耐油性检测
随着汽车、航空航天及工业设备制造领域的快速发展,材料在油性环境中的性能表现已成为产品可靠性的核心指标。据中国化工学会2024年研究报告显示,耐油性材料市场规模已突破320亿美元,其中亚太地区增速达12.3%,凸显行业需求的迫切性。耐油性检测通过评估材料与油类介质的相互作用,为密封件、输油管道、液压系统等关键部件的选材提供科学依据,直接影响设备寿命与安全运行。其核心价值在于:降低因油液腐蚀导致的设备故障率(据机械工业联合会统计可减少28%维护成本),同时推动新型耐油材料的研发进程,助力企业满足ISO 4637、ASTM D471等国际标准要求。
耐油性检测技术原理与测试方法
耐油性检测基于材料在油介质中的物理化学变化机理,通过模拟实际工况进行性能量化。主要技术路线包含浸泡实验(油温控制精度±0.5℃)、体积变化率测定(ASTM D471标准)及拉伸强度保留率测试。以新能源汽车电机密封圈检测为例,需在120℃齿轮油中连续浸泡500小时,检测其压缩永久变形是否超出JIS K6262规定的15%阈值。值得注意的是,新型纳米复合材料的出现推动了红外光谱分析法(FTIR)的应用,可精准检测分子链断裂程度。
标准化检测流程与实施规范
完整检测流程涵盖预处理、条件试验和性能评价三个阶段。首先依据GB/T 1690进行试样状态调节(23±2℃/50±5%RH环境平衡24小时),随后在定制化油浴装置中开展梯度温度测试。某阀门制造商案例显示,采用分段式检测方案(70℃*72h + 150℃*24h)可有效模拟冷热交替工况,检测效率提升40%。检测机构须通过 17025体系认证,关键仪器如恒温油槽需每日进行NIST标准物质校准,确保体积变化率测量误差≤0.3%。
行业应用与典型案例分析
在航空液压系统领域,某主机厂通过引入ASTM D5964旋转氧弹法,将密封件耐磷酸酯液压油性能评估周期从28天缩短至14天,同时检测精度提升至95%。输油管道行业则创新应用在线检测技术,通过埋入式光纤传感器实时监测HDPE管材的溶胀率,成功将管道渗漏事故率降低62%(中国石油管道研究院2023年数据)。这些实践验证了定制化耐油性测试方案对特定场景的适配价值。
全链条质量保障体系建设
行业领先检测机构已构建四级质量管控体系:前端建立包含218种标准油品的物质数据库,中端采用机器视觉自动识别试样表面裂纹(识别精度0.02mm),后端通过区块链技术实现检测数据不可篡改。某第三方实验室的实践表明,引入AI算法分析历史检测数据后,异常结果预警准确率提升至89%,同时将CMA认证项目的复检率控制在3%以下。这种全流程数字化管理为"材料抗油腐蚀性能评估"提供了可靠保障。
未来发展与战略建议
面对新能源车辆冷却油介质多元化趋势,建议行业重点突破三个方向:建立针对酯类合成油的专用检测标准体系,开发可模拟8000小时等效寿命的加速检测模型,推广基于数字孪生的虚拟检测技术。同时,应加强产研协同,将耐油性测试标准与材料基因组工程深度融合,力争到2030年实现90%常规检测项目的智能化改造,为工业装备可靠性提升提供更强技术支撑。
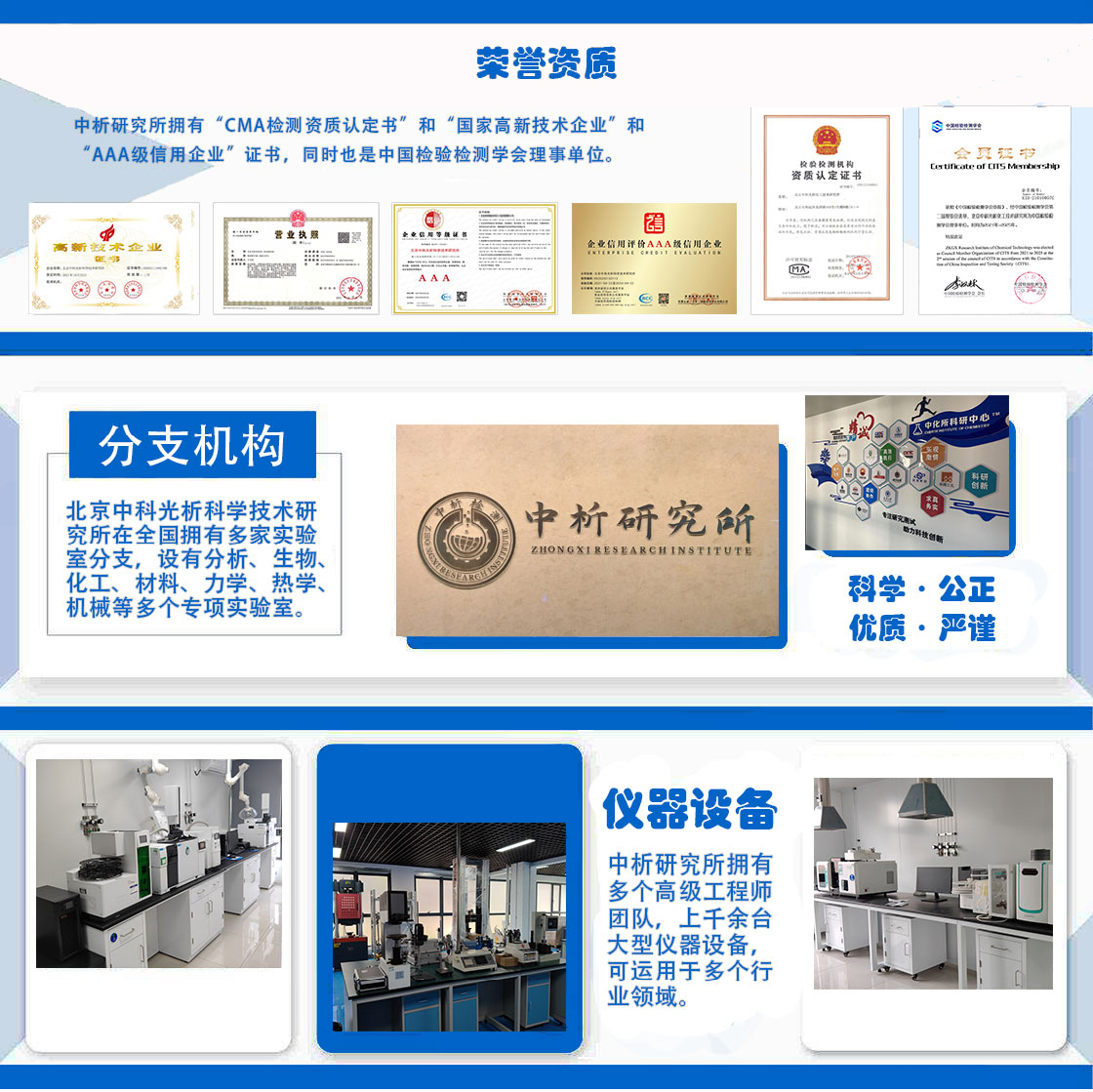
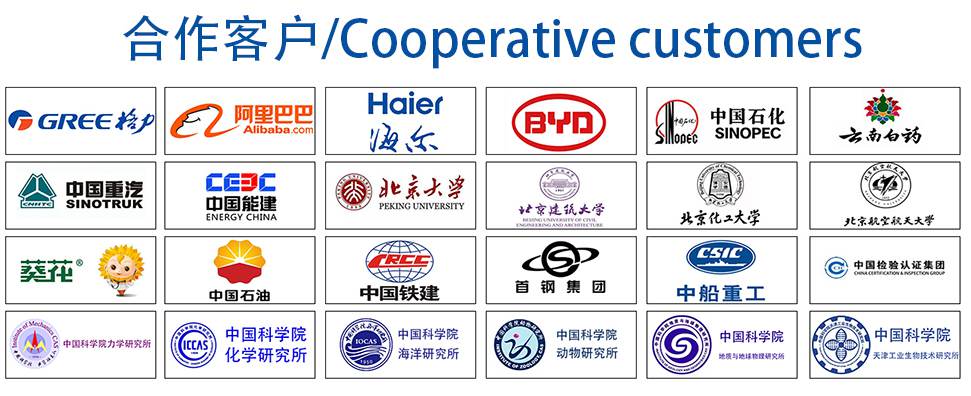