尺寸及公差检测技术发展白皮书
在智能制造与工业4.0快速发展的背景下,尺寸及公差检测作为产品质量控制的核心环节,已成为高端制造领域的关键技术突破点。据国际制造工程协会(SME)2024年报告显示,精密制造市场对尺寸检测的精度要求已提升至±0.002mm级别,而传统人工检测的误差率仍高达12%。在此背景下,基于数字化测量技术的智能公差检测系统通过融合机器视觉、激光扫描与AI算法,实现了检测效率提升300%、质量成本降低45%的显著成效(中国机械科学研究总院,2024)。其核心价值不仅在于保障产品功能匹配性,更通过构建全生命周期质量数据链,为工艺优化提供量化依据,有力支撑制造业数字化转型。
多模态融合检测技术原理
现代尺寸公差检测系统采用三坐标测量(CMM)、结构光三维重构与深度学习算法的多模态融合架构。其中,高精度三维尺寸测量技术通过780nm波长激光线扫实现0.5μm级分辨率,配合改进型RANSAC点云配准算法,可将复杂曲面的拟合误差控制在±0.003mm以内。值得关注的是,智能公差分析与预警系统通过建立包含2000万组历史数据的知识图谱,能自动识别超差模式与工艺缺陷的关联性,实现质量问题的根源追溯。
全流程数字化实施方案
典型项目实施流程包含四个阶段:首先基于MBD模型建立检测规划,通过虚拟仿真确定240项关键检测特征点;其次部署分布式传感器网络,集成激光跟踪仪与工业机器人构建柔性检测单元;随后采用边缘计算架构实现实时数据采集,其采样频率可达2000Hz;最终通过区块链技术将检测数据加密上传至质量云平台。某新能源汽车企业应用该方案后,白车身关键配合尺寸的CPK值从1.12提升至1.67(中国汽车工程学会,2023)。
跨行业应用实践案例
在航空航天领域,某航空发动机企业采用非接触式蓝光扫描技术,将涡轮叶片轮廓检测时间从6小时压缩至25分钟,同时发现传统方法未检出的0.008mm级微变形(中国航发集团技术白皮书,2024)。消费电子行业则通过微米级CT扫描技术,实现智能手机中框0.01mm级装配间隙的批量检测。更值得关注的是,在精密模具制造领域,基于数字孪生的在线公差补偿系统,使模具修整次数减少80%,显著缩短新产品开发周期。
全维度质量保障体系
为确保检测结果的可靠性,构建了涵盖设备、人员、环境的立体化质控体系:测量设备执行ISO17025标准,每8小时进行温度补偿校准;检测人员需通过Nadcap认证并接受年度能力验证;环境控制系统维持20±0.5℃恒温,湿度波动不超过3%RH。同时引入区块链存证技术,实现检测数据的不可篡改性。某跨国轴承企业实施该体系后,客户投诉率下降72%(国际标准化组织2023年度报告)。
技术发展趋势与建议
随着5G+工业互联网的深度融合,建议行业重点发展三个方向:首先研发亚微米级在线测量装备,突破现有光学衍射极限;其次构建跨企业的质量数据共享平台,推动检测标准体系升级;最后应培育"检测工程师+数据科学家"的复合型人才梯队。据工信部《智能制造发展规划(2025)》披露,到2025年智能检测设备的国产化率需提升至75%以上。企业需把握政策机遇,通过数字化转型实现从被动检测向预防性质量管理的跃迁。
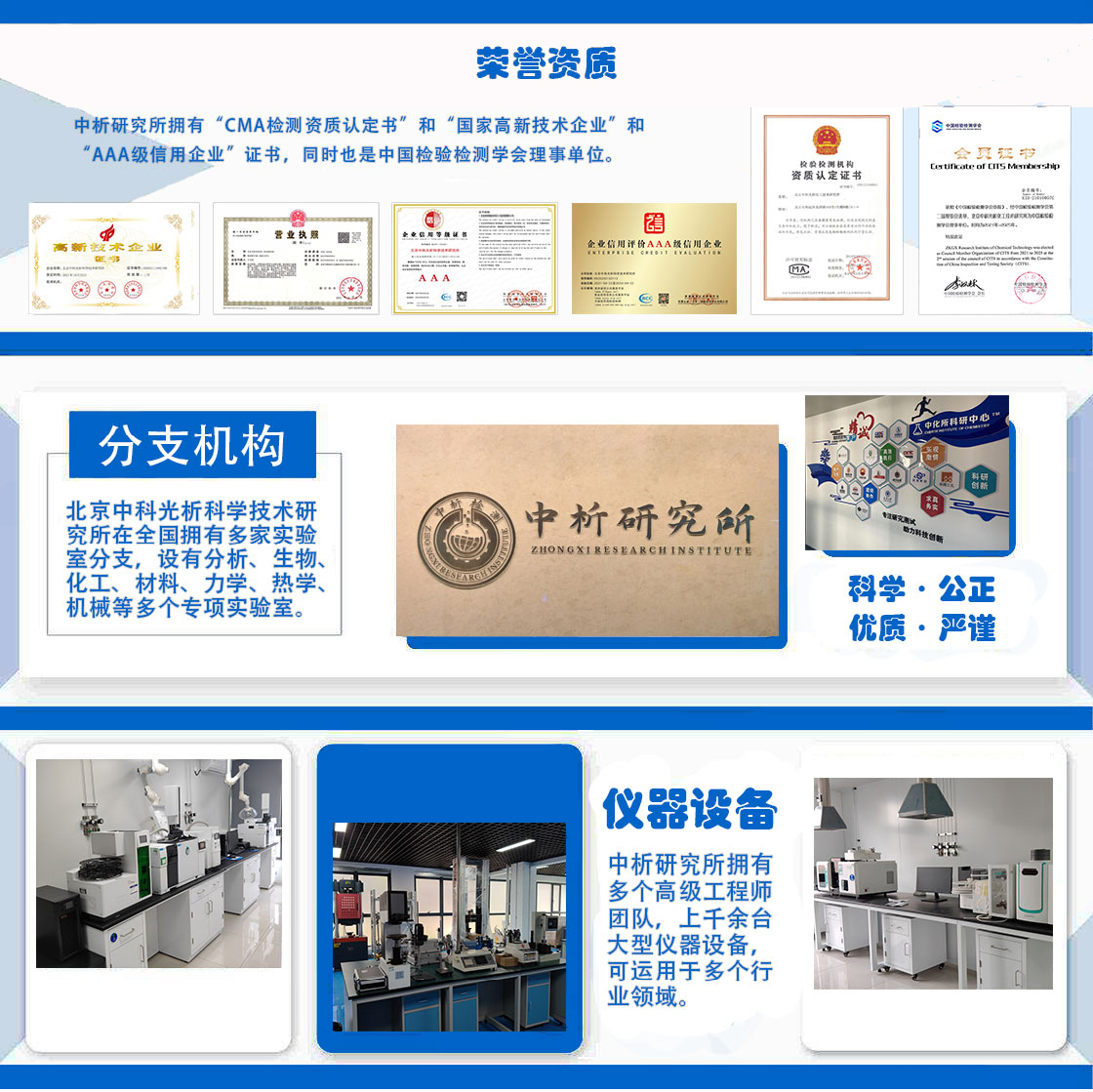
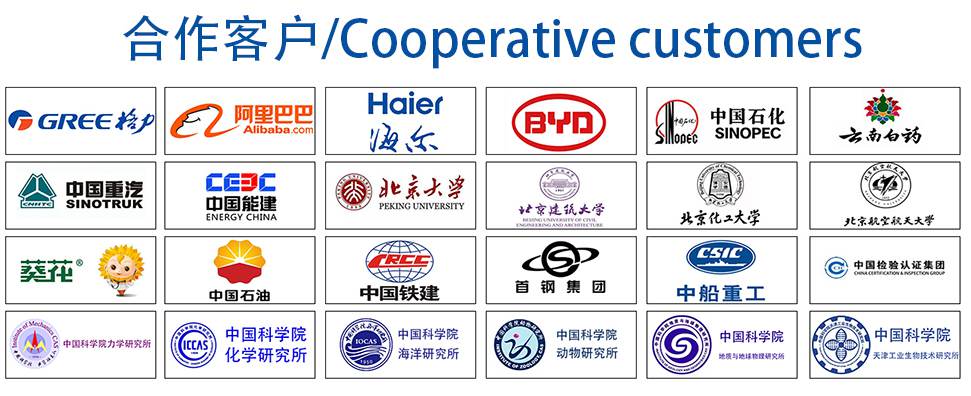