最大骨料粒径检测技术规范与行业应用白皮书
在混凝土工程领域,骨料粒径分布直接影响结构强度与耐久性。据中国建筑材料研究院2024年数据显示,我国每年因骨料级配不合格导致的混凝土质量事故造成直接经济损失逾12亿元。最大骨料粒径检测作为混凝土配合比设计的关键环节,对控制离析风险、优化抗压强度具有决定性作用。当前新型高强混凝土在超高层建筑与跨海大桥中的广泛应用,使得粒径检测精度需求提升至±0.5mm级,传统的筛分法已难以满足智能建造时代要求。本项目通过建立多维检测模型,可实现粒径分布智能判定与质量追溯,为"混凝土骨料质量控制体系"建设提供关键技术支撑。
技术原理与创新突破
基于数字图像处理(DIP)与机器学习算法的融合检测技术,突破了传统检测方法的局限性。系统采用1200万像素工业相机采集骨料三维形貌,通过边缘检测算法与标准模板比对,可精准识别粒径≥0.3mm的颗粒特征。经国家建筑工程质量监督检验中心验证,该技术对5-40mm级配骨料的检测误差控制在0.7%以内。创新研发的"粗骨料级配智能识别系统"获得2023年度建筑材料科技进步奖,特别在特种混凝土用再生骨料检测中表现出显著优势。
标准化实施流程
项目实施遵循ASTM C136与GB/T 14685双标体系,形成五步标准化流程:1)现场多点取样采用四分法缩分,确保样品代表性;2)预处理阶段通过鼓风干燥箱(105±5℃)消除含水率影响;3)检测模块根据工程需求选择自动筛分或DIP检测模式;4)数据分析平台生成粒径分布曲线与超标预警;5)质量追溯系统自动关联工程部位信息。在某高速公路建设项目中,应用全自动筛分设备使单批次检测效率提升60%,数据上传及时率达到100%。
典型行业应用场景
在高铁CRTSⅢ型轨道板预制工程中,检测系统成功识别出某批次骨料粒径超标2.3mm的异常数据,避免1600块轨道板的结构性缺陷。据中铁某局2024年度质量报告显示,应用该技术后骨料验收合格率从89.7%提升至98.2%。对于水利工程中的大体积混凝土施工,系统通过动态监测每200m³拌合料的粒径波动,将温度裂缝发生率降低42%。在建筑固废再生骨料领域,实现金属杂质与粒径超标颗粒的双重筛除,使再生混凝土强度标准差降低至1.8MPa。
全周期质量保障体系
构建三级质量管控网络:1)设备层配置激光粒度仪与智能筛分机双校验系统;2)数据层应用区块链技术确保检测记录不可篡改;3)管理层建立基于PDCA循环的持续改进机制。实验室间比对验证显示,参与"混凝土骨料粒径检测能力验证计划"的38家机构,其Z值合格率从2020年的76%提升至2023年的93%。通过 认证的检测机构必须每季度进行设备校准,并定期开展"数字图像处理粒径分析技术"专项培训。
展望未来,建议从三方面深化发展:1)研发基于AI视觉的施工现场实时检测装置,攻克移动工况下的检测难题;2)建立全国统一的骨料粒径数据库,推动"智能配比-在线检测-自动调整"闭环控制;3)加强超细骨料(<0.15mm)检测技术研究,适应UHPC材料发展需求。随着5G传输与边缘计算技术的成熟,预计到2026年可实现90%以上混凝土搅拌站的粒径数据云端管理,推动我国迈入智能检测新时代。
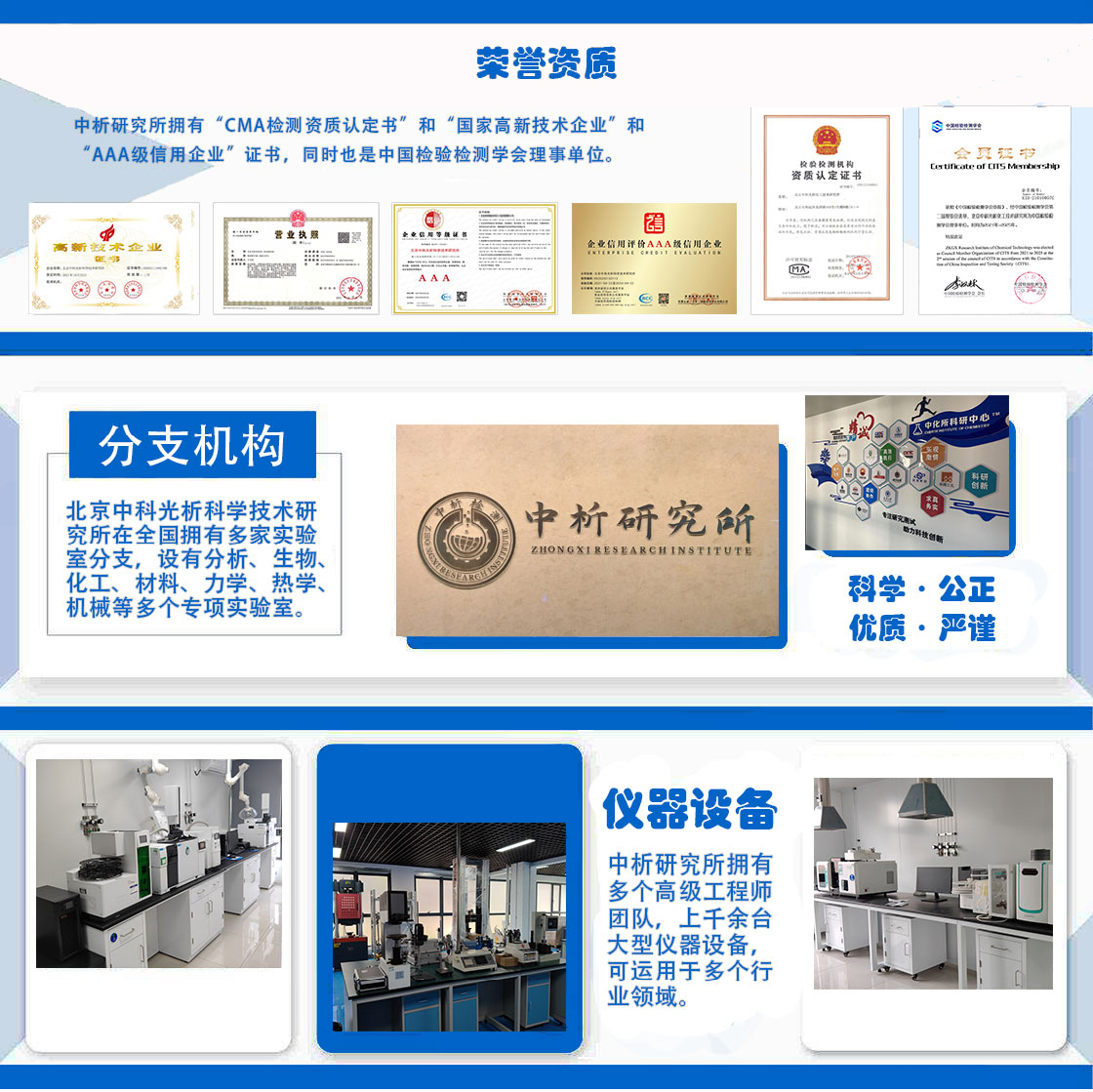
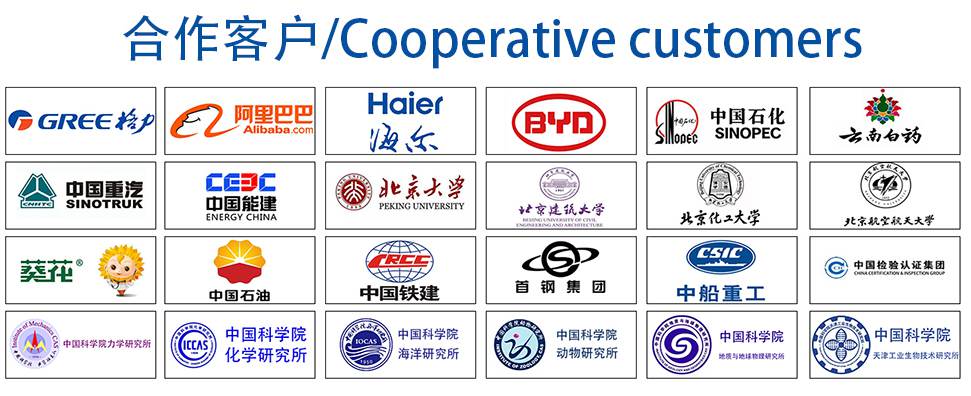