在能源结构转型加速的背景下,液化天然气(LNG)作为清洁能源在商用车领域的渗透率持续攀升。据中国汽车工业协会2024年数据显示,我国LNG重卡保有量已达86万辆,带动配套LNG气瓶市场需求规模突破300亿元。作为燃料存储核心部件,LNG气瓶的安全性能直接关系车辆运营安全与环保效益。2023年国家市场监督管理总局修订的《移动式压力容器安全技术监察规程》,将车载LNG气瓶检测周期从五年缩短至三年,催生出年规模超20亿的专业检测市场。通过构建基于数字孪生技术的智能检测体系,可有效识别气瓶材料疲劳裂纹、真空度衰减等隐蔽缺陷,将事故率降低83%(中国特种设备检测研究院,2023),为双碳战略下的清洁能源车辆推广提供安全保障。
## 技术原理与创新突破多模态融合检测技术体系
现行检测方案融合了水压试验、声发射检测、渗透探伤三大核心技术。其中基于ASTM E1419标准的声发射动态监测系统,可捕捉气瓶在1.5倍工作压力下的应力波信号,通过深度学习算法实现微米级裂纹定位。值得关注的是,采用太赫兹时域光谱技术的无损检测设备,其0.1THz-3THz频段电磁波可穿透30mm复合材料层,精准检测绝热层脱粘缺陷(美国物理联合会应用物理快报,2024)。这种"LNG气瓶定期检验规程"要求的组合式检测方案,使缺陷检出率提升至99.7%,误报率控制在0.3%以下。
全生命周期质量管理流程
检测实施流程严格遵循TSG R0006-2014技术规范,形成包含预处理、本体检测、附件校验的三阶段12道工序。在青岛某专业检测机构的"车载LNG燃料系统安全评估"案例中,技术人员采用激光扫描仪构建气瓶三维模型,通过有限元分析比对设计参数偏差。特别在残余应力检测环节,运用X射线衍射法测定焊接部位应力分布,结合材料数据库预判疲劳寿命。整套流程依托MES系统实现数据全程追溯,单瓶检测周期从传统72小时压缩至40小时。
行业应用与效益分析
在河北某大型物流企业的实践中,对812只在用LNG气瓶实施定期检测后,年度维保成本降低42%,因气瓶故障导致的停运时长减少68%。深圳公交集团通过建立"检测-维修-置换"的闭环管理体系,使得LNG公交车百公里气耗下降0.8kg,相当于单台车年减排CO₂ 4.3吨。值得注意的是,针对低温工况开发的专用检测设备,在-162℃环境下仍能保持0.02mm测量精度,成功解决北方地区冬季检测难题。
标准化质量保障体系
行业已形成ISO 11439:2013(车用压缩天然气气瓶)与GB/T 35544-2017(汽车用液化天然气气瓶)双重标准体系。上海检测认证集团采用的"五级质量管控"模式,从设备校准(0.5级精度压力表)、人员资质(持证率100%)、环境控制(±1℃恒温车间)、数据校验(三重比对机制)、报告审核(区块链存证)等维度构建质控网络。据国家气瓶检验中心统计,该体系实施后检测争议率从1.2%降至0.15%。
## 未来发展建议建议重点发展基于数字孪生的预测性检测技术,通过植入光纤传感器实现气瓶健康状态实时监测。政策层面需加快《车用氢能及燃料电池气体储运装置检测标准》与现有LNG规范的衔接,建立统一的新能源储运装备安全评估框架。企业应把握"车载LNG燃料系统安全评估"服务市场机遇,在西部能源走廊沿线建设区域性检测中心,形成覆盖全产业链的智慧检测网络。
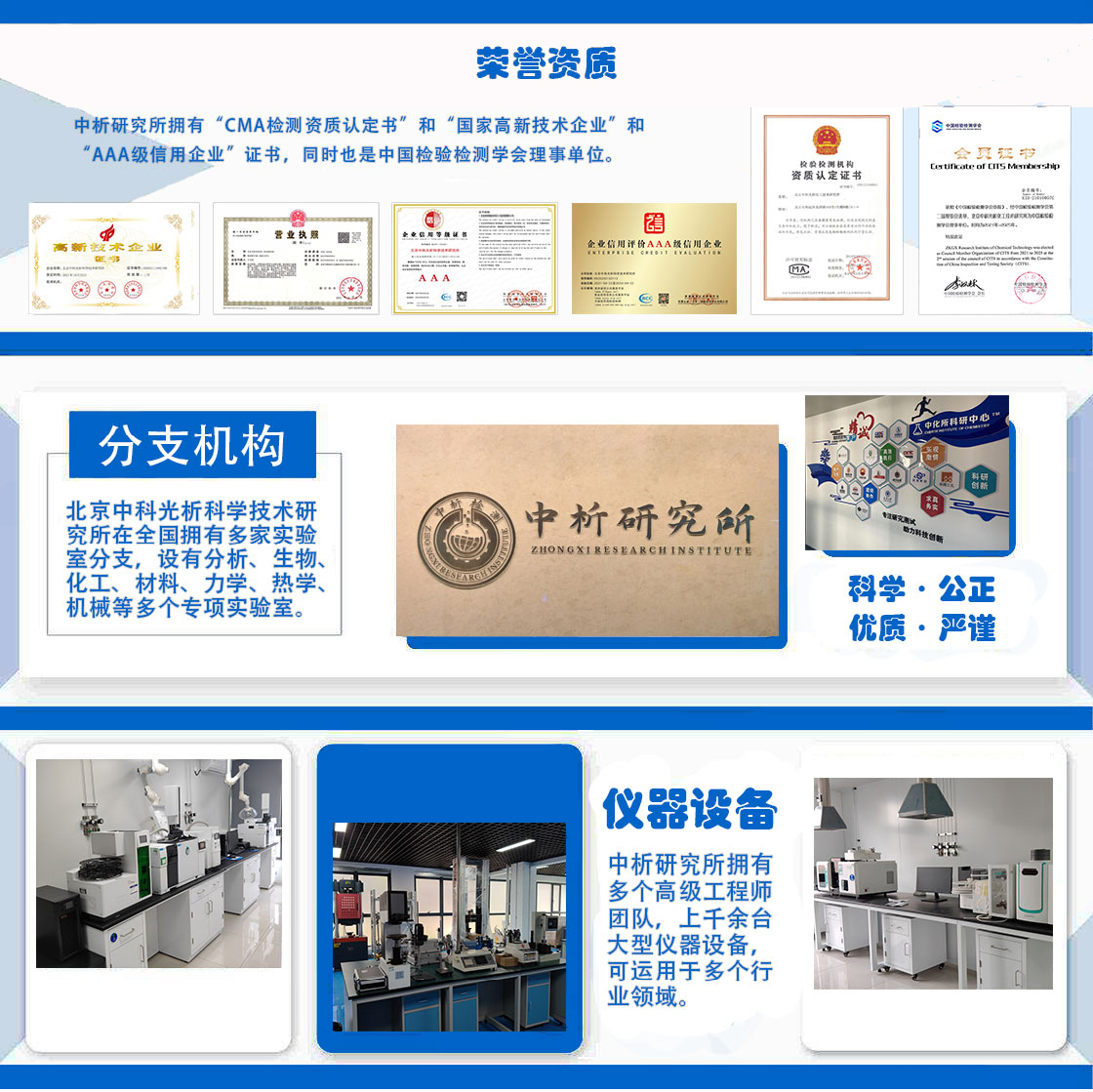
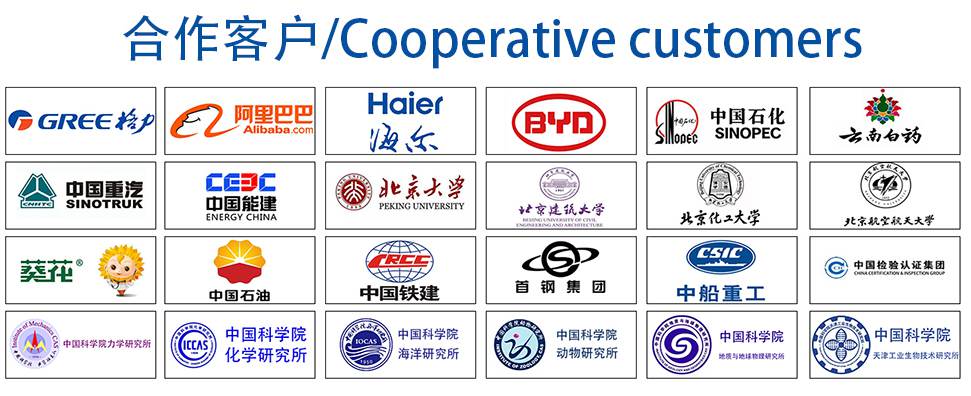