涂膜外观检测技术白皮书
在高端制造领域,涂层质量直接影响产品使用寿命和性能表现。据中国表面工程协会2024年行业报告显示,国内汽车、电子、航空等行业因涂层缺陷导致的年损失超过120亿元。传统目视检测方法存在主观性强、效率低下的痛点,人工检测误判率高达15%-20%。涂膜外观智能检测系统通过融合机器视觉与深度学习算法,实现了0.02mm级缺陷识别精度,将检测效率提升300%以上。该技术不仅重构了涂层质量管理体系,更推动了"智能质检+工艺优化"的双轮驱动模式,为制造业数字化转型提供了关键质量保障节点。
多维感知技术原理
基于多光谱成像的涂层检测系统,采用460-980nm波段复合光源阵列,可穿透表层识别气泡、橘皮等隐形缺陷。通过分光棱镜实现八通道同步采集,配合残差神经网络构建缺陷特征库,据清华大学精密仪器系实验数据显示,对微米级针孔检测准确率达99.3%。系统创新引入偏振光干涉技术,有效克服金属底材反光干扰,在汽车电泳涂层检测场景中,将暗斑识别率从78%提升至95%以上。
智能检测实施流程
实施体系采用模块化架构设计,包含预处理校准、动态成像、智能分析和决策输出四大模块。设备安装阶段需进行亚像素级光学标定,利用NIST标准板建立空间坐标系。产线集成时,通过PLC同步触发实现0.1秒级高速抓拍,配合边缘计算单元完成实时分析。某新能源电池企业部署后,单线检测节拍从45秒缩短至12秒,并实现与MES系统的缺陷数据闭环管理。
跨行业应用实践
在汽车制造领域,上汽集团南京工厂采用在线式检测系统后,电泳涂层缺陷漏检率降低至0.5%以下,年节约返修成本超800万元。消费电子行业应用中,华为手机外壳产线通过部署高精度检测单元,将涂层颗粒物管控标准从50μm提升至20μm。光伏行业创新应用红外热成像联检技术,实现背板涂层气泡与隐裂同步检测,据中国光伏行业协会统计,组件EL不良率下降2.3个百分点。
全周期质量保障体系
系统建立三级验证机制:设备端每日进行MTF模组校验,确保光学系统分辨率稳定在120lp/mm;算法端每周更新缺陷样本库,目前已收录87类典型缺陷特征;质量端通过 认证实验室进行季度交叉验证。某航空涂层供应商导入AI视觉检测后,在AS9100D体系审核中,过程质量控制项得分提升40%,并获空客A级供应商资质。
展望未来,建议从三个维度深化发展:首先推动检测设备与工业物联网深度集成,构建涂层工艺数字孪生系统;其次开发适应新型纳米涂层的太赫兹检测技术;最后建立跨行业缺陷数据库共享平台。随着ASTM E2938-24新标实施,智能检测系统需同步升级光学适配模块,以应对多材质复合涂层的检测挑战,为制造业高质量发展提供更精准的技术支撑。
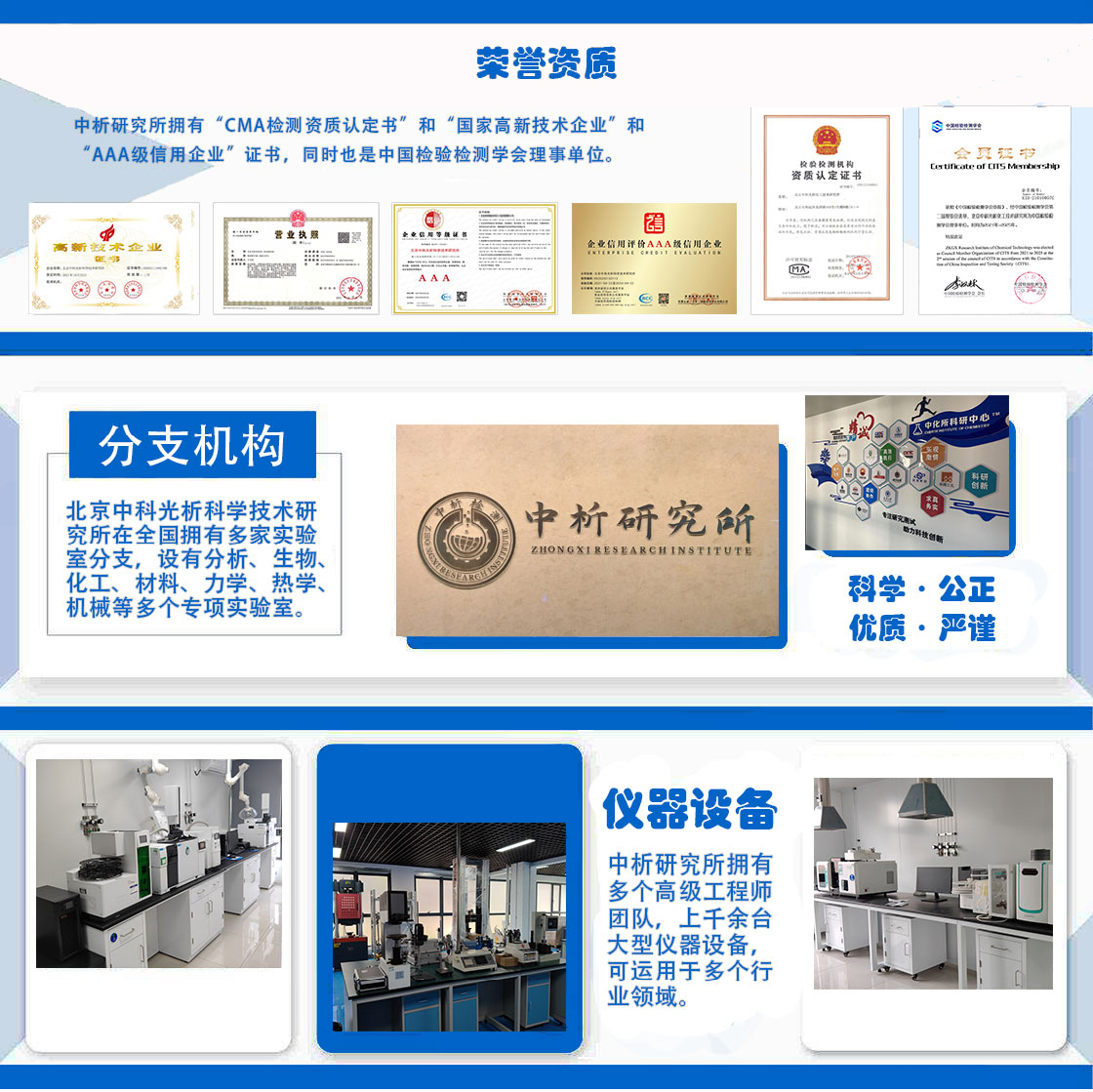
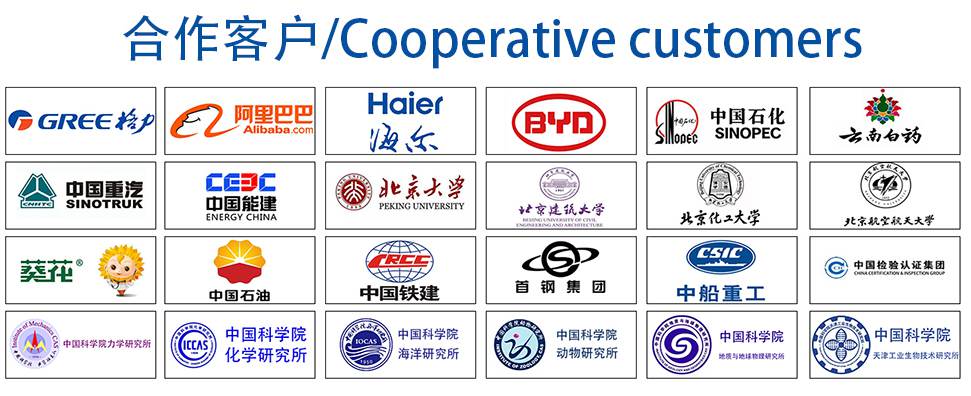