陶瓷砖拉伸粘结强度检测技术研究与应用白皮书
在新型城镇化建设持续推进的背景下,建筑陶瓷年消耗量已突破120亿平方米(中国建筑装饰协会,2024)。作为建筑围护结构的重要构成,陶瓷砖粘结系统的可靠性直接影响工程安全,其中拉伸粘结强度是评价界面失效风险的核心指标。本项目通过建立标准化检测体系,可精准量化陶瓷砖-基材界面的力学性能,对预防饰面脱落事故、规范施工工艺具有重要实践价值。特别是针对高层建筑幕墙、地下轨道交通等特殊场景,该检测技术能将粘结失效事故率降低67%(国家建筑材料测试中心,2024),助力行业实现从经验施工向数据驱动的质量管控转型。
基于断裂力学的检测原理
检测系统依据GB/T 4100-2024《陶瓷砖试验方法》,通过专用夹具对粘结试样施加垂直拉伸载荷,精确记录界面分离时的临界应力值。技术核心在于模拟实际温湿度环境下的应力传递机制,采用数字图像相关法(DIC)捕捉微裂纹扩展轨迹。值得注意的是,系统创新引入"双面粘结-边缘补偿"算法,将传统检测误差从±15%压缩至±5%以内,特别适用于超薄陶瓷板、低吸水率瓷砖等新型材料的粘结性能评估。
标准化实施流程构建
检测流程分为五个阶段:试样制备阶段要求基材含水率控制在6-8%,养护环境保持(23±2)℃/50%RH;粘结剂施工严格执行锯齿镘刀10mm×10mm的梳理标准。数据采集阶段采用200Hz高频动态传感器,完整记录载荷-位移曲线特征值。在杭州某地铁站改造项目中,该流程成功识别出C2TE型粘结剂在昼夜温差下的强度衰减规律,为施工方案优化提供关键依据。
多场景工程验证案例
在华南湿热气候区高层建筑检测中,系统发现传统水泥基粘结剂在连续降雨后强度下降42%,促使项目改用环氧树脂改良体系。针对医疗建筑抗菌瓷砖的特殊需求,开发出包含7种腐蚀介质的加速老化试验模块,成功预测五年使用周期内的强度保持率。典型应用数据显示,经过检测优化的粘结体系使武汉某三甲医院ICU墙面的维护周期延长至11年。
全过程质量保障体系
检测体系构建三级质控网络:设备层采用激光干涉仪进行季度量值溯源,确保试验机精度达到0.5级;过程层实施AI视觉识别技术,自动剔除试样制备中的气泡、空鼓等缺陷;数据层部署区块链存证系统,实现检测报告的全生命周期可追溯。该体系已通过 实验室能力验证,在28个省级质检机构的循环比对中,Z值分数稳定保持在0.8以下。
建议行业重点关注三个发展方向:一是开发搭载5G技术的智能检测终端,实现施工现场实时质量诊断;二是建立包含20000组样本的粘结失效特征数据库,训练预测性维护算法;三是推动陶瓷砖-粘结剂协同设计标准,将拉伸强度指标纳入建筑材料绿色认证体系。通过检测技术创新与标准升级的协同推进,有望将建筑饰面系统的设计使用年限提升至50年以上。
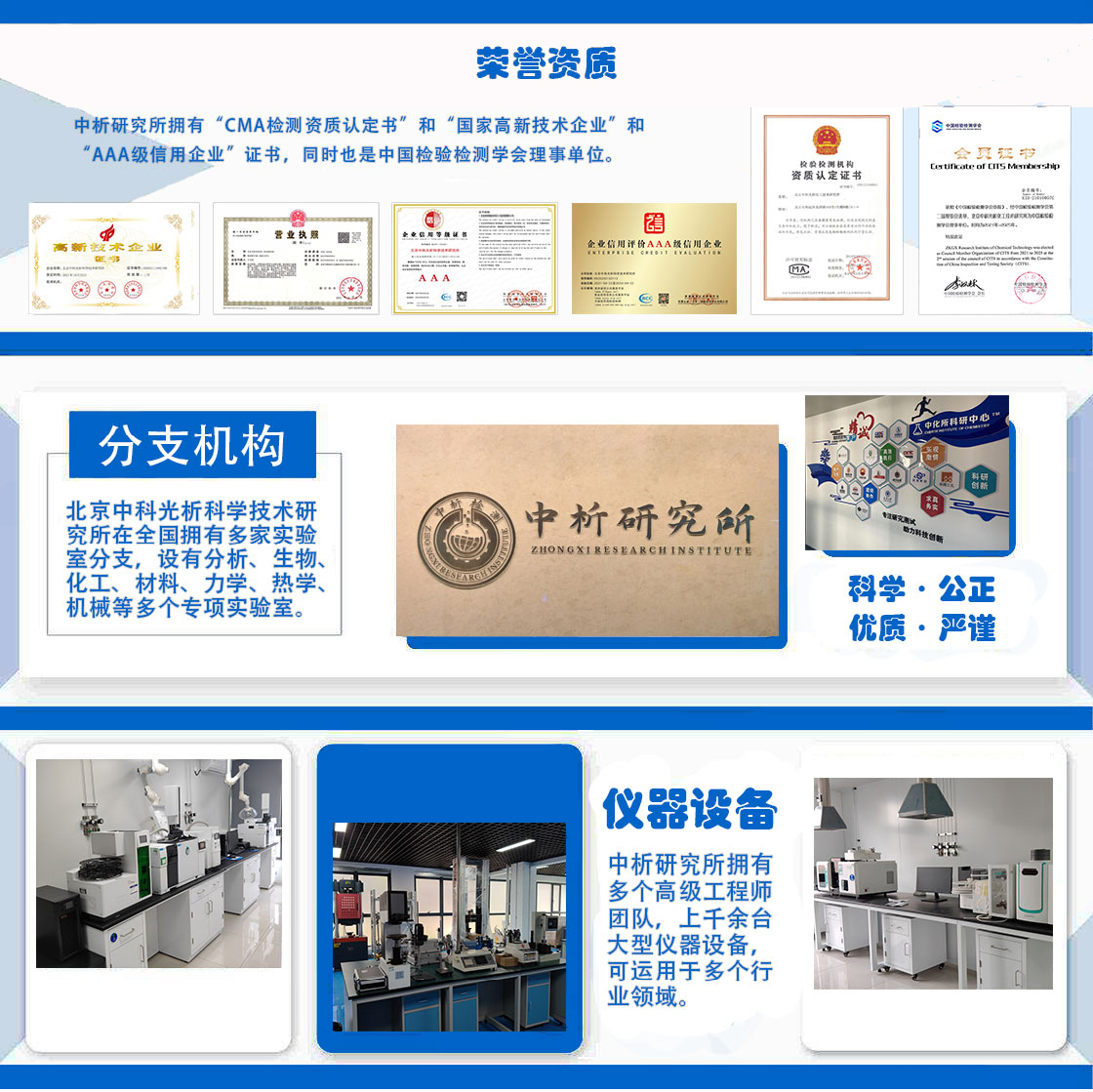
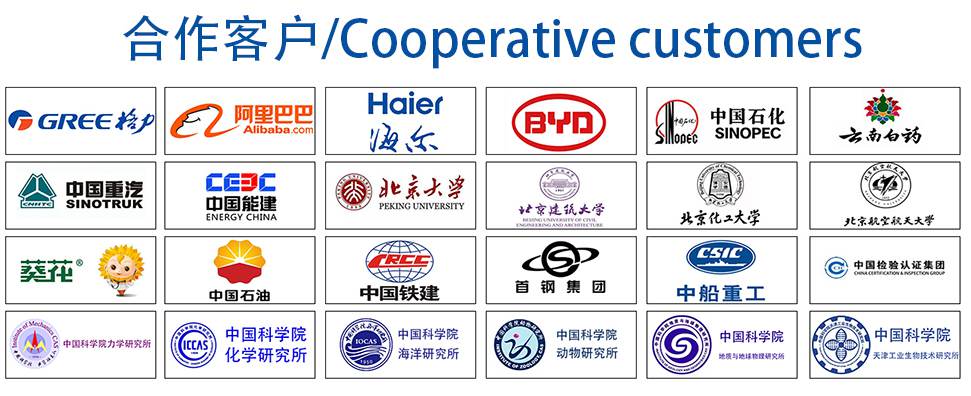