基于应变控制的检测技术原理
现代拉伸检测系统采用三级闭环控制架构,通过载荷传感器(精度±0.5%)、高分辨率引伸计(分辨率1μm)与伺服电机的协同作业,实现真实应力-应变曲线采集。美国材料试验协会ASTM E8标准规定,对于厚度≤3mm的金属薄板,测试速度须控制在0.015-0.15mm/s区间,确保塑性变形阶段数据有效性。通过数字图像相关法(DIC)的引入,系统可捕捉试样表面0.01%级别的微应变分布,有效识别"颈缩效应"前的材料各向异性特征。
全流程标准化实施体系
检测流程严格遵循ISO 6892-1:2019国际标准,涵盖试样制备、环境调控、设备校准三大环节。以某航天级钛合金检测为例,需在恒温恒湿实验室(23±1℃,50±5%RH)完成取样,使用线切割机制备5B型哑铃试样,表面粗糙度Ra≤0.8μm。设备预热30分钟后,采用三级砝码标定法验证500kN试验机力值误差<±0.3%。在动态加载阶段,系统同步记录载荷-位移曲线并自动计算断后伸长率,全过程数据经区块链存证确保可追溯。
多行业典型应用场景解析
在新能源汽车领域,某头部电池企业通过开展"高温高湿环境下的拉伸性能测试",发现NCM811电池极耳铜材在85℃/95%RH条件下抗拉强度下降12.7%,据此优化了焊接工艺参数。而对于医用高分子材料,强生医疗采用ASTM D638 IV型试样检测PEEK椎间融合器的拉伸模量,通过2000次循环加载验证其抗蠕变性能,将产品疲劳寿命提升至15年临床使用标准。这些案例印证了检测数据对产品迭代的关键支撑作用。
四维质量保障体系构建
为应对复杂工况检测需求,构建了包含设备、人员、方法、环境的四维质控体系:试验机每年接受 认可实验室的激光干涉仪校准,检测员需通过CSM材料测试工程师认证;针对碳纤维复合材料等特殊材料,开发了应变速率自适应控制算法,将测试重复性误差控制在0.8%以内;实验室配备Class 100洁净度和±0.2℃温控系统,确保生物可吸收镁合金等敏感材料检测数据的稳定性。
## 技术展望与升级路径 面向材料检测智能化转型趋势,建议重点突破三项技术:基于机器学习的断裂模式识别系统,可提升缺陷判定效率40%以上;嵌入式光纤光栅传感器,实现多维应力场实时监测;开发符合ASTM D3039标准的复合材料多轴加载系统,满足航空发动机叶片复杂应力状态检测需求。同时建议建立覆盖全国主要产业集群的材料数据库,通过检测大数据挖掘推动新材料研发周期缩短30%,为制造强国战略提供基础支撑。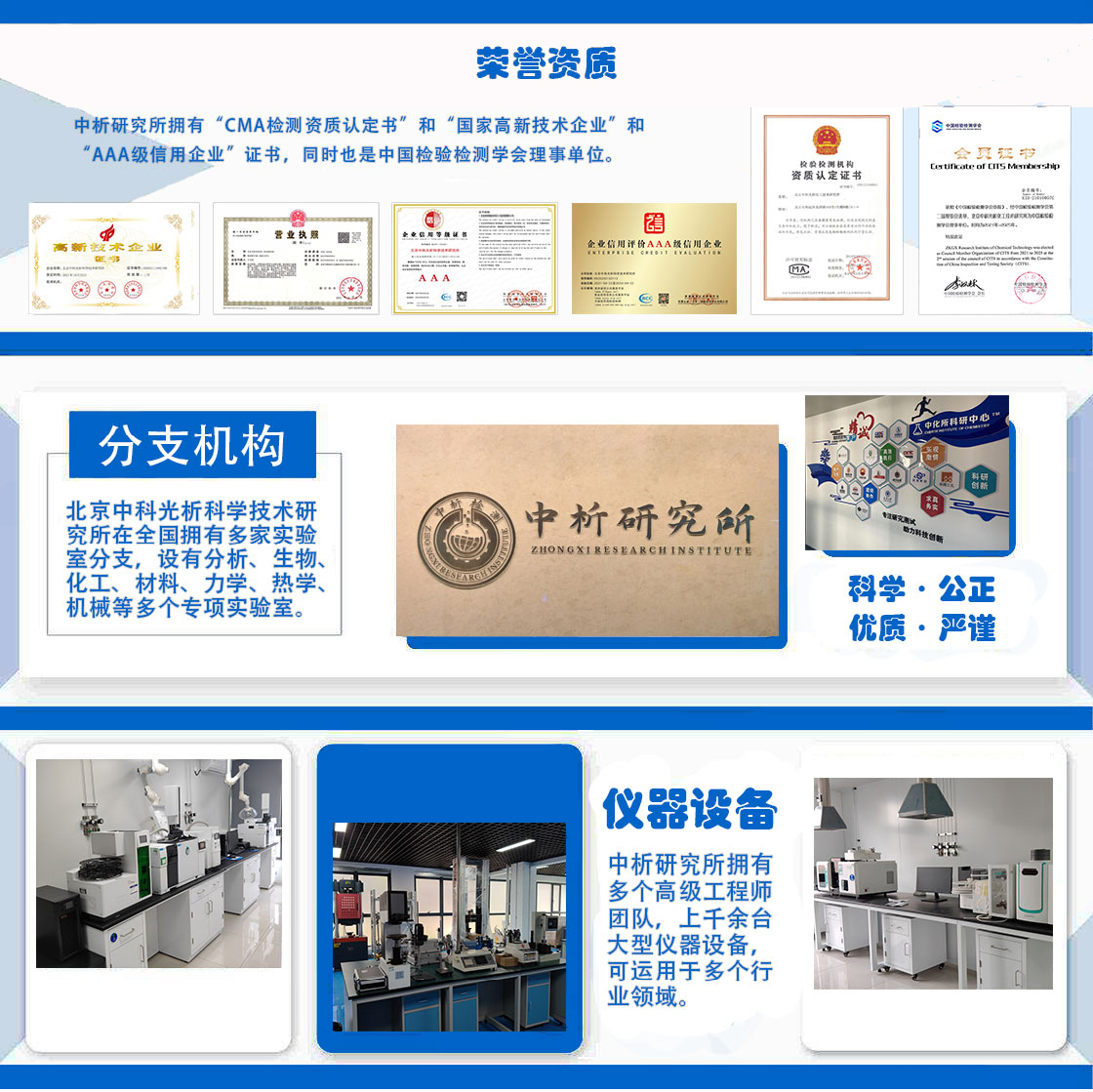
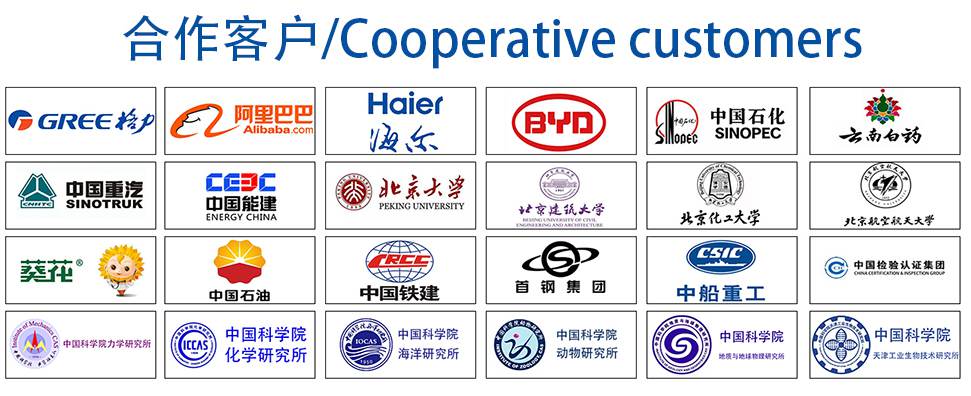