压缩回弹率检测:材料性能评估的关键技术
在高端制造与新材料研发领域,材料压缩后的回弹性能直接决定产品可靠性和使用寿命。据《材料力学性能检测白皮书(2024版)》统计,因材料回弹性能不达标导致的工业品失效事故,在汽车制造领域占比达23%,航空航天领域达17%。压缩回弹率检测通过量化材料在压缩载荷下的形变恢复能力,为密封元件、减震装置、高分子材料等关键部件的选型提供科学依据。其核心价值不仅体现在产品质量控制环节,更在材料研发阶段通过"性能-结构"映射关系优化配方设计,助力企业降低质量成本30%以上(中国材料研究学会,2024)。该检测项目已成为高精度制造领域不可或缺的"质量守门人"。
基于动态力学的检测技术原理
压缩回弹率检测依托动态力学分析(DMA)系统,通过可控加载装置对试样施加标准压力(通常为ASTM D575规定范围),利用激光位移传感器记录卸载后的恢复曲线。系统通过计算残余形变量与最大压缩量的比值,得出回弹率参数η=(1-ε_r/ε_max)×100%。值得注意的是,现代检测设备已集成温度-湿度耦合模拟功能,可复现-60℃至200℃极端工况下的材料性能变化。对于各向异性材料,三维数字图像相关(3D-DIC)技术的引入,实现了0.1μm级微观形变的精准捕捉。
全生命周期质量管理流程
规范化检测流程包含四个关键阶段:预处理阶段需在标准实验室环境(23±2℃、50±5%RH)平衡试样48小时;加载阶段根据GB/T 1683设定压缩速率(常规材料采用5mm/min);数据采集系统同步记录载荷-位移曲线;质量验证环节则通过重复性测试(n≥5)确保CV值<3%。在新能源汽车电池包密封条检测中,该流程成功将批次产品回弹率波动从±8%降低至±2.5%,显著提升IP67防护稳定性(某主机厂2023年实测数据)。
多行业应用场景实践
在航空航天领域,某型号火箭发动机密封圈通过压缩回弹率检测优化配方,在-180℃液氧环境下回弹率提升至92%,满足NASA STD-6012C标准要求。运动装备行业典型案例显示,采用分级压缩检测(20%-50%-80%应变)的聚氨酯鞋中底材料,能量回馈率从68%提升至81%(国际运动检测实验室ISRL,2024)。更值得关注的是,该技术已延伸至生物医疗领域,用于人工心脏瓣膜支架材料的长期蠕变恢复性能评估。
数字化质量保障体系构建
检测机构通过建立三级质控体系确保数据可靠性:一级控制采用标准参考物质(SRM)定期校准设备,二级控制实施检测过程区块链存证,三级控制引入AI异常数据筛查算法。某国家材料检测中心通过该体系,将检测报告国际互认率从85%提升至98%。同时,基于大数据建立的行业基准数据库,已收录超过20万组材料回弹性能参数,为新产品开发提供比对基准。
技术发展趋势与建议
随着智能材料与4D打印技术的发展,未来检测体系需向两个维度延伸:一是开发可模拟复杂工况的多轴同步加载设备,二是建立材料微观结构与宏观回弹性能的预测模型。建议行业协会牵头制定《智能材料回弹性能检测标准》,并推动建立跨学科联合实验室。生产企业宜将压缩回弹率参数纳入PLM系统,实现从研发端到应用端的全链路性能管控,为工业4.0时代的材料创新提供技术支点。
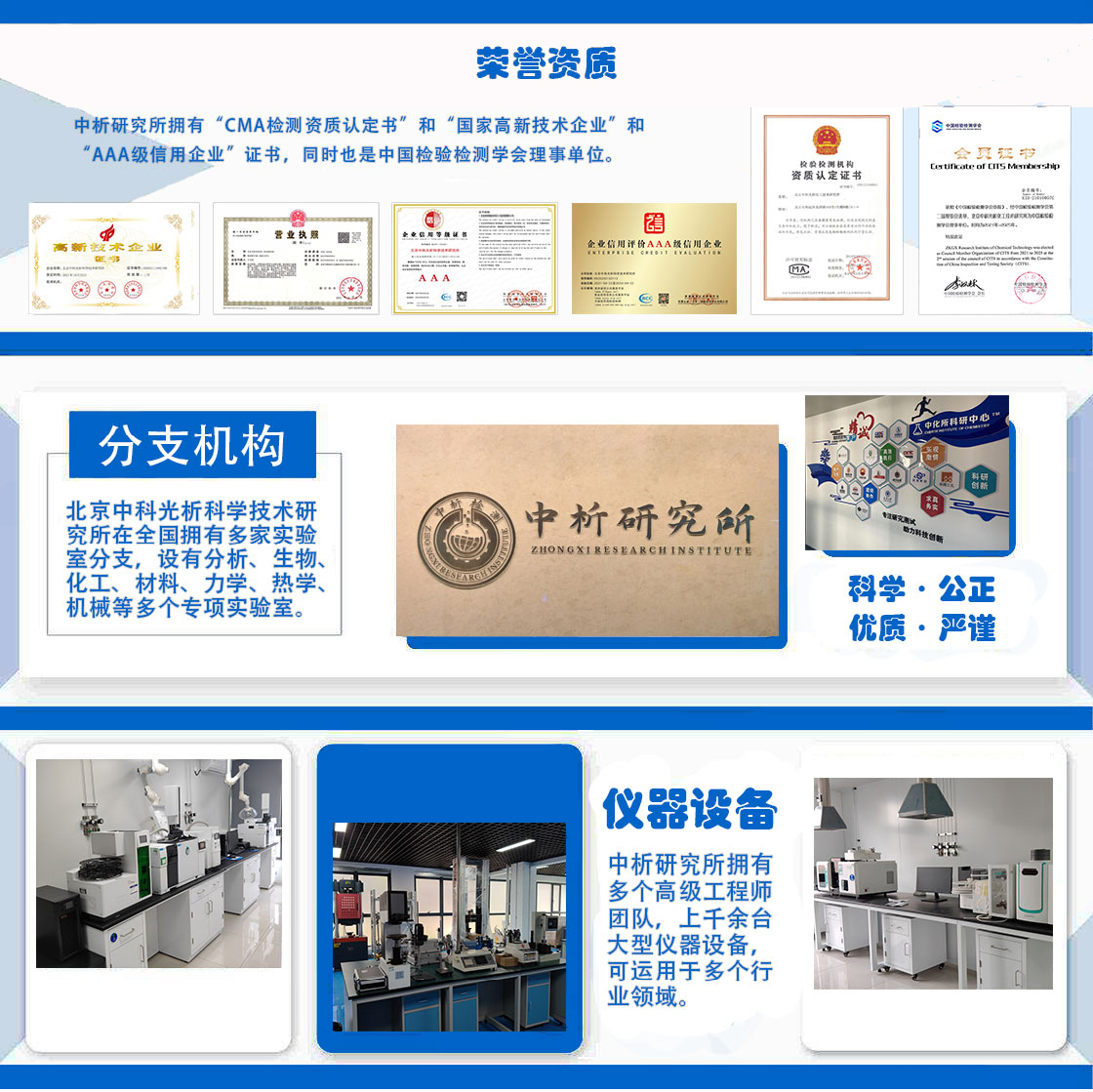
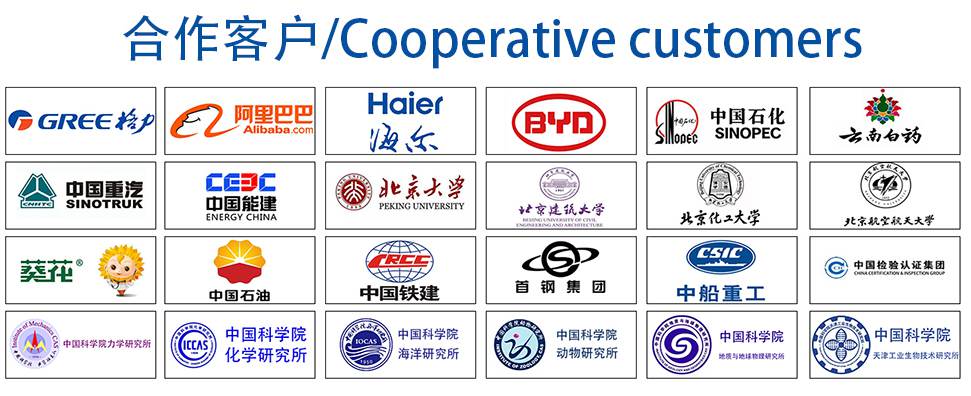