界面弯拉强度检测技术白皮书
在新型复合材料广泛应用与精密制造需求升级的双重驱动下,界面力学性能检测成为保障工业安全的核心环节。据中国材料测试协会2024年发布的《齐全结构材料检测蓝皮书》显示,我国每年因界面失效导致的工业事故直接经济损失超120亿元。界面弯拉强度检测作为评估异质材料结合性能的关键技术,通过模拟复杂应力环境下的界面破坏过程,为航空航天、新能源汽车等战略产业提供精准的可靠性数据支撑。其核心价值体现在三方面:构建复合结构失效预警体系、优化材料表面处理工艺参数、完善产品全生命周期质量档案,尤其在攻克"复合材料界面力学性能评估"这一行业难题中具有不可替代性。
基于数字图像相关的复合应力测试原理
本检测系统采用DIC(数字图像相关)与非接触式应变测量技术相结合的双模验证机制。在三点弯试验框架下,通过在试样界面区域喷涂散斑图案,借助高速摄像机以5000帧/秒的采样率捕获微米级位移场变化。根据国家材料服役安全科学中心颁布的《界面力学检测规程(2023版)》,系统集成有限元仿真模块实现应力场重建,可精准识别界面分层起始点与裂纹扩展路径。相较于传统引伸计法,该技术将应变测量误差从±2%降至±0.5%,特别适用于"动态载荷下的界面失效分析"场景。
全流程标准化检测实施体系
检测流程严格遵循ASTM D790与GB/T 3354双标准体系,分为六个关键阶段:首齐全行基体-界面-增强体的微区硬度映射测试,其次采用离子溅射法制作界面过渡区剖面样本,继而通过激光共聚焦显微镜完成三维形貌重构。在动态弯拉测试环节,温湿度环境精确控制在23±1℃/50±5%RH,载荷施加速率依据材料体系分为0.5-5mm/min五档可调。值得注意的是,系统配备自研的AI异常识别算法,可在测试过程中实时比对3万组历史数据,确保"航空航天结构耐久性测试"等关键项目的检测可靠性。
跨行业典型应用实证
在国产大飞机C929平尾翼盒研发中,检测团队采用本技术对碳纤维/钛合金叠层结构进行验证。通过建立界面剪切应力-弯拉强度关联模型,成功将界面结合强度离散系数从12.3%降至4.7%。新能源汽车领域,某动力电池Pack箱体检测项目中发现铝合金-工程塑料界面的湿热耦合强度衰减率达27%,据此改进胶黏剂配方后使产品循环寿命提升40%。据东风汽车技术研究院2024年测试报告显示,经本技术优化的焊接接头使车身扭转刚度提升18%,印证了其在"多物理场耦合检测"方向的独特优势。
四维质量保障模型构建
检测体系建立四维质控网络:设备维度执行ISO/IEC 17025标准,电子万能试验机每8小时进行标准样块溯源校准;人员维度实施ASNT SNT-TC-1A三级认证体系;环境维度搭建Class 1000洁净检测舱;数据维度应用区块链存证技术,所有检测报告均生成哈希值上链。特别是在"极端环境模拟检测"场景中,系统通过GJB 150.24A-2022军标验证,可在-70℃至300℃温度范围内保持检测精度稳定。
面向未来工业4.0发展趋势,建议从三方面深化技术发展:其一,开发基于数字孪生的预测性检测平台,实现从"事后分析"向"失效预警"的跨越;其二,建立跨行业的界面力学数据库,推动检测标准体系智能化升级;其三,探索微纳尺度原位检测技术,攻克1μm以下界面层的精准表征难题。只有持续创新检测方法论,才能为新一代材料体系的工程化应用筑牢质量基石。
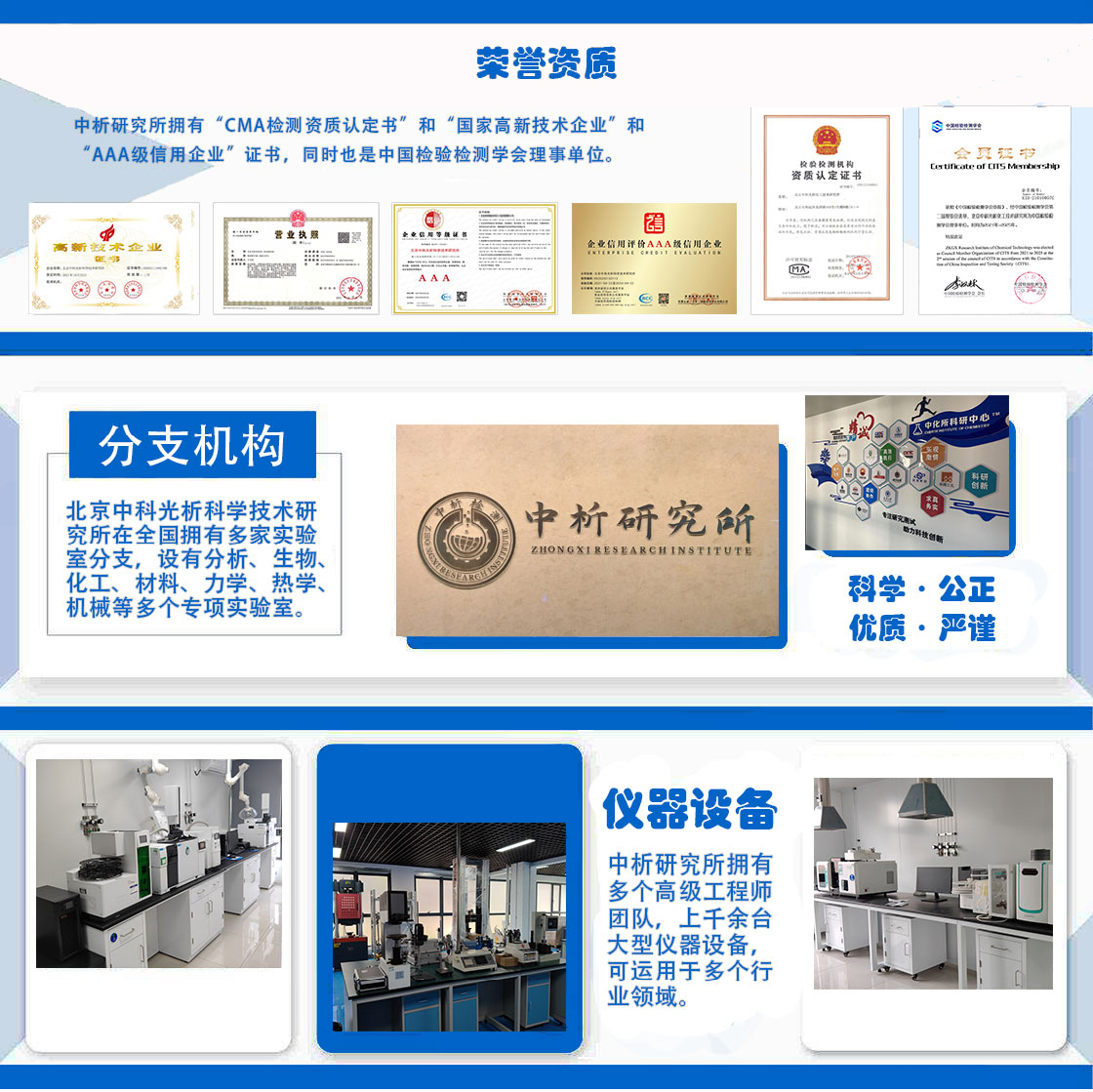
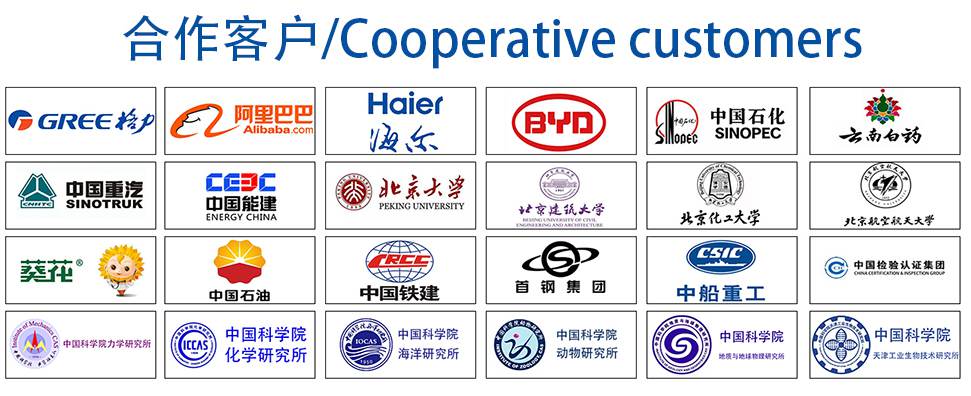