在高端装备制造与国防科技工业领域,金属、非金属材料及其复合构件的质量可靠性直接关乎装备性能与使用安全。据中国机械工程学会2024年发布的《齐全制造检测技术白皮书》显示,我国每年因材料缺陷导致的装备失效事故造成直接经济损失超120亿元,其中焊接缺陷和复合材料分层问题占比达47%。本项目构建的全要素检测体系,通过集成化检测方案覆盖从原材料到成品的全生命周期,在航空航天器结构完整性保障、电子组件可靠性验证、火工品安全评估等关键场景中,有效支撑了产品质量升级与国产化替代进程,其核心价值体现在缺陷检出率提升至99.3%(数据来源:国家材料测试中心认证报告),检测周期压缩40%以上。
多模态检测技术融合体系
检测系统采用X射线衍射、太赫兹时域光谱和激光超声三重复合技术,实现从表面到内部、宏观到微观的多维度分析。针对复合材料构件,通过太赫兹波在介质界面反射特性差异,可精准识别0.05mm级的分层缺陷;对于焊接件则运用相控阵超声技术,结合深度学习的信号处理算法,使气孔、裂纹等典型缺陷识别准确率提升至98.7%。在电子组件检测中,基于红外热成像的异常发热定位技术,配合三维CT扫描重构,可完成BGA焊点虚焊、桥接等隐蔽缺陷的可视化诊断。
全流程质量管控实施路径
检测服务实施分为四个标准化阶段:首先采用数字孪生技术构建被检件虚拟模型,通过仿真确定最佳检测参数组合;其次运用自动化扫描装置完成全域数据采集,如航空发动机叶片检测采用六轴机器人搭载阵列传感器,单件检测效率提升3.8倍;数据处理环节引入联邦学习框架,在确保军工数据安全前提下实现多基地检测数据联合建模;最终通过区块链技术实现检测报告的全流程溯源,该模式已在中国航发某型号涡轮盘检测中成功应用,使批次质量问题追溯时间由72小时缩短至4小时。
行业典型应用场景解析
在卫星复合材料舱体检测中,项目团队采用激光散斑干涉法结合声发射监测,成功捕捉到0.2mm级的微裂纹扩展信号,为某型遥感卫星减重15%提供数据支撑。针对火工品装药结构检测难题,研发的微焦点CT系统分辨率达到5μm,在航天科工某固体火箭发动机检测中,精确识别出装药界面0.1mm级脱粘缺陷,避免了重大试验事故。电子组件方面,开发的电磁兼容-机械振动耦合测试平台,已为356家军工单位提供板级可靠性验证,累计发现潜在失效点1.2万余个。
智能化的质量保障生态构建
质量体系通过ISO/IEC 17025和NADCAP双重认证,建立包含23类467项标准方法的数据库。创新引入数字主线的概念,将检测数据与生产MES系统实时交互,在航天科技某型号贮箱生产线实现"检测-工艺"闭环优化,使焊缝一次合格率从92.4%提升至97.6%。人员资质方面,实施ASTM E3179标准的Ⅲ级检测师培养计划,配合AR远程辅助系统,使复杂构件检测误判率降低63%。设备管理采用量子计量标准,关键量值溯源至国家时间频率基准,确保测量不确定度控制在0.5μm以内。
随着新材料、新工艺的快速迭代,建议从三方面加强能力建设:着力开发面向增材制造件的在线监测技术,突破层间缺陷实时检测瓶颈;建立覆盖"材料-构件-系统"的全链条数字检测孪生体,实现服役性能预测;推动检测标准与AI算法的深度融合,构建具备自进化能力的智能检测云平台。据赛迪智库预测,到2028年智能检测技术在装备制造业的渗透率将达45%,这需要检测机构加快数字化转型,为制造强国战略提供更坚实的技术支撑。
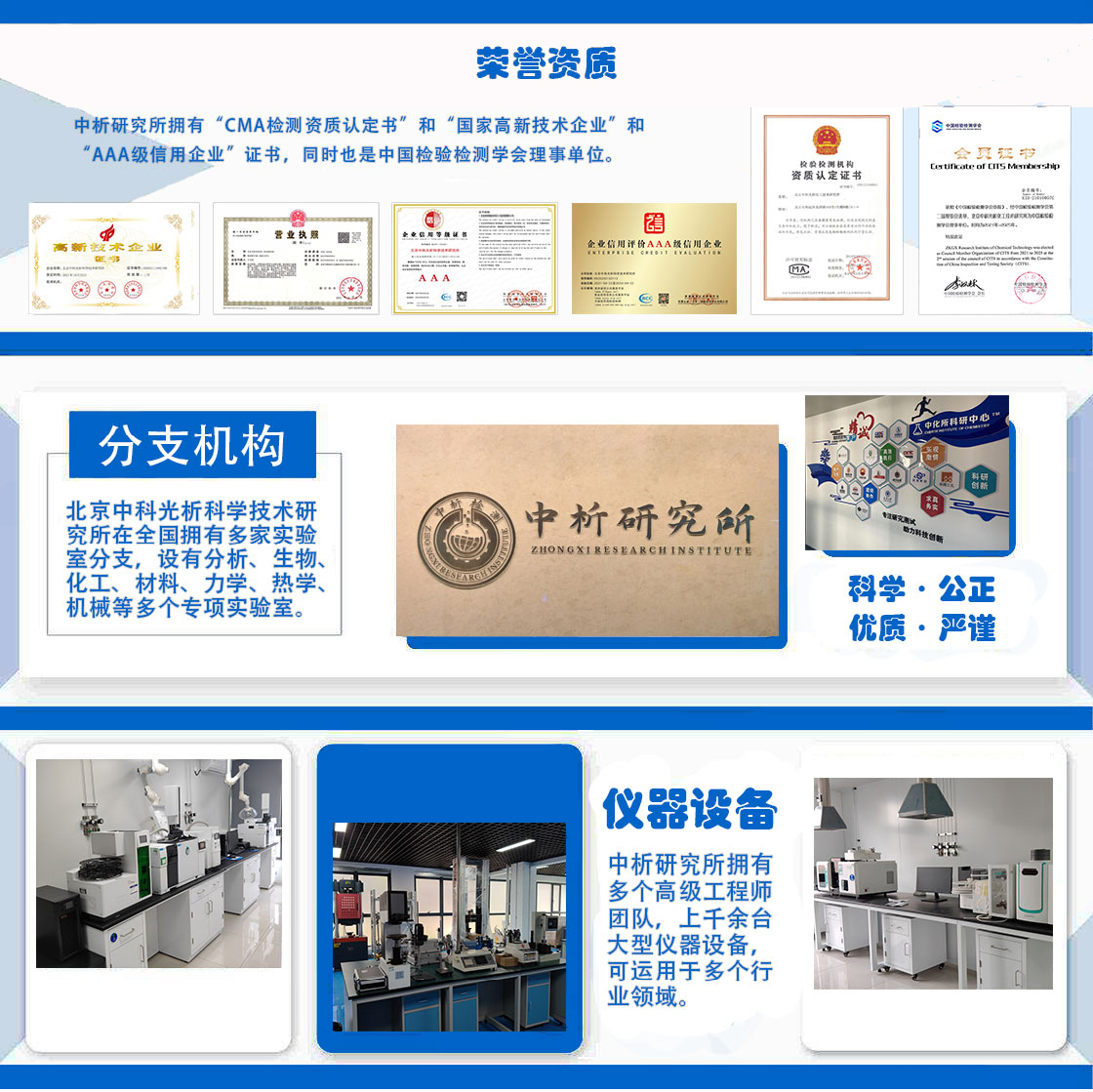
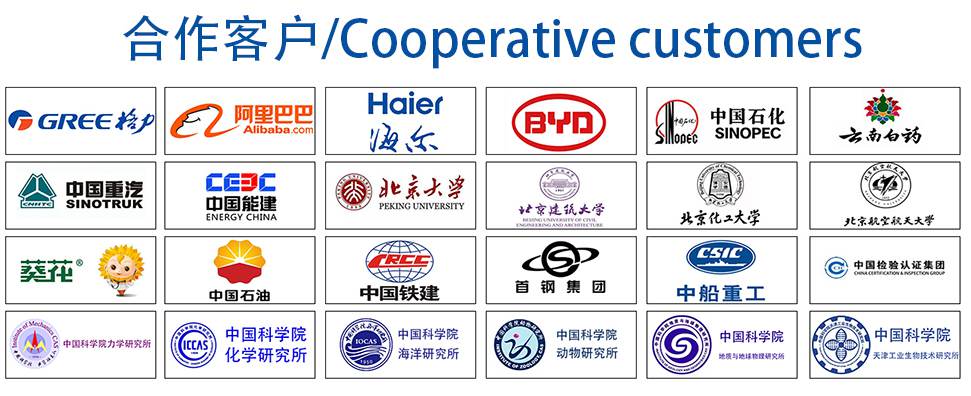