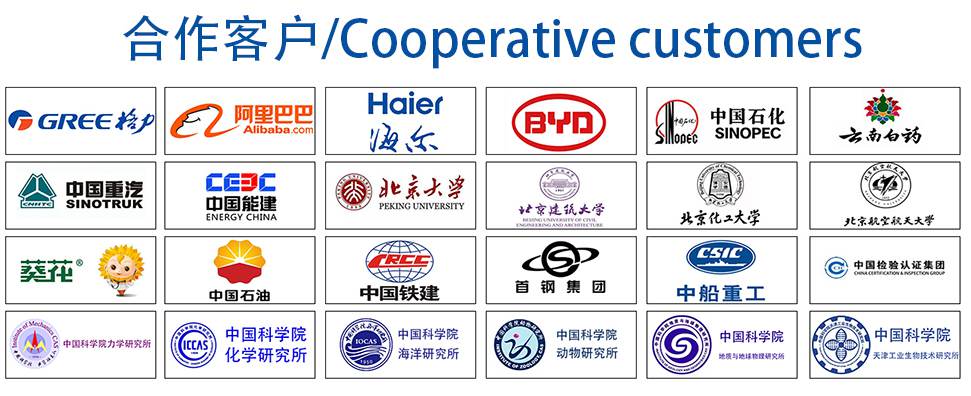